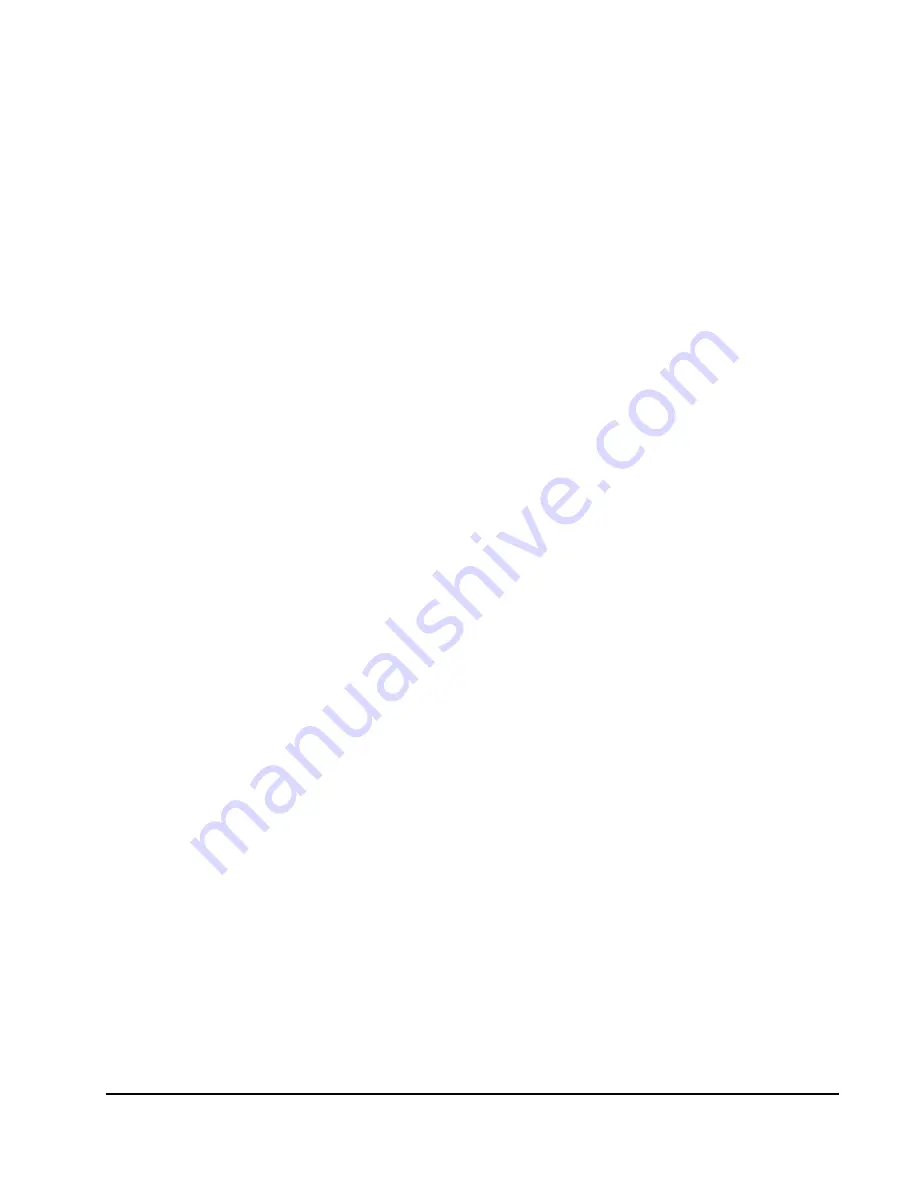
AMI Analyzer Manual
Maintenance and troubleshooting
30
Troubleshooting
Basics of oxygen troubleshooting
Most problems are due to either leaks, or a used-up sensor.
Oxygen is of course present in air at about 3psi partial pressure, and the rate at which it diffuses into a gas
line is only dependent on the difference in the partial pressure between the gas in the line, and in air. Since
there is normally (hopefully) no oxygen in the pipe, that full partial pressure differential drives oxygen into
any leak, no matter what the partial pressure of any other gas may be. Any leak therefore will increase the
oxygen in the sample. This is also true for span gas – a leak at the regulator on a span gas tank can allow
oxygen to flow into the tank, changing its oxygen level and making any spans performed with that gas
incorrect.
Typical life expectancy of a sensor is somewhere between six months and two years, depending on oxygen
levels. If they are exposed to too much oxygen, they will get used up. Always keep the sensor shorted when
it is not in the analyzer. Leave its shorting clip in until you have put it into the cell block, and only then pull
the shorting tab out of the sensor.
If the sensor is deeply frozen (below about 25
º
F), or overheated (above 115°F) the membrane can be
damaged and if so, it will no longer read correctly. This may or may not happen. Also, the sensor can be
poisoned by excessive levels of H
2
S or other poisonous gases. Any of these things will cause the sensor to
read too low.
Reading too high is normally caused by too much oxygen. If you suspect a leak, due to excessive oxygen
readings, you can often get an idea of where it is by changing the sample flow rate. If the oxygen reading
decreases as you increase the flow rate, that is a sure sign of a leak since the intake of oxygen is pretty
constant, but the dilution of that oxygen by the sample is of course greater with a higher flow rate. If you
time how long it takes for the reading to decrease, the distance to the leak source is more or less
proportional to the time it takes to fall. If it goes down immediately, the source is very close to the sensor –
possibly the cell cap is loose, or perhaps an O ring in the analyzer valve is damaged. If it takes a while for the
reading to change, the source is further away. It can be very difficult to pin point the source of the leak, but
don’t give up – the analyzer is essentially a leak detector and it is only doing its job.
Another common problem is a reading that is too low. This is normally due either to a dead sensor, or to an
incorrect calibration. If the span gas is contaminated with oxygen, when you span the analyzer you will turn
the span down too much to make the reading come out to what you thought it should be. It can be hard to
figure this one out: what we suggest when things seem to be confusing is that you perform an air
calibration, and then let the sensor stabilize on the sample gas (or nitrogen); then flow the span gas and see
what the analyzer reads. The sensor and analyzer are in fact very linear, so if the analyzer now says that the
span gas has a lot more oxygen than the label on the tank states, you can be sure that the tank has been
contaminated. If so, you have to replace it, and figure out what the reason for the contamination is. Leak-
check all the possible leak sources. And remember that it is always possible for the gas supplier to make a
mistake. Incidentally, the air calibration is quite accurate, and you can leave it like that with confidence.