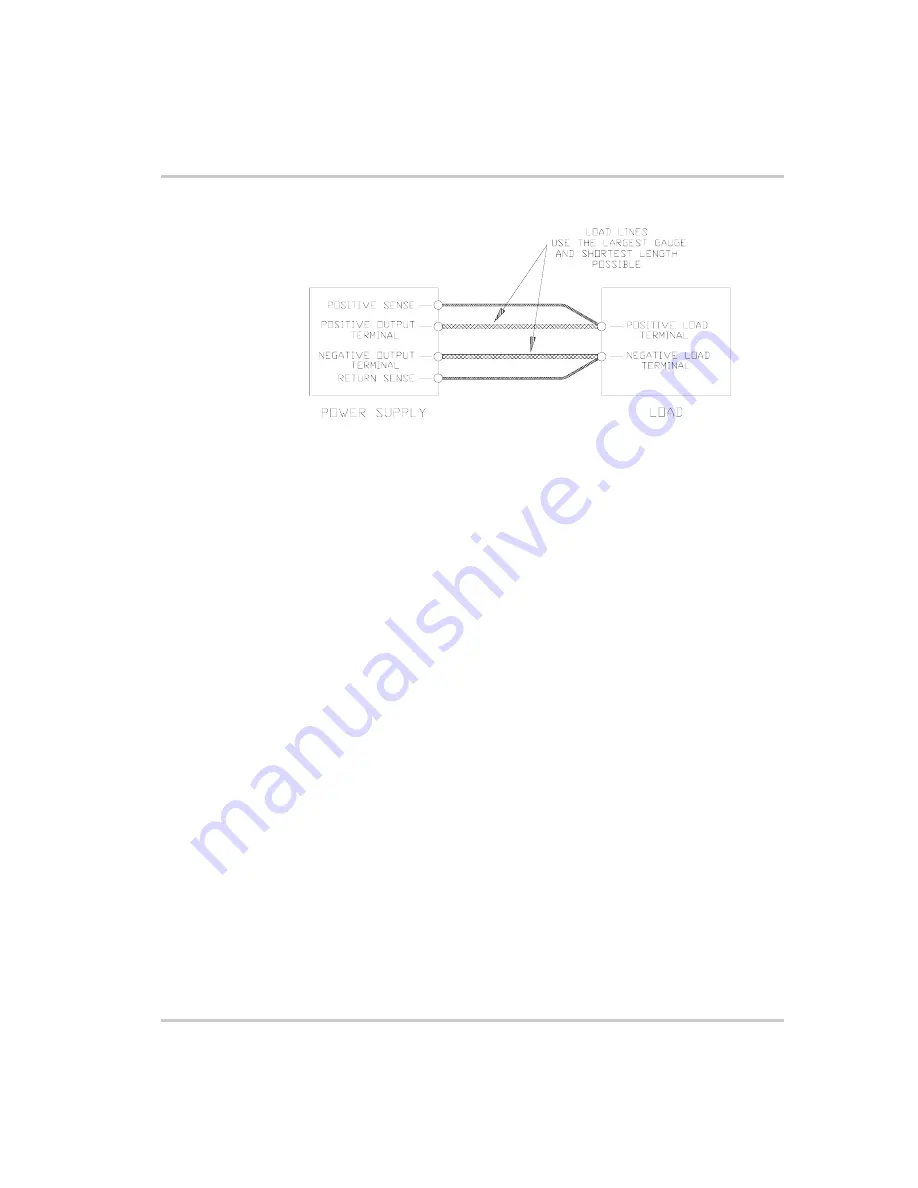
Load Connection
TM-F2OP-C1XN-01
2-19
Connecting Multiple Loads
Proper connection of distributed loads is an important aspect of power
supply use. Two common methods of connection are the parallel power
distribution method and the radial power distribution method.
Parallel Power Distribution
This distribution method involves
connecting leads from the power supply to one load, from that load to the
next load, and so on for each load in the system. This method results in
the voltage at each load depending on the current drawn by the other loads
and allows DC ground loops to develop. Except for low current
applications, we do not recommend using this method.
Radial Power Distribution Method
To connect distributed loads, we
recommend that you use radial power distribution. With this method, you
connect power to each load individually from a single pair of terminals
designated as the positive and negative distribution terminals. These
terminals may be the power supply output terminals, the terminals of one
of the loads, or a distinct set of terminals especially established for
distribution use. Connect the sense leads to these terminals to compensate
for losses and to minimize the effect of one load upon another.
Figure 2-9 and Figure 2-10 show recommended load and sensing
connections for multiple loads. Local sense lines shown are default J10
sense connections. See “Local and Remote Sensing” on page 2–21 for
more information about using remote sensing and grounding the sense
line shield.
Figure 2-8
Single Load with Remote Sensing
Summary of Contents for Sorensen XFR 100-28
Page 3: ...This page intentionally left blank ii...
Page 5: ...This page intentionally left blank iv...
Page 7: ...This page intentionally left blank vi...
Page 13: ...xii...
Page 15: ...xiv...
Page 25: ...1 10...
Page 67: ...3 18...
Page 73: ...Remote Operation 4 6 TM F2OP C1XN 01 Figure 4 1 Connecting Programming Sources to J2 Connector...
Page 75: ...4 8...
Page 87: ...5 12...