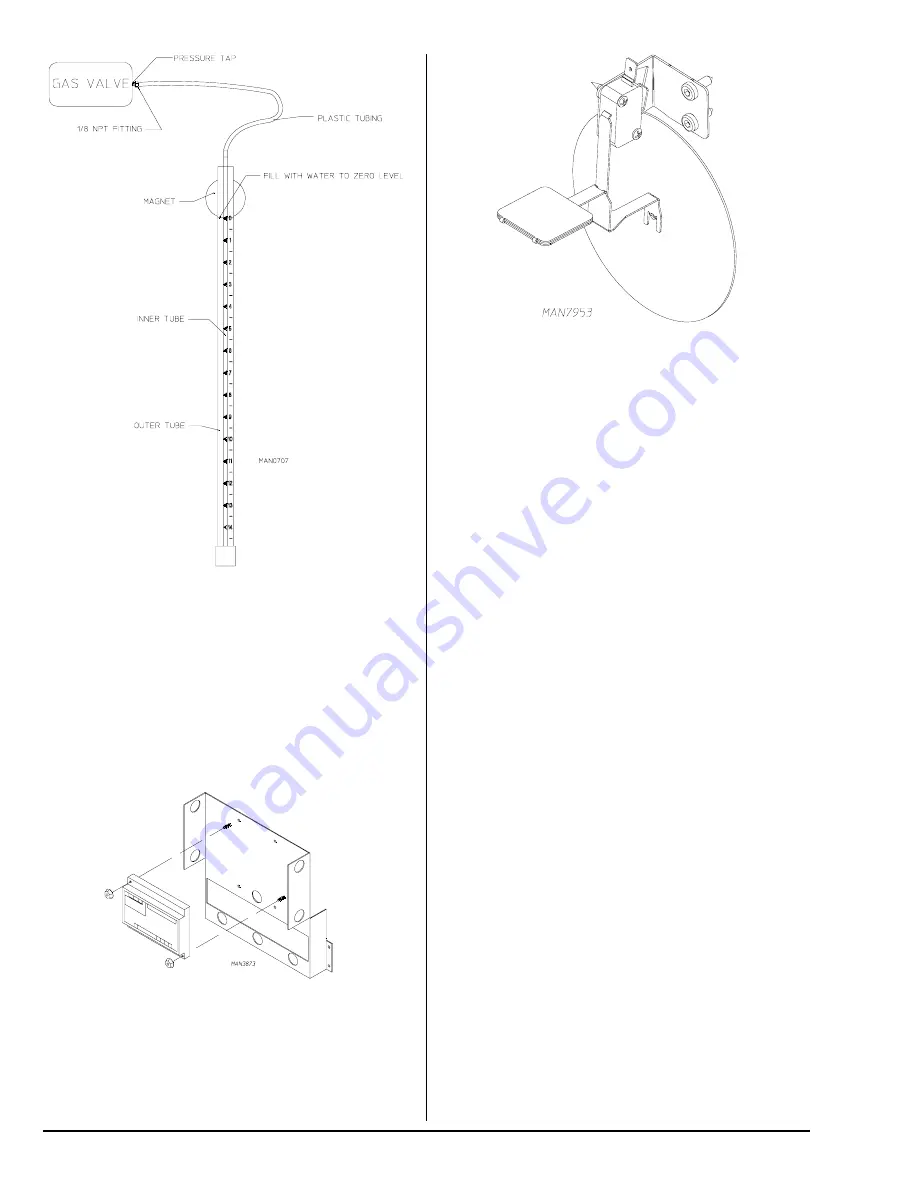
12
American Dryer Corp.
450370 - 2
TO REPLACE DSI MODULE
1. Discontinue power to the dryer.
2. Remove the wires connected to the terminal strip at the
top of the module, and wires connected on the side of the
module.
3. Remove the high voltage wire from the module.
4. Remove the two (2) hex nuts securing the module to the
module mounting bracket.
5. Replace module by reversing process.
TO REPLACE SAIL SWITCH
1. Discontinue power to the dryer.
2. Disconnect the two (2) wires from the switch.
3. Disassemble sail switch from mounting bracket by
removing the two (2) screws securing the switch in place.
4. Reverse this procedure for installing the new sail switch.
Adjust sail switch as described in the next section.
TO ADJUST SAIL SWITCH
1. Operate the installed dryer normally to verify that the heat
system is fully operational.
2. Open the main dryer door.
3. Manually depress the door switch actuator.
4. While continuing to depress the door switch actuator, and
with the door open, start the dryer.
5. If the heat system is not activated in 15-seconds, the sail
switch is properly adjusted.
6. If the heat system is activated, the sail switch is improperly
adjusted and must be readjusted by bending the actuator
arm of the sail switch toward the front of the dryer. If the
actuator arm is bent too far toward the front of the dryer,
the dryer may not have heat when needed. After any
adjustments of the sail switch, the above procedure must
be repeated to verify proper operation.
CAUTION: Do not disable this switch by taping or
screwing sail switch damper to burner. Personal
injury or fire could result.
Front Panel and Main Door Assemblies
TO REPLACE MAIN DOOR SWITCH
1. Discontinue power to the dryer.
2. Open the main door.
3. Remove the two (2) Phillips head screws holding the main
door switch cover in place.
4. Remove the two (2) nuts and washers securing the switch
to the door hinge, and take the switch off the two (2) clinch
studs on the hinge.
5. Disconnect the two (2) wires on the door switch. Connect
the new door switch to those two (2) wires.
6. Reverse this procedure for installing the new door switch.
IMPORTANT:
Under no circumstances should the door
switch be disabled.
TO REPLACE MAIN DOOR ASSEMBLY
1. Remove screws holding main door upper hinge block.
2. Lift and remove door off of lower hinge block.
3. Reverse this procedure for reinstalling the new main door
assembly.