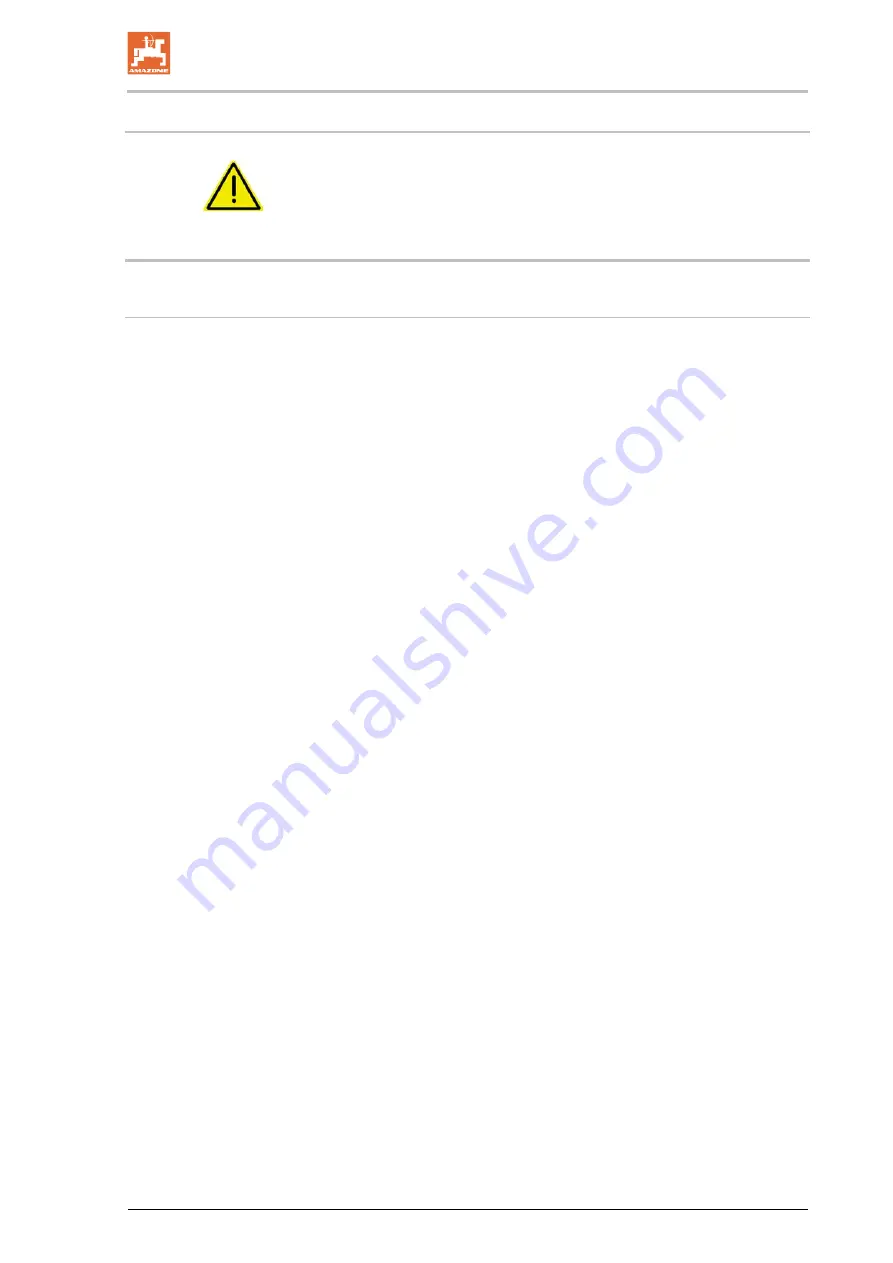
General safety advice
Citan BAG0014.4 09.14
25
2.16
Safety advice for the operator
Warning!
Always check traffic and operational safety before putting the
machine to operation!
2.16.1
General safety and accident prevention advice
Coupling and uncoupling the machine
•
Only connect and transport the machine with tractors suitable for
the task.
•
When coupling machines to the tractor's three-point linkage, the
linkages of the tractor and the machine must always be the
same.
•
Connect the machine to the prescribed equipment in accordance
with the specifications.
•
When coupling machines to the front or the rear of the tractor,
the following may not be exceeded:
ο
The approved total tractor weight
ο
The approved tractor axle loads
ο
The approved load capacities of the tractor tyres
•
Secure the tractor and the machine against rolling unintentionally
before coupling or uncoupling the machine.
•
Do not stand between the machine and tractor to be coupled
while the tractor is approaching the machine.
Any helpers may only act as guides standing next to the vehi-
cles, and may only move between the vehicles when both are at
a standstill.
•
Before connecting the machine to or disconnecting the machine
from the tractor's three-point linkage, secure the operating lever of
the tractor hydraulic system so that unintentional raising or lowering
is prevented.
•
When coupling and uncoupling machines, move the support
equipment (if available) to the appropriate position (stability).
•
When actuating the support equipment, there is a risk of injury
from crushing and cutting points.
•
Be particularly careful when coupling the machine to the tractor
or uncoupling it from the tractor. There are crushing and cutting
points in the area of the coupling point between the tractor and
the machine.
•
It is forbidden to stand between the tractor and the machine
when actuating the three-point linkage.
•
Coupled supply lines
ο
must give slightly to all movements while cornering without
tensioning, kinking or rubbing.
ο
must not chafe against other parts.
•
The release ropes for quick couplings must hang loosely and
must not release themselves when lowered.
•
Also ensure that uncoupled machines are stable.