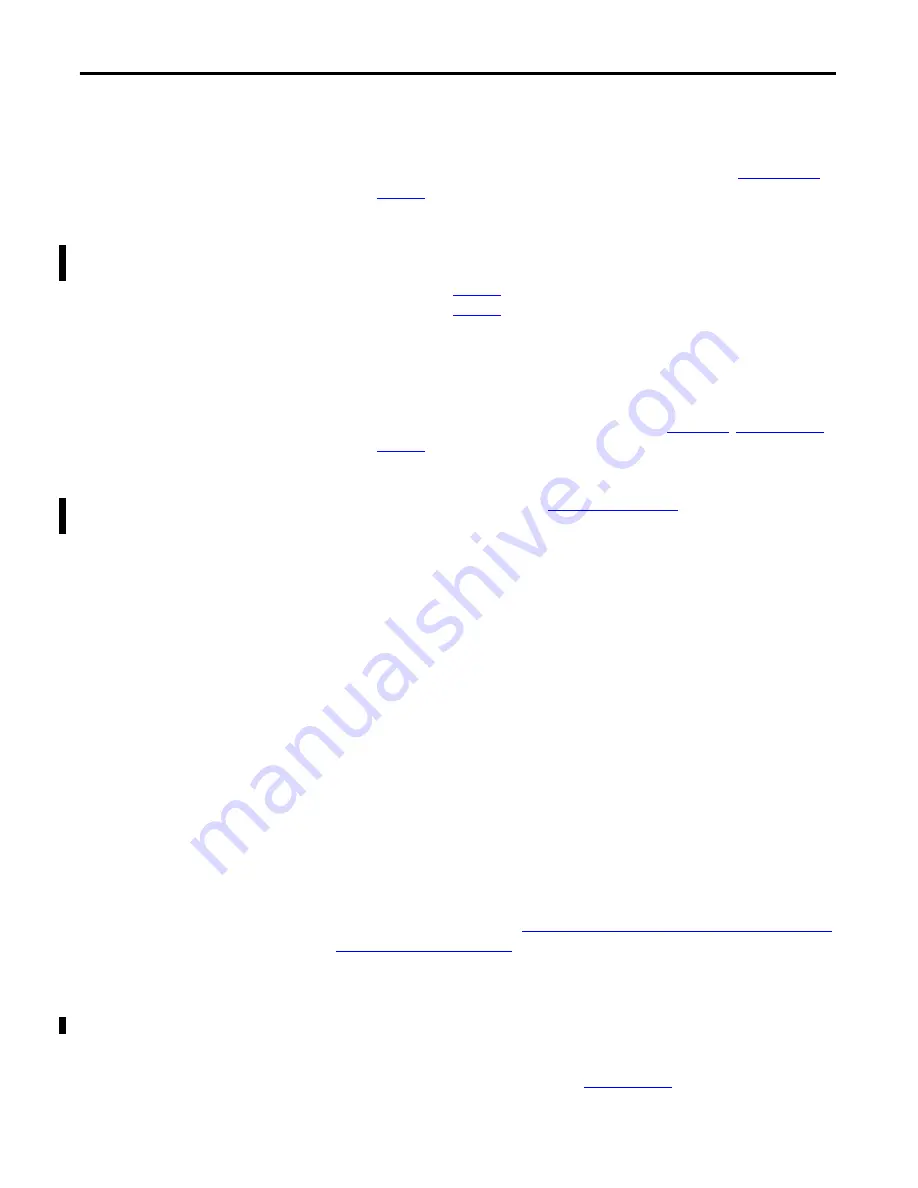
44
Rockwell Automation Publication 1756-RM001I-EN-P - May 2012
Chapter 5
ControlLogix I/O Modules
• Use of external relays to disconnect module power if output
de-energized state is critical
. To verify that outputs will de-energize, users
must wire an external relay or other measure, that can remove power from
the output module if a short or other fault is detected. See
for an example method of wiring an external relay.
• Test outputs at specific times to make sure they are operating properly
.
The method and frequency of testing is determined by the requirements of
the safety application. For more information on testing diagnostic module
outputs, see
. For more information on testing standard module
outputs, see
• For typical emergency shutdown (ESD) application outputs must be
configured to de-energize
: When configuring any ControlLogix output
module, each output must be configured to de-energize in the event of a
fault and in the event of the controller going into Program mode. For
exceptions to the typical ESD applications, see
•
When wiring two digital output modules in series so that one may break
source voltage (as shown in
), one controller must
own both modules.
Wiring ControlLogix Digital Output Modules
Diagnostic digital output modules and standard output modules have different
wiring considerations. Reference the module-type considerations that apply to
your system configuration.
Wiring Diagnostic Digital Output Modules
Diagnostic output modules have circuitry that is not included in standard output
modules. Because of this feature, you are not required to use an input module to
monitor output status, as is required with standard output modules.
Diagnostic output modules can be used as-is in a SIL 2 application. No special
wiring considerations need be employed other than the wiring of the external
relay to remove line power from the module in the event of a fault to make sure
outputs will de-energize if shorted.
In addition to referencing the
Requirements When Using ControlLogix Digital
, perform a Pulse Test on each output periodically to
make sure that the output is capable of changing state. Automatic diagnostic
testing of output modules should be made at intervals that are an order of
magnitude less than the demand rate. For example, pulse testing should be
scheduled at least twice a year for a low demand system.
For more information on performing the pulse test, see the ControlLogix Digital
I/O Modules User Manual, publication
Summary of Contents for 1756-L6 Series
Page 24: ...24 Rockwell Automation Publication 1756 RM001I EN P May 2012 Chapter 1 SIL Policy Notes ...
Page 76: ...76 Rockwell Automation Publication 1756 RM001I EN P May 2012 Chapter 6 FLEX I O Modules Notes ...
Page 126: ...126 Rockwell Automation Publication 1756 RM001I EN P May 2012 Appendix D Checklists Notes ...
Page 133: ...Allen Bradley Motors ...