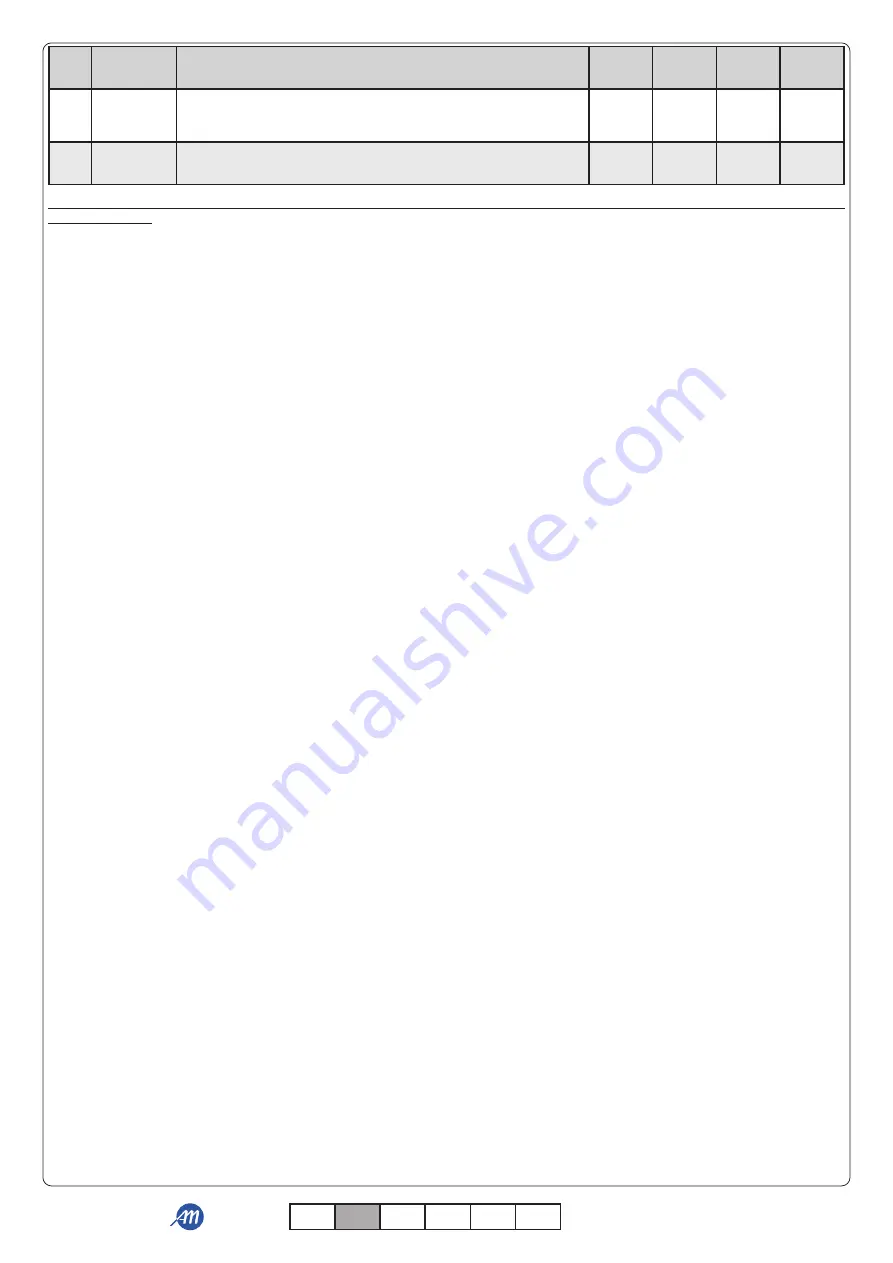
14/20
6-1622400 rev. 8 19/01/2022
ENG
ITA
ENG
FRA
ESP
NLD
TUR
PARAMETERS
DESCRIPTION
DEFAULT
CUSTOM
MIN
MAX
UNIT
9
LSI
Amplitude of slowdown.
P = personalized during learning.
0…100% = percentage of stroke.
20
0
100
%
10
asL
Anti slipping / Extra time.
15
0
300
s
NOTE - the parameters highlighted in grey depend on the selected motor. In the table are reported the data of the CUSTOM motor. For more information,
refer to chapter 11.
1. AUTO RECLOSING TIME
TCL
Active when the automation is in the completely open position, the automation automatically closes after
tCL
. seconds. In this phase the display shows
-TC
with the blinking dash, that during the last 10 seconds will be replaced by the count down. An opening command or the photocells intervention
restarts the counting.
2. AUTO RECLOSING TIME AFTER TRANSIT
ttr
If in the opening phase or in the completely open position the beam of the photocells is obscured and freed, the automation automatically closes
after
ttr
seconds when the completely open position is reached. In this phase the display shows
-tC
with the blinking dash, that during the last 10
seconds will be replaced by the count down.
3. OBSTACLE SENSITIVITY WITH RUNNING SPEED
SEn
Adjust the obstacle sensitivity to ensure a correct functioning of the automation, it must stop if there is an obstacle but also it must ensure the complete
movement in the worst conditions (exp. winter, hardening of motors, etc). After the adjustment of this parameter it is recommended to perform a
complete movimentation (opening and closing) before trying the obstacle detection.
Lower values correspond to a greater thrust on the obstacle.
The intervention for obstacle stops the automation and makes a short inversion of the movement.
4. OBSTACLE SENSITIVITY DURING SLOWDOWNS
SEL
Adjust the obstacle sensitivity during the slowdown to ensure a correct functioning of the automation, it must stop if there is an obstacle but also it must
ensure the complete movement in the worst conditions (exp. winter, hardening of motors, etc). After the adjustment of this parameter it is recommended
to perform a complete movimentation (opening and closing) before trying the obstacle detection.
Lower values correspond to a greater thrust on the obstacle.
The intervention for obstacle stops the automation and makes a short inversion of the movement.
5. RUNNING SPEED
SPn
Adjust the running speed to ensure a correct functioning of the automation. It is possible to adjust the percentage of speed between 50% and 100%.
WARNING - after the amendment of this parameter, it is necessary to carry out a new setting of the strokes.
6. SLOWDOWNS SPEED
SPL
Adjust the slowdowns speed to ensure a correct functioning of the automation. It is possible to adjust the percentage of speed between 10% and
100% of the running speed
SPn
.
WARNING - after the amendment of this parameter, it is necessary to carry out a new setting of the strokes.
7. STEP BY STEP CONFIGURATION (SS)
SBS
It is possible to set 5 different working modes for the SS command:
•
SBS
=
0
normal (AP-ST-CH-ST-AP-ST-CH-…).
Typical functioning of Step by Step. During the movement a SS command stops the automation.
•
SBS
=
1
alternated STOP (AP-ST-CH-AP-ST-CH-…).
Alternated functioning with STOP during the opening. During the opening phase a SS command stops the automation.
•
SBS
=
2
alternated (AP-CH-AP-CH-…).
The user cannot stop the automation during the movement with a SS command.
A SS command during the movement inverts the movement.
•
SBS
=
3
condominium – timer.
A SS command only opens the automation. When the automation is completely open, if the command persists the control unit will wait until the
opening of the contact before beginning the contdown of the automatic reclosing (if enabled), another SS command in this phase will restart the
contdown of the automatic reclosing.
•
SBS
=
4
condominium with immediate auto reclosing.
Like condominium – timer (previous point) but during the countdown a SS command will close the automation.
8. AFTER BLACK-OUT
blt
When the control unit switches on after a black-out, the behaviour of the control unit depends on the parameter
blt
:
•
blt
=
0
no action – when the control unit turns on the automation doesn’t move until the first command. The first movement is an opening.
•
blt
=
1
closing – at the turning on of the control unit it will perform a closing.
9. AMPLITUDE OF SLOWDOWN
LSI
With this parameter it is possible to adjust the amplitude of the slowdown and eventually disable it (
LSI
=
0
). If you need more precise or different
slowdown between opening and closing it is possible to set the parameter
LSI
on
P
(personalized) and perform an advanced learning of strokes
providing also the beginning of slowdowns during the learning.
10. ANTI SLIPPING / EXTRA TIME
ASL
This parameter is used if the motor slips, the control unit adds
asL
seconds to the movement, to ensure a complete movement of the automation also
in the worst conditions.
Summary of Contents for BIOS1 24V
Page 1: ...BIOS1 24V MADE IN ITALY CENTRALINA PER CANCELLI SCORREVOLI 24V...
Page 21: ...BIOS1 24V CONTROL UNIT FOR SLIDING GATES AT 24V MADE IN ITALY...
Page 41: ...BIOS1 24V CENTRAL DE COMMANDE POUR PORTAIL COULISSANT 24V MADE IN ITALY...
Page 61: ...BIOS1 24V CUADRO DE MANDO PARA CANCELAS CORREDERAS 24V MADE IN ITALY...
Page 81: ...BIOS1 24V BESTURINGSEENHEID VOOR SCHUIFPOORTEN 24V MADE IN ITALY...
Page 101: ...BIOS1 24V 24V KAYAR KAPILAR N KUMANDA MERKEZ TALYAN MALI...