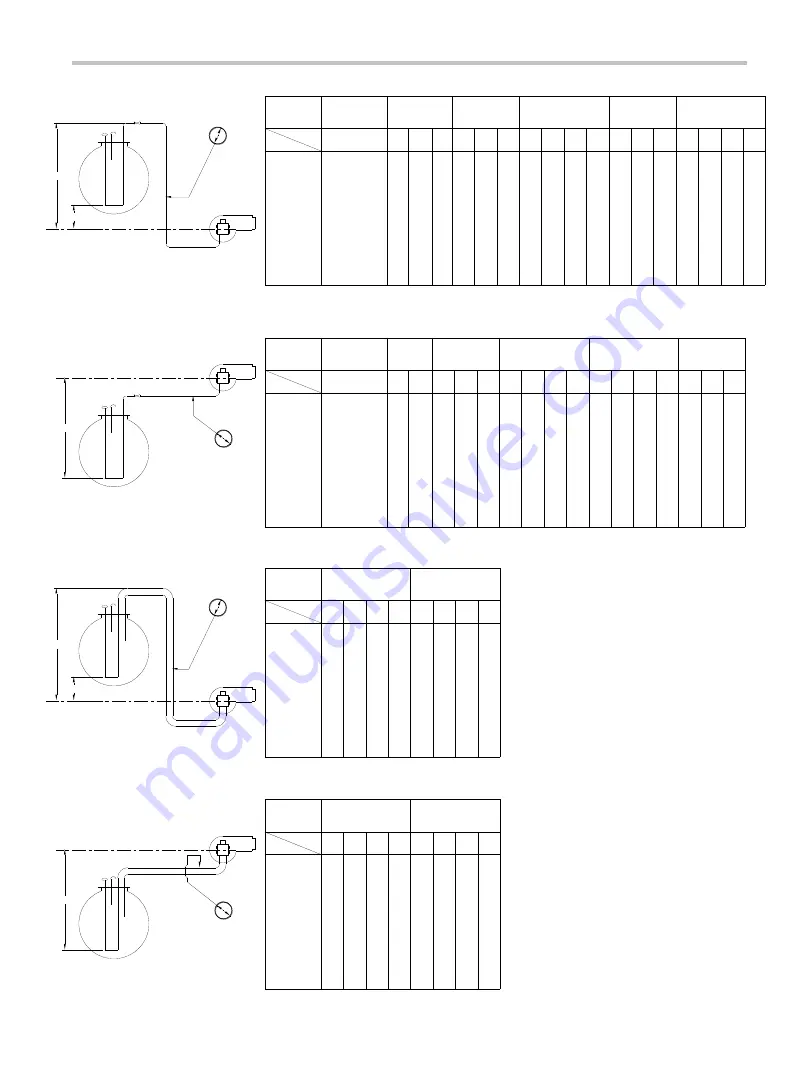
19
Nozzle
20
14
12
10
43
20
18
39
8
12
8
62
56
7
48
23
66
31
27
57
9
69
12
95
11
82
10
8
30
12
11
27
10
8
42
17
38
15
33
13
45
18
39
16
46
19
64
26
55
22
6
6
10
5
70
63
5
8
6
9
8
29
26
6
78
8
100
7
92
10
14
12
44
38
32
0,5
0
H (m)
1
3
2
d (mm)
10
75
36
14
100
52
21
73
30
100
16
50
4
9
d
H
E
E max. = 20m
(E-H) max. = 4,5 m
d
H max. = 4,5 m
H
AJ4/J4/E4
150
47
58
53
11
14
13
31
28
25
14
12
10
0
0,5
1
H (m)
d (mm)
69
91
80
17
23
20
43
37
49
2
4
3
16
81
91
100
100
100
100
d
(D-H) max. = 4,5 m
D max. = 20m
D
H
d
H
H max. = 4,5 m
14
72
81
89
100
100
100
30
10
12
14
48
25
12
13
28
53
92
70
81
59
49
37
43
31
23
17
20
15
32
15
100
61
24
28
11
13
9
7
8
10
45
92
79
66
46
53
38
20
54
16
60
31
16
35
18
14
12
4
-
H (m)
2
3
1
4
-
6
d (mm)
0
0,5
8
7
6
-
5
-
-
-
-
4
-
-
5
-
-
-
-
-
-
-
4
8
12
34
14
19
8
48
20
20
11
29
13
15
8
63
26
56
23
10
8
38
33
10
14
5
3
8
8
20
3
30
17
-
43
5
27
11
9
23
8
10
7
56
49
6
12
8
6
10
14
20
7
13
19
22
25
12
22
39
55
21
10
11
5
30
14
6
3
9
64
72
14
39
18
34
16
12
10
12
10
10
8
25
14
4
36
12
28
16
8
15
23
41
48
16
42
14
14
12
54
31
27
47
14
16
30
45
16
82
72
63
44
25
5
AJ6/J6/E6
250
11
13
9
8
7
6
93
82
70
25
47
54
28
40
21
59
53
48
30
34
17
16
27
14
10
12
14
16
AJ4/J4/E4
150
3
4
2
3
-
6
H (m)
10
1
0,5
0
9
10
11
d (mm)
-
3
7
5
24
43
14
7
-
-
25
13
0
-
2
13
7
-
-
14
25
10
12
14
12
AJ6/J6/E6
250
10
16
14
12
62
72
81
36
42
19
22
47
25
4
5
6
16
14
20
24
36
42
27
48
(US GPH)
One pipe siphon feed system
One pipe lift system
Nozzle
(US GPH)
Two pipe siphon feed system
Q* (I/h)
Pump
Two pipe lift system
Q* (I/h)
Pump