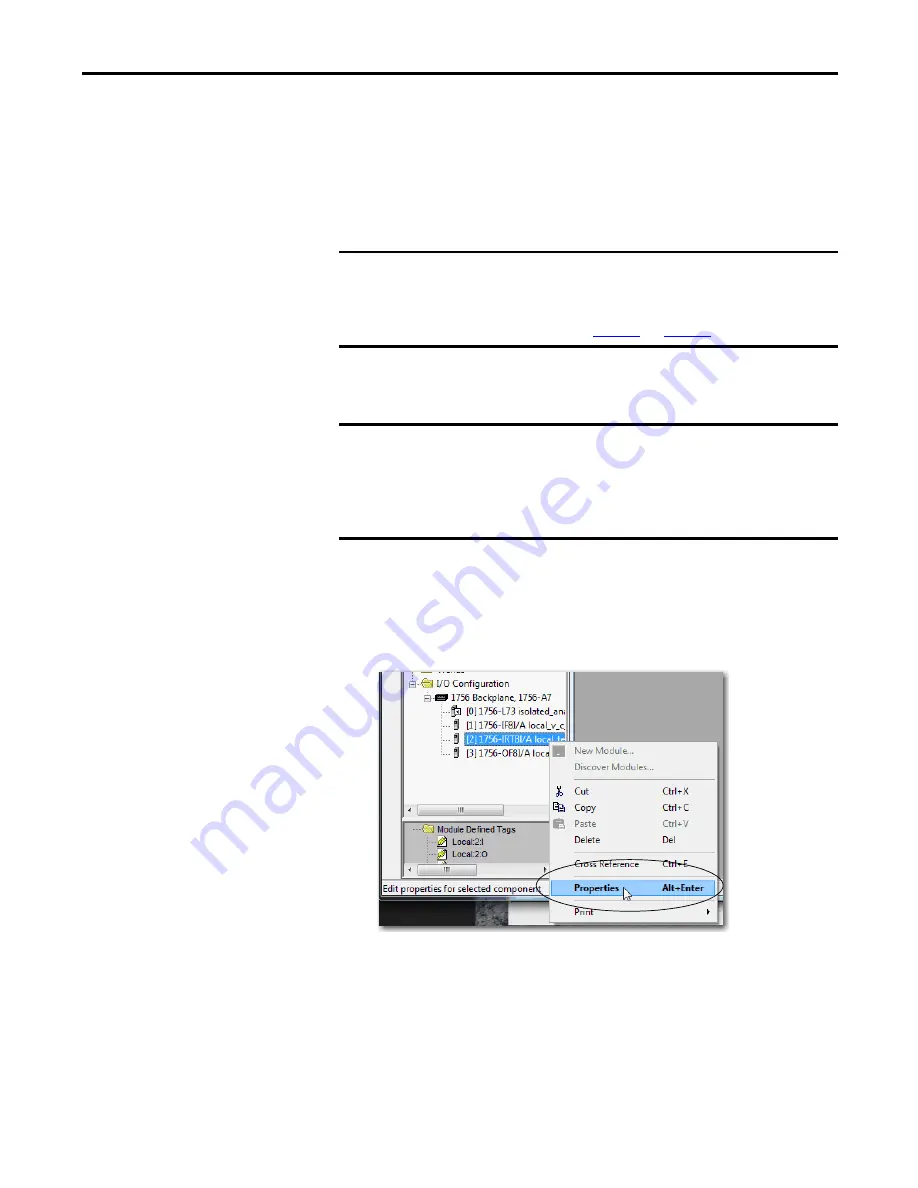
Rockwell Automation Publication 1756-UM540E-EN-P - December 2017
151
Calibrate the ControlLogix Analog I/O Modules
Chapter 8
Calibrate the Module for an RTD Input Type
The module uses two precision resistors to calibrate the channels in ohms. You
connect the following:
•
1
Ω
precision resistor for low reference calibration
•
487
Ω
precision resistor for high reference calibration
The module can operate in multiple input ranges when an RTD is connected.
However, the module calibrates only in the 0…500
Ω
range.
Follow these steps to calibrate your module.
1.
Go online with your project.
2.
Right-click the module you want to calibrate and choose Properties.
3.
On the Configuration tab, make sure that the Input Type for each channel
to be calibrated is set to the same RTD input type.
The sensor type selection does not impact calibration.
The1756-IRT8I module has eight channels, the 1756-IR12 module has
12, and 1756-IT16 module has 16.
IMPORTANT
After you connect either precision resistors to the 1756-IRT8I module, we
recommend that you wait for a minimum of two minutes before
proceeding to the next task to obtain the highest calibration accuracy.
For more information, see
page 153
and
page 153
.
IMPORTANT
When you are wiring precision resistors for calibration, follow the wiring
diagrams. Make sure terminals IN_x(-)/B and IN_x/RTD C are shorted
together at the RTB.
You can calibrate the 1756-IRT8I module for 3-wire or 4-wire mode.
Calibrate in the mode in which the module operates.