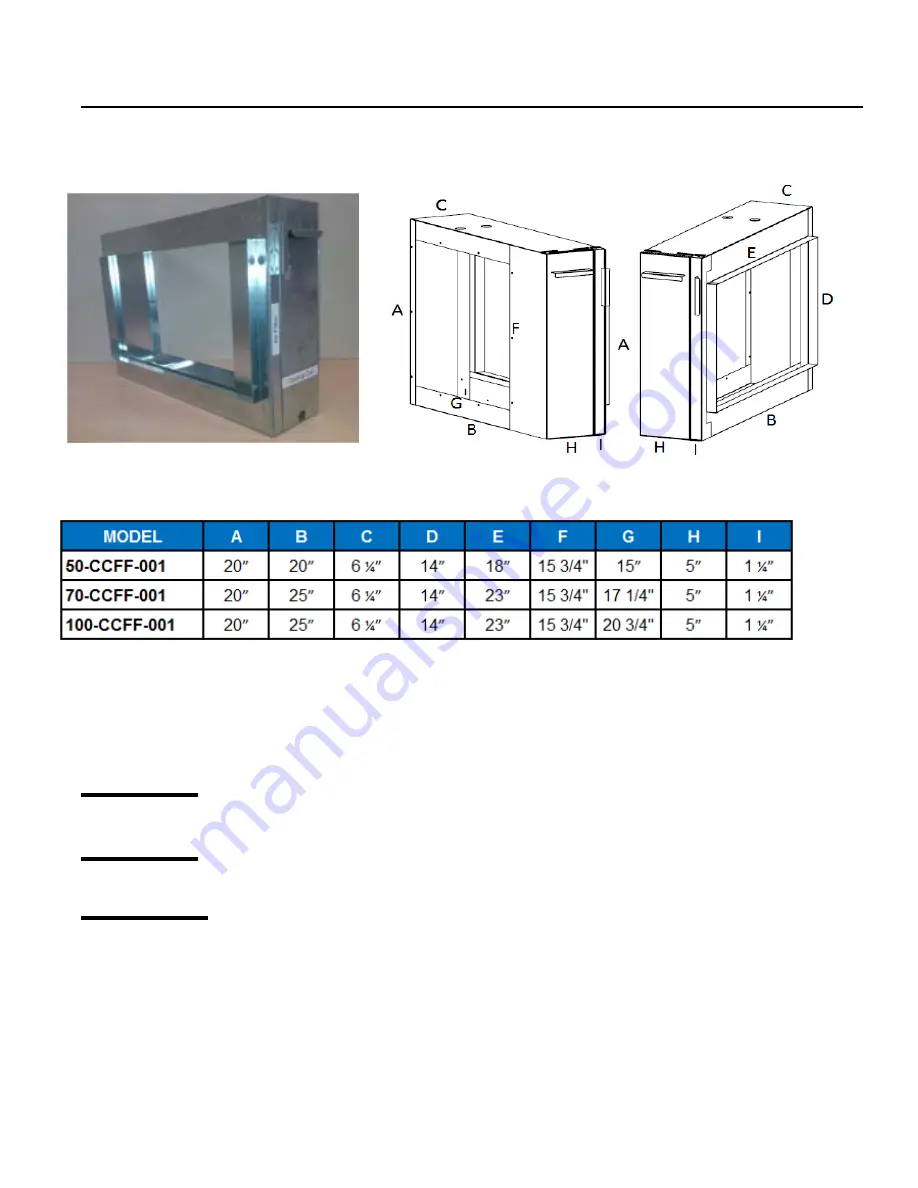
Page 58
50/70/100 CCFF-001 COOLING COIL FILTER FRAME CABINET
.
Cooling Coil Filter Frame:
Cooling coil filter frames accept a standard dimensional 1” filter. The
coil section has dimples pressed into the top and bottom of the cabinet to ensure proper coil
slope.
50-CCFF-001
cooling coil/filter frame 20” x 20” x 6-1/4” deep (accepts 16 x 20 x 1 filter),
Return air connection is (14 x 18). Use with 30 & 50 series
70-CCFF-001
cooling coil/filter frame 20” x 25” x 6-1/4” deep (accepts 16 x 25 x 1 filter,
Return air connection is (14 x 23). Use with 70 series
100-CCFF-001
cooling coil/filter frame 20” x 25” x 6-1/4” deep (accepts 16 x 25 x 1 filter,
Return air connection is (14 x 23). Use with 100 series
Summary of Contents for MaxAir 100e P2
Page 43: ...Page 43 WIRING DIAGRAM P2 UNITS...
Page 44: ...Page 44 WIRING DIAGRAM P3 UNITS...
Page 45: ...Page 45 WIRING DIAGRAM P2 UNITS ALTERATIONS HEAT PUMP OPTION...
Page 46: ...Page 46 WIRING DIAGRAM P3 UNITS ALTERATIONS HEAT PUMP OPTION...
Page 51: ...Page 51 FAN COIL DIMENSIONS AND RETURN AIR SIZE LOCATION...
Page 52: ...Page 52...
Page 53: ...Page 53...
Page 54: ...Page 54...
Page 55: ...Page 55...
Page 56: ...Page 56...
Page 61: ...Page 61 2 AND 2 5 TON EVAPORATOR COIL SIZES 70 IPCE 24 30A...
Page 62: ...Page 62 SAMPLE PIPING SCHEMATICS...
Page 63: ...Page 63...
Page 64: ...Page 64...
Page 65: ...Page 65...