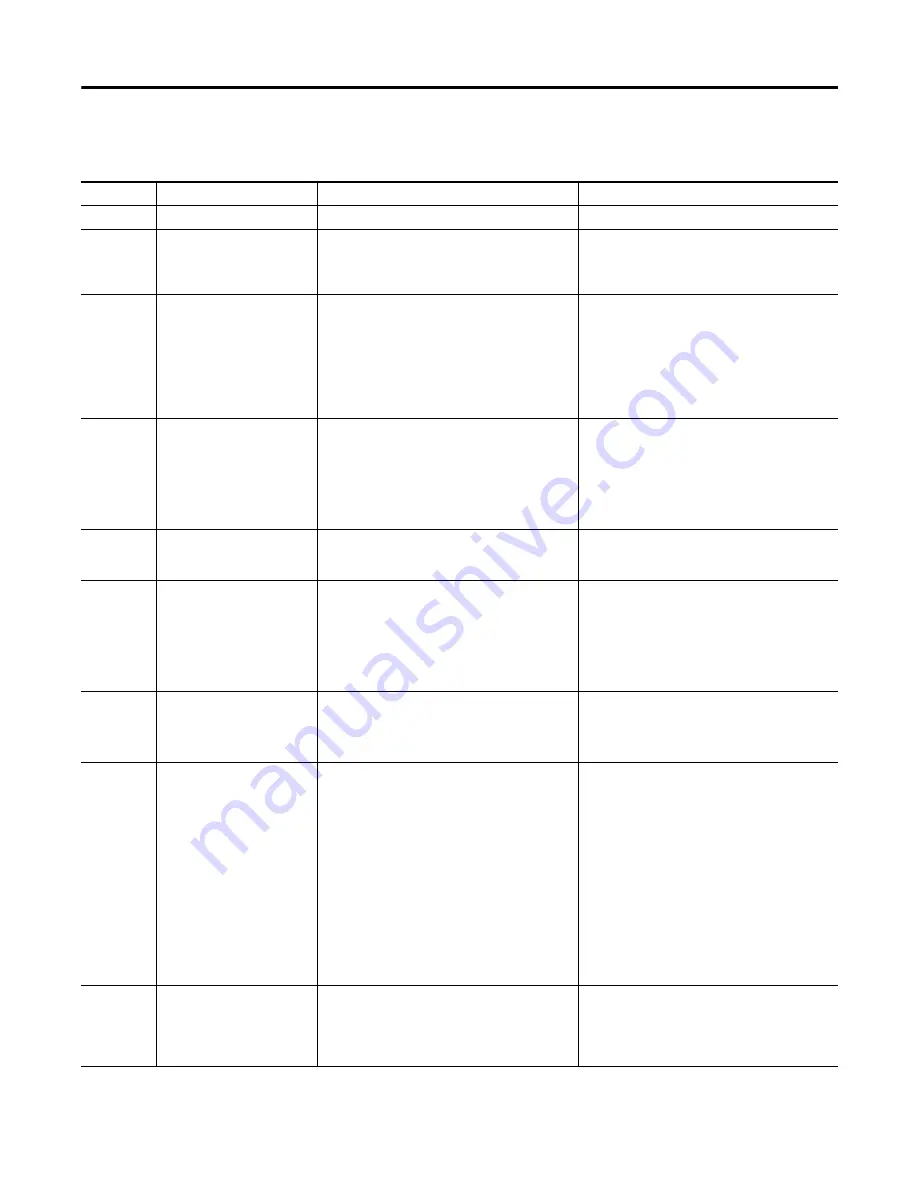
Rockwell Automation Publication 2080-UM002K-EN-E - March 2019
107
Motion Control
Chapter
7
Motion Function Block and Axis status Error ID
Error ID
Error ID MACRO
Error description for Function Block
Error description for Axis Status
(1)
00
MC_FB_ERR_NO
Function block execution is successful.
The axis is in operational state.
01
MC_FB_ERR_WRONG_STATE The function block cannot execute because the
axis is not in the correct state. Check the axis
state.
The axis is not operational due to incorrect axis
state detected during a function block execution.
Reset the state of the axis using the MC_Reset
function block.
02
MC_FB_ERR_RANGE
The function block cannot execute because there is
invalid axis dynamic parameter(s) (velocity,
acceleration, deceleration, or jerk) set in the
function block.
Correct the setting for the dynamic parameters in
the function block against Axis Dynamics
configuration page.
The axis is not operational due to invalid axis
dynamic parameter(s) (velocity, acceleration,
deceleration, or jerk) set in a function block.
Reset the state of the axis using the MC_Reset
function block.
Correct the setting for the dynamic parameters in
the function block against Axis Dynamics
configuration page.
03
MC_FB_ERR_PARAM
The function block cannot execute because there is
invalid parameter other than velocity, acceleration,
deceleration, or jerk, set in the function block.
Correct the setting for the parameters (for
example, mode or position) for the function block.
The axis is not operational due to invalid
parameter(s) other than velocity, acceleration,
deceleration, or jerk, set in a function block.
Reset the state of the axis using the MC_Reset
function block.
Correct the setting for the parameters (for
example, mode or position) for the function block.
04
MC_FB_ERR_AXISNUM
The function block cannot execute because the
axis does not exist, the axis configuration data is
corrupted, or the axis is not correctly configured.
Motion internal Fault, Error ID = 0x04.
Call Tech support.
05
MC_FB_ERR_MECHAN The function block cannot execute because the
axis is faulty due to drive or mechanical issues.
Check the connection between the drive and the
controller (Drive Ready and In-Position signals),
and ensure the drive is operating normally.
The axis is not operational due to drive or
mechanical issues.
Check the connection between the drive and the
controller (Drive Ready and In-Position signals),
and ensure the drive is operating normally.
Reset the state of the axis using the MC_Reset
function block.
06
MC_FB_ERR_NOPOWER The function block cannot execute because the
axis is not powered on.
Power on the axis using MC_Power function block.
The axis is not powered on.
Power on the axis using MC_Power function block.
Reset the state of the axis using the MC_Reset
function block.
07
MC_FB_ERR_RESOURCE
The function block cannot execute because the
resource required by the function block is
controlled by some other function block or not
available.
Ensure the resource required by the function block
available for use.
Some examples:
•
MC_power function block attempts to control
the same axis.
•
MC_Stop function block is executed against the
same axis at the same time.
•
Two or more MC_TouchProbe function blocks
are executed against the same axis at the same
time.
The axis is not operational due to the resource
required by a function block is under the control of
other function block, or not available.
Ensure the resource required by the function block
available for use.
Reset the state of the axis using the MC_Reset
function block.
08
MC_FB_ERR_PROFILE
The function block cannot execute because the
motion profile defined in the function block cannot
be achieved.
Correct the profile in the function block.
The axis is not operational due to motion profile
defined in a function block cannot be achieved.
Reset the state of the axis using the MC_Reset
function block. Correct the profile in the function
block.
Summary of Contents for Micro830
Page 6: ...vi Rockwell Automation Publication 2080 UM002K EN E March 2019 Preface Notes ...
Page 273: ...Rockwell Automation Publication 2080 UM002K EN E March 2019 259 Quickstarts Appendix C ...
Page 300: ...286 Rockwell Automation Publication 2080 UM002K EN E March 2019 Appendix C Quickstarts Notes ...
Page 352: ...Rockwell Automation Publication 2080 UM002K EN E March 2019 338 Index Notes ...
Page 353: ...Rockwell Automation Publication 2080 UM002K EN E March 2019 339 ...