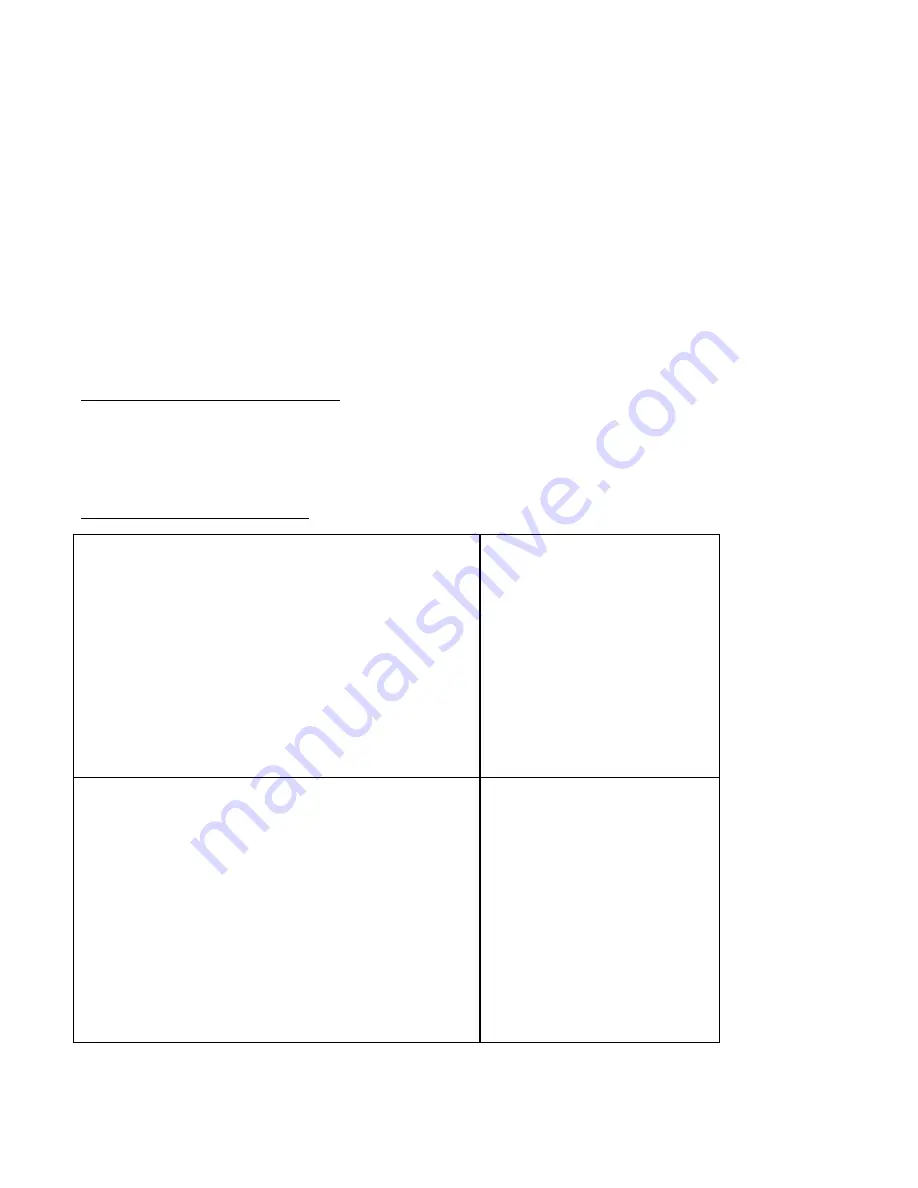
Page 37
minimum open position and the cooling condenser circuit is energized provided field
supplied freeze thermostat is closed.
3.
After Time delay fan motor starts at value selected by installer and corresponding “Y1” or
“Y1” input
4.
Only upon a call for additional zone(s), after the time delay and based on a proper plenum
sensor reading will the fan value increase to “Y2” value.
5.
If the plenum temperature drops the sensor will cycle the condenser to maintain the
temperature above the frost point.
6.
When room temperature is satisfied, thermostat breaks connection between “R”, “G” and
“Y1” wires. The off zone damper(s) returns to the minimum open position.
7.
When all zone temperature are satisfied the cooling condenser circuit is de-energized, the
zone dampers revert to the full open position and the fan shuts off after the programmed
purge delay (or switches to continuous run speed when continuous run (Fan On) is
employed at the thermostat).
Continuous Run Cycle (Fan ON)
1. Zone thermostat connection is made between (“G” terminal) green and (“R” terminal) red.
2.
Corresponding zone damper opens fully, the other zone damper, if not calling, powers to
minimum position.
3.
Continuous run relay is energized; fan input value operates on continuous run speed.
Wiring for 2 Stage Operation
Accomplished through 2
‐
zone board.
Provide W wire from wall thermostat to connection
on board.
Jumper must be removed from DCC7235S board
between W1 and W2 at H7 and Switch 1 on SW1
must be set to 1&2 STG HT (factory setting).
Zone board controls fan coil speed to W1 level for 1
st
20 minutes of a heat call after which it increases to
W2 air flow level.
Both settings yield air flow levels defined in Table A
& Table B for W1 & W2.
Not possible on 2
‐
zone board.
Only has the capability for
single air flow level.
Both settings yield air flow
levels defined in Table A &
Table B for Y2 (with H6
jumper in place).
Accomplished through 3
‐
zone board.
Provide W wire from wall thermostat to connection
on board.
Jumper must be removed from DCC7235S board
between W1 and W2 at H7 and Switch 1 on SW1
must be set to 1&2 STG HT (factory setting).
The 3 zone board will provide the logic for staging.
Both settings yield air flow levels defined in Table A
& Table B for W1 & W2.
Through 3
‐
zone board.
Must provide Y wire from wall
thermostat to connections on
board.
Jumper must be removed
from DCC7235S board
between Y1
‐
Y2 at H6.
The 3 zone board will provide
the logic for staging.
Both settings yield air flow
levels defined in Table A &
Table B for Y1 & Y2.
Summary of Contents for MaxAir 100e P2
Page 43: ...Page 43 WIRING DIAGRAM P2 UNITS...
Page 44: ...Page 44 WIRING DIAGRAM P3 UNITS...
Page 45: ...Page 45 WIRING DIAGRAM P2 UNITS ALTERATIONS HEAT PUMP OPTION...
Page 46: ...Page 46 WIRING DIAGRAM P3 UNITS ALTERATIONS HEAT PUMP OPTION...
Page 51: ...Page 51 FAN COIL DIMENSIONS AND RETURN AIR SIZE LOCATION...
Page 52: ...Page 52...
Page 53: ...Page 53...
Page 54: ...Page 54...
Page 55: ...Page 55...
Page 56: ...Page 56...
Page 61: ...Page 61 2 AND 2 5 TON EVAPORATOR COIL SIZES 70 IPCE 24 30A...
Page 62: ...Page 62 SAMPLE PIPING SCHEMATICS...
Page 63: ...Page 63...
Page 64: ...Page 64...
Page 65: ...Page 65...