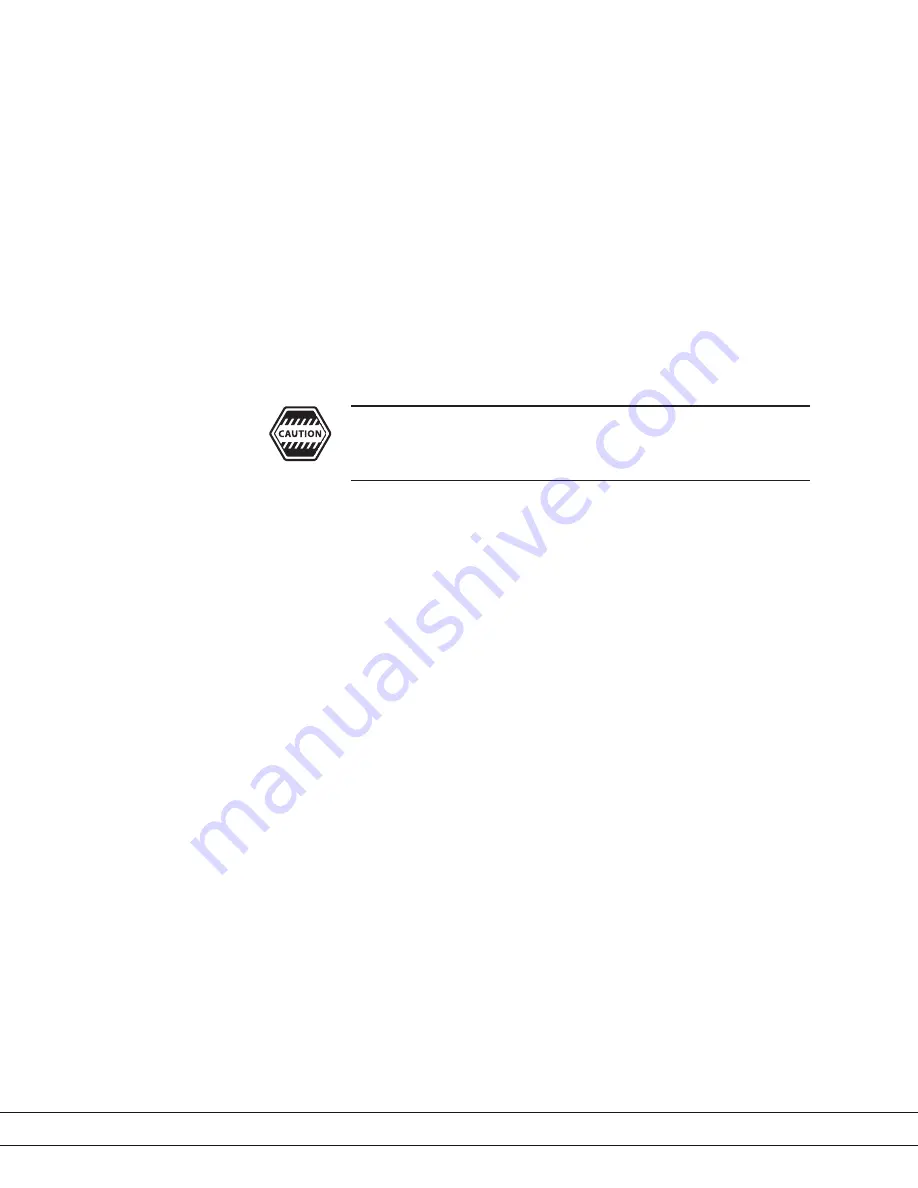
PN 9000-133-VE, Rev U
PRECAUTIONS AUX DOMMAGES DE L’ANALYSEUR
Utilisez une alimentation électrique adéquate
Ne faites pas fonctionner l’analyseur avec une alimentation électrique qui four-
nit plus que la tension électrique spécifiée.
Ne faites pas fonctionner avec les défaillances suspectes
Si vous suspectez que l’analyseur est endommagé, demandez à un technicien
qualifié de l’inspecter.
Mise à la terre CEM (EMC), blindage et protection contre le bruit
Dans un but de compatibilité électromagnétique, en aucune circon-
stance vous ne devez laisser l’écran d’un câble déconnecté en une ou
deux extrémités (unité de contrôle ou de terrain ou autre appareil).
5-6 | Thermox
®
WDG-V / VC / VCM / VM
Summary of Contents for WDG-V
Page 12: ...PN 9000 133 VE Rev U This page intentionally left blank xii Thermox WDG V VC VCM VM...
Page 60: ...PN 9000 133 VE Rev U Figure 2 16 RCU Connections 2 34 Thermox WDG V VC VCM VM...
Page 93: ...PN 9000 133 VE Rev U Figure 3 4 Thermocouple replacement Maintenance and Troubleshooting 3 19...
Page 97: ...PN 9000 133 VE Rev U Figure 3 6 Flow sensor replacement Maintenance and Troubleshooting 3 23...
Page 103: ...PN 9000 133 VE Rev U Figure 3 10 Sensor board removal Maintenance and Troubleshooting 3 29...
Page 124: ...PN 9000 133 VE Rev U This page intentionally left blank 4 10 Thermox WDG V VC VCM VM...