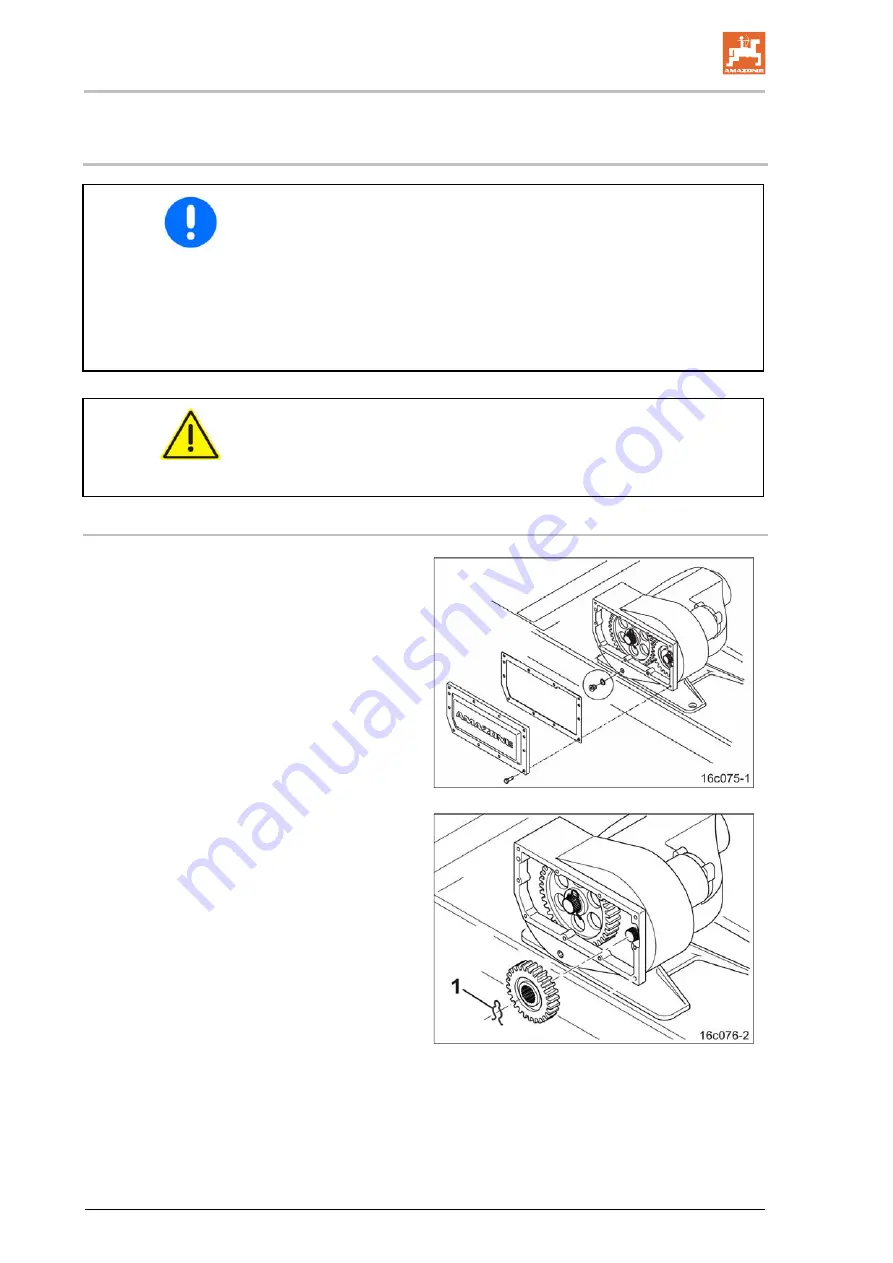
Cleaning, maintenance and repair
150
KG / KX / KE BAH0063-6 04.16
12.3.2
Repositioning/replacing the gear wheels
on the WHG/KX / WHG/KG Special / Super (specialised workshop)
When the gearbox cover is opened, transmission fluid runs out.
To prevent contamination from escaping fluid,
raise the mounted implement using the tractor's three-point
hydraulics until the implement is inclined about 30° forwards
park the implement on solid ground and reduce the oil level by
draining off the transmission fluid.
Only reuse the collected transmission fluid if it has not been
contaminated by dirt particles.
DANGER
Secure the raised soil tillage implement which is attached to the
tractor against unintentional lowering by using suitable support
elements or a crane.
12.3.2.1 Repositioning/replacing the gear wheels on the WHG/KX
1. Couple the soil tillage implement to the
tractor.
2. Uncouple the seed drill.
3. Tilt the implement about 30° forwards using
the tractor's three-point hydraulic system.
4. Switch off the tractor PTO shaft, apply the
tractor parking brake, switch the tractor
engine off and remove the ignition key.
5. Secure the raised implement using suitable
support elements or a crane.
6. Open the gearbox cover.
Fig. 157
7. Remove the retaining springs (Fig. 157/1).
8. Remove the gear wheels and, using the
speed table,
swap them around or
replace with a different set of gear
wheels.
9. Fit the retaining springs.
10. Close the gearbox cover and cover gasket.
11. Lower the implement.
12. Check the gearbox for leak points.
13. Check the oil level.
Fig. 158