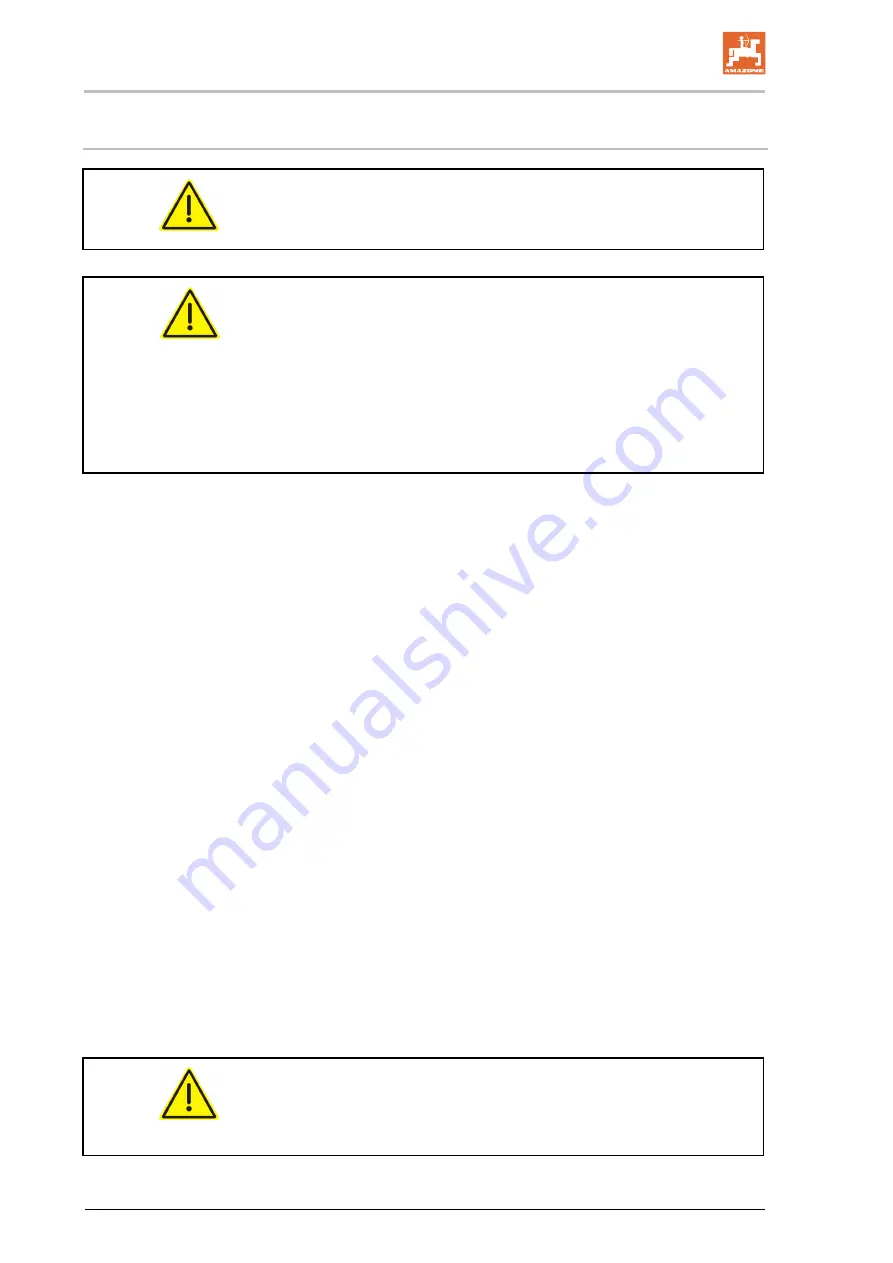
Initial commissioning
76
KG 4/5/6001-2 BAH0060-5 12.17
6.4.1
Adjusting the length of the universal joint shaft to the tractor (specialist
workshop)
WARNING
Only a specialist workshop may make structural changes to the
universal joint shaft.
WARNING
Danger of crushing from unintentional
Rolling of the tractor and the coupled implement!
Lowering of the lifted implement!
Secure the tractor and implement from unintentional starting and
unintentional rolling and secure the implement from unintentional
lowering before entering the danger zone between the tractor and
lifted implement in order to adjust the universal joint shaft.
1. Couple the soil tillage implement to the tractor.
2. Secure the tractor and implement against unintentional start-up
and rolling.
3. Clean and grease the following:
The tractor PTO shaft.
The gearbox input shaft of the implement.
4. Fix the two universal joint shaft halves to the tractor PTO shaft
and the gearbox input shaft.
Do not interconnect the universal joint shaft halves.
Observe the operating manual from the universal joint shaft
manufacturer.
5. Raise and lower the implement.
To do so, actuate the control valves at the rear of the tractor.
6. Before entering the danger area between the tractor and
implement, secure the raised implement against unintentional
lowering, by supporting it or hooking it to a crane.
7. Determine the shortest and longest operating position for the
universal joint shaft by holding the universal joint shaft halves
next to each other.
8. If necessary, have the universal joint shaft shortened in a
specialist workshop. Observe the operating manual from the
universal joint shaft manufacturer.
The safety devices and guards of the extended universal joint shaft
must overlap by at least 50 mm.
WARNING
Never actuate the operating controls for the tractor's three-point
hydraulic system while you are in the danger area between the
tractor and implement.