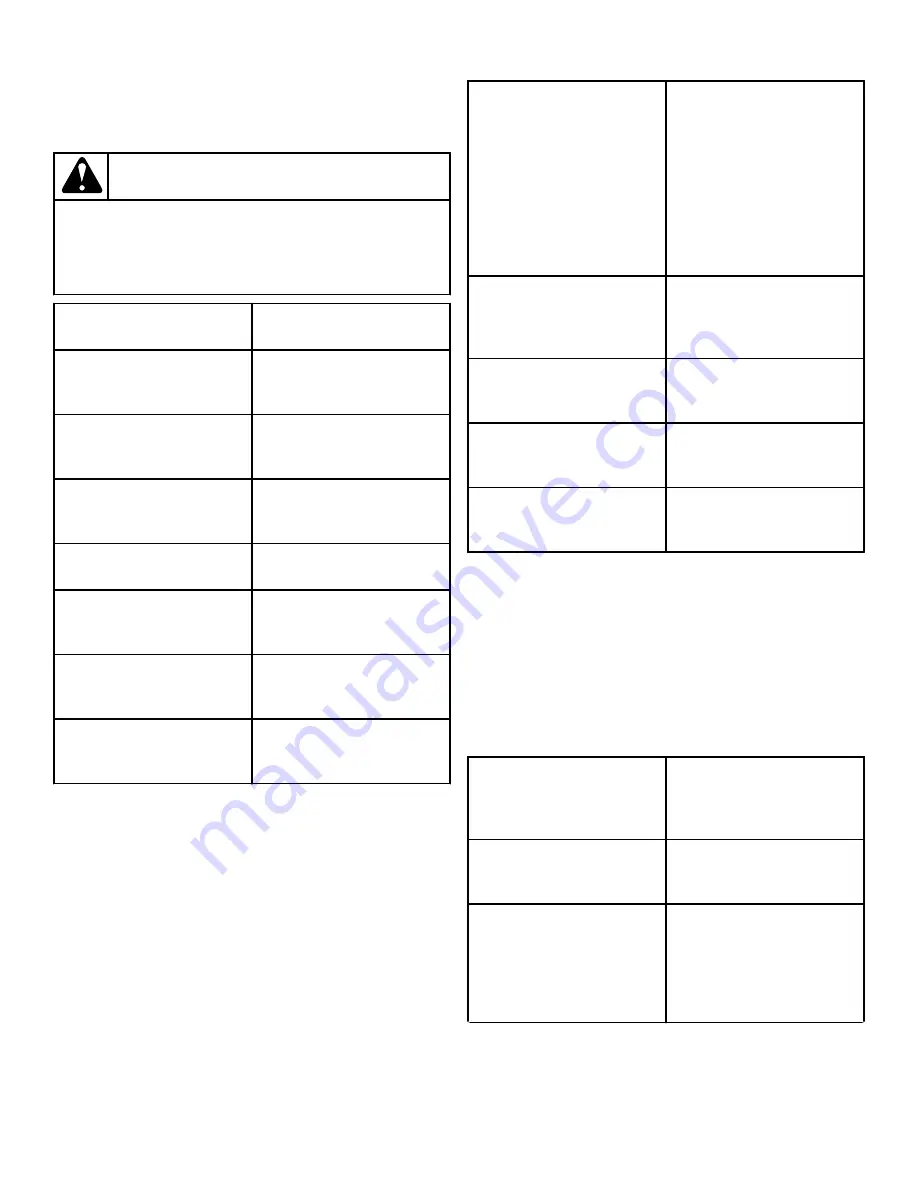
(Refer to Monitoring Temperature Values).
A skilled and experienced technician must examine the heating
and air outlet system before the machine is put in operation again.
WARNING
IF FAILURE 37 OCCURS WE CAN EXPECT THERE IS
RISK OF BURN AND NECESSARY ACTIONS MUST
BE TAKEN TO REDUCE TEMPERATURE.
C143
1. Check the air outlet system. If the airflow is not sufficient,
adjust the air outlet system.
2. Check the temperature sen-
sor.
If the temperature sensor is not
measuring correctly, replace
the temperature sensor.
3. Check the heating system.
If the heating system is bro-
ken, repair or replace the heat-
ing system.
4. Check the heating contactor
(valve).
If the heating contactor (valve)
is not functional, repair or re-
place the component.
5. Check the wiring.
If the wiring is damaged, re-
pair the wiring.
6. Check the Safety Thermo-
stats ST1 & ST2.
The Safety Thermostats should
go open before failure 37 is
generated.
7. Check the output relay that
controls the heating system.
If the output relay is not func-
tional, replace the control
board.
8. Check the input Signal by
monitoring the state at the
Service menu.
If the input is not functional,
replace the control board.
Failure 39: Error Fan
Machine With Heat Pump (HP)
Error 39 is displayed as soon as an electronic protection of the
fan motor is activated.
A qualified technician must examine the water heating system
and air exhaust system before the machine is put in operation
again.
DIAGNOSE:
1. Check if the contact of the
electronic protection of the
fan motor is connected when
the fan is operating (CMF –
On).
NOTE: If supply voltage
is not fed into the fan,
the protection contact is
in the open state.
If the contact is disconnected,
the fan motor is overheated
or the fan is damaged: wait
until the fan cools down - ap-
prox. 15 minutes. In case the
fault is a temperature prob-
lem and the fan is not dam-
aged, the error will not reac-
tivate when the machine is
restarted.
2. Check if the airflow is ob-
structed. Also check if the ro-
tation of the drum and fan are
obstructed/limited.
Check if the lint filter is clog-
ged, if so, clean it. Check the
heat exchangers, if clogged
with dust, clean them.
3. In case the electronic pro-
tection of the motor does not
connect within 15 minutes.
It is likely the fan is damaged,
replace the fan.
4. Check if the power supply
and control circuits of the fan
are interrupted.
If the circuits are interrupted,
repair them.
5. Check the input signal based
on the state as indicated in the
Service menu.
If the input is not functional,
replace the programmer board.
Failure 40: Phase Error
Machine With Heat Pump (HP)
Error 40 may occur when the sequence of phases is incorrectly
connected in the power supply system.
If error 40 occurs during the operation, it is either due to a failure
of one phase of the power supply system or due to a significant
difference of voltage in the individual phases.
DIAGNOSE:
1. The fault occurred after the
machine was installed.
Change the sequence of phases
respective to the power supply
system on the machine supply
cable.
2. The fault occurred during
machine operation.
Check if unwanted failures in
the machine power supply sys-
tem occurred.
3. The fault occurred during
machine operation - check (ac-
cording to the wiring diagram)
if interruptions in the power
supply circuits of the individu-
al machine circuits occurred.
Check the state of the pilot re-
lay which monitors the phases.
If the wiring is not continuous,
repair the wiring.
Table continues...
Troubleshooting
©
Copyright, Alliance Laundry Systems LLC -
DO NOT COPY or TRANSMIT
51
Part No. D1621ENR3
Summary of Contents for SGHP190E
Page 2: ......