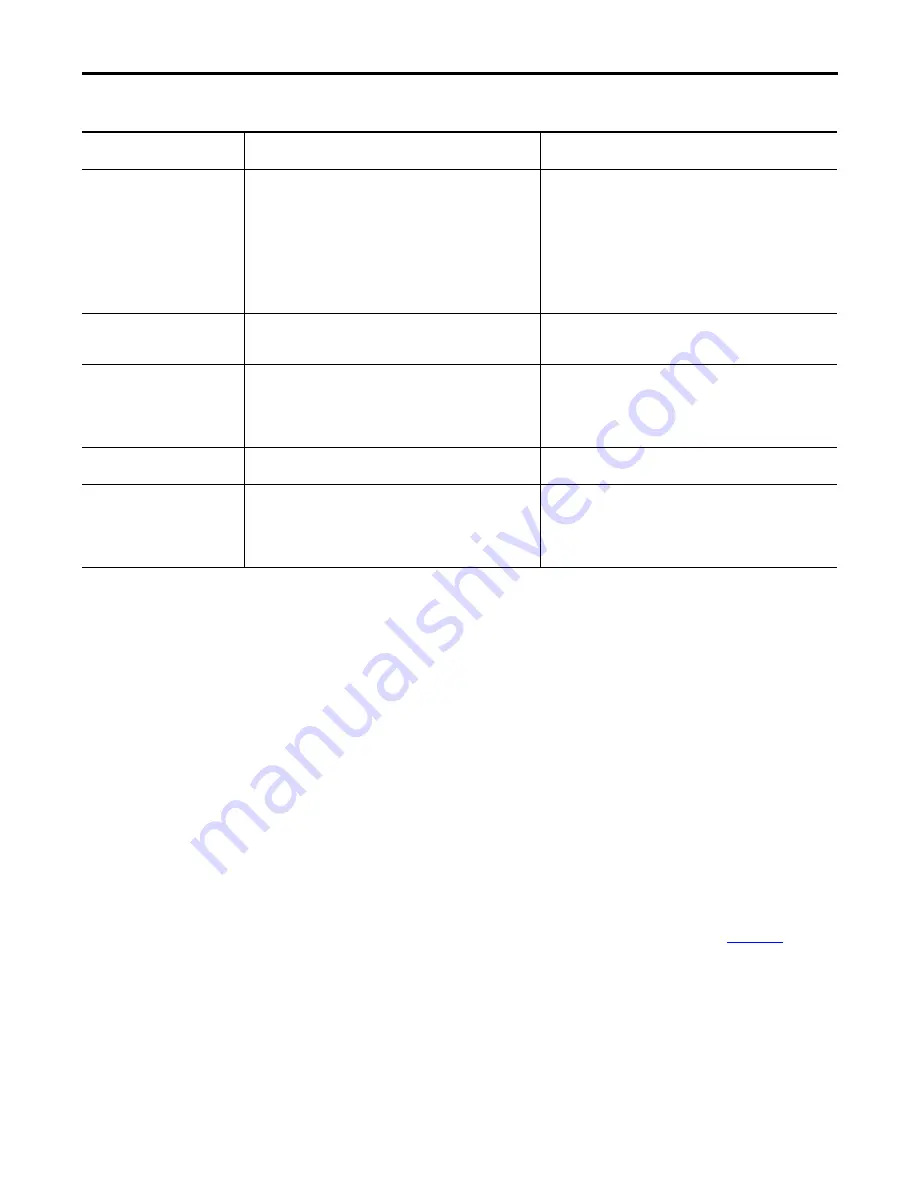
Rockwell Automation Publication 1756-UM540E-EN-P - December 2017
175
Troubleshoot Your Module
Chapter 9
1756-IF8I Module - Incorrect Input Voltage/Current Readings
To determine the cause of the incorrect reading, first determine the nature of the
incorrect reading. For example, the module can perform as follows:
•
The module always reads maximum.
•
The module always reads minimum/zero/negative.
•
The module reads voltage/current erratically (data jumping around).
•
The module reads with an offset over the entire range.
First, complete the following tasks.
1.
Check the status indicators to verify that the module is powered and
communicating.
Red or flashing green status indicators indicate a problem. For more
information on the 1756-IF8I module status indicators,
2.
Make sure that wiring is intact and correct, and that the current or voltage
input is wired to the corresponding terminals and with proper polarity.
Incorrect reading soon after module
installation
One of the following:
•
Incorrect readings at initial module installation and configuration
are often the result of installation and configuration errors.
•
Incorrect readings at installation of an existing, previously-
working module are more likely the result of a hardware failure.
One of the following:
•
If error is occurring on a new module installation and
configuration, make sure that those tasks were completed
corrected and correct any errors you find.
•
If the error is occurring on an existing, previously-working
module, diagnose the hardware failure and correct it. If more than
one channel is experiencing the incorrect readings in this case,
disconnect all thermocouples except one. This can help determine
if it is external hardware or the module itself is the cause
Grounded RTD
Due to the module's excitation current traveling on an RTD lead that
is grounded there can be errant ground paths which would cause
inaccuracies to the RTD measurements.
Eliminate the ground or use a signal conditioner/isolator.
Lead Compensation
An RTD sensor requires at least three leads to compensate for lead
resistance error, caused by resistance mismatch. The amount of error
eliminated depends upon the difference between the resistance
values of the lead wires. The closer the resistance values are to each
other, the greater the amount of error that is eliminated
To verify that the lead resistance values match as closely as possible:
•
use heavy gauge wire (16–18 gauge)
•
keep lead distances less than 1000 feet
•
use quality cable that has a small tolerance impedance rating.
Sensor Offset
The software configured Sensor Offset value is summed with the
input data value.
Verify that the Sensor Offset feature is desired.
Programming and Configuration
One of the following:
•
Input value read from correct data tag.
•
Channel configured for correct range.
•
Signal and Engineering units are set correctly and equal.
If the incorrect input data value is in a secondary location, for
example, an HMI device, verify the base tag value in the controller.
Correct module configuration as needed.
Table 25 - Troubleshoot Incorrect RTD Readings (continued)
Possible Cause of Incorrect
Reading
Description
Recommended Action