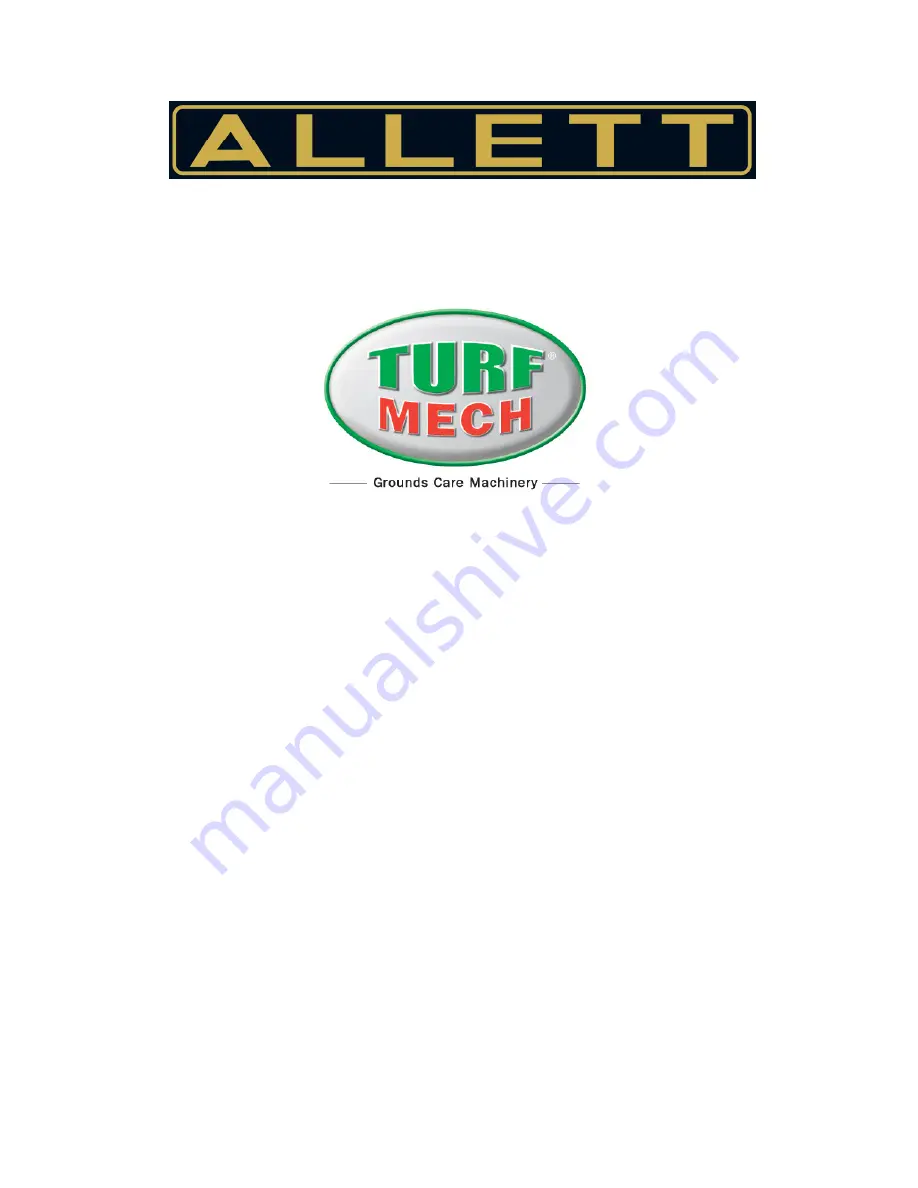
BY
BUFFALO 20”, 24” & 27”
OPERATORS & PARTS MANUAL
English version
Turfmech Machinery Limited
Hangar 5, New Road, Hixon, Stafford, ST18 0PJ, United Kingdom
Tel: +44 (0) 1889 271503
Fax: +44 (0) 1889 271321
www.turfmech.co.uk
For Allett spare parts
Tel: +44 (0) 1889 272092 or 272093
Fax: +44 (0) 1889 272084
www.allett.co.uk
Summary of Contents for BUFFALO 24"
Page 2: ......
Page 4: ......
Page 38: ...32 ...
Page 39: ...33 BUFFALO 20 24 27 PARTS SECTION ...
Page 40: ...34 ...
Page 42: ...36 Chassis ...
Page 44: ...38 Cutting Cylinder Bottom Blade and Front Roller ...
Page 46: ...40 Cutting Cylinder Bottom Blade and Front Roller ...
Page 48: ...42 Engine and Drive Shaft ...
Page 50: ...44 Drive Train Components ...
Page 52: ...46 Drive Train Components ...
Page 54: ...48 Drive Train Components ...
Page 56: ...50 Parking Brake ...
Page 58: ...52 Handlebars and Control Cables ...
Page 60: ...54 Handlebars and Control Cables ...
Page 62: ...56 Rear Drive Roller ...
Page 64: ...58 Rear Drive Roller ...
Page 66: ...60 Grassbox ...
Page 68: ...62 Notes ...