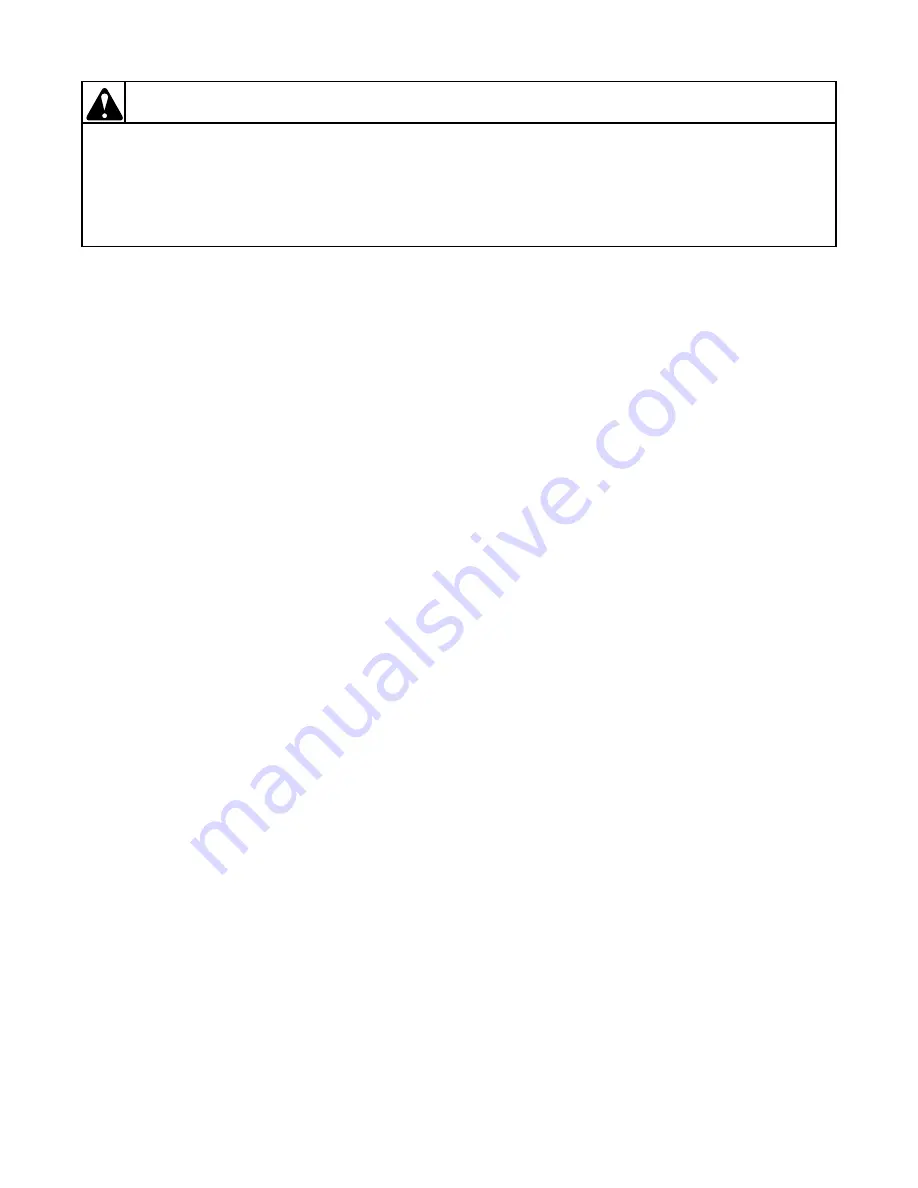
70
39201
Section 5 Service Procedures
To reduce the risk of electric shock, fire, explosion, serious injury or death:
• Disconnect electric power to the washer before servicing.
• Never start the washer with any guards/panels removed.
• Whenever ground wires are removed during servicing, these ground wires must be
reconnected to ensure that the washer is properly grounded.
W003
WARNING
© Copyright, Alliance Laundry Systems LLC – DO NOT COPY or TRANSMIT
NOTE: It may be necessary to use a gear puller to
remove hub.
n. Remove old water seal from outer tub.
IMPORTANT: Use care when removing old seal so
as not to damage tub flange or porcelain.
NOTE: When reinstalling or replacing outer tub,
always install a new No. 646P3 Hub and Seal Kit.
Refer to Paragraph 37.
o. Using No. 289P4 Spring Hook Tool, unhook
six module springs from lower edge of outer
tub. Refer to Figure 54.
IMPORTANT: When installing module springs,
make sure spring hook is fully seated in hole in tub
skirt. Mark the word “FRONT” on front side of
outer tub so complete tub module can be reinstalled
in same position.
p. Loosen hose clamp and remove hose from
bottom of outer tub.
IMPORTANT: Some water will always remain in
outer tub. Therefore, before removing hose from
pump, pinch off or drain hose to prevent water
spillage.
q. Loosen hose clamp and remove pressure hose
from pressure bulb. Refer to Figure 44.
r. Remove wire tie holding motor wire harness to
support leg.
s. Grasp outer tub and lift complete tub module
assembly straight up and out of washer cabinet.
t. Turn outer tub upside-down and set on
protective padding.
u. Remove screw, washer and helix holding drive
pulley to input shaft of transmission assembly.
Refer to Figure 55.
v. Lift drive pulley up and out from between
support legs.
NOTE: When reinstalling pulley, place a small
amount of No. 03200P Lubricant to top side of drive
pulley that will be contacting the large flat washer.
Lubricate helix ramps with a small amount of
No. 03200P Lubricant. Refer to Figure 56.
IMPORTANT:
DO NOT OVER LUBRICATE!
Excess lubricant can be thrown into pivot dome
area during normal washer operation. Any
lubricant on pivot dome, base or friction ring will
affect washer operation. This condition will persist
until lubricant is removed.
w. Remove two screws holding counterweight to
support leg.
x. Remove screws and lockwashers holding each
support leg to outer tub. Refer to Figure 56.
Then lift weldment assembly off transmission
tube.
NOTE: It may be necessary to tap lightly on
weldment assembly to loosen it from transmission
tube.
y. Lift transmission assembly out of upper
bearing.