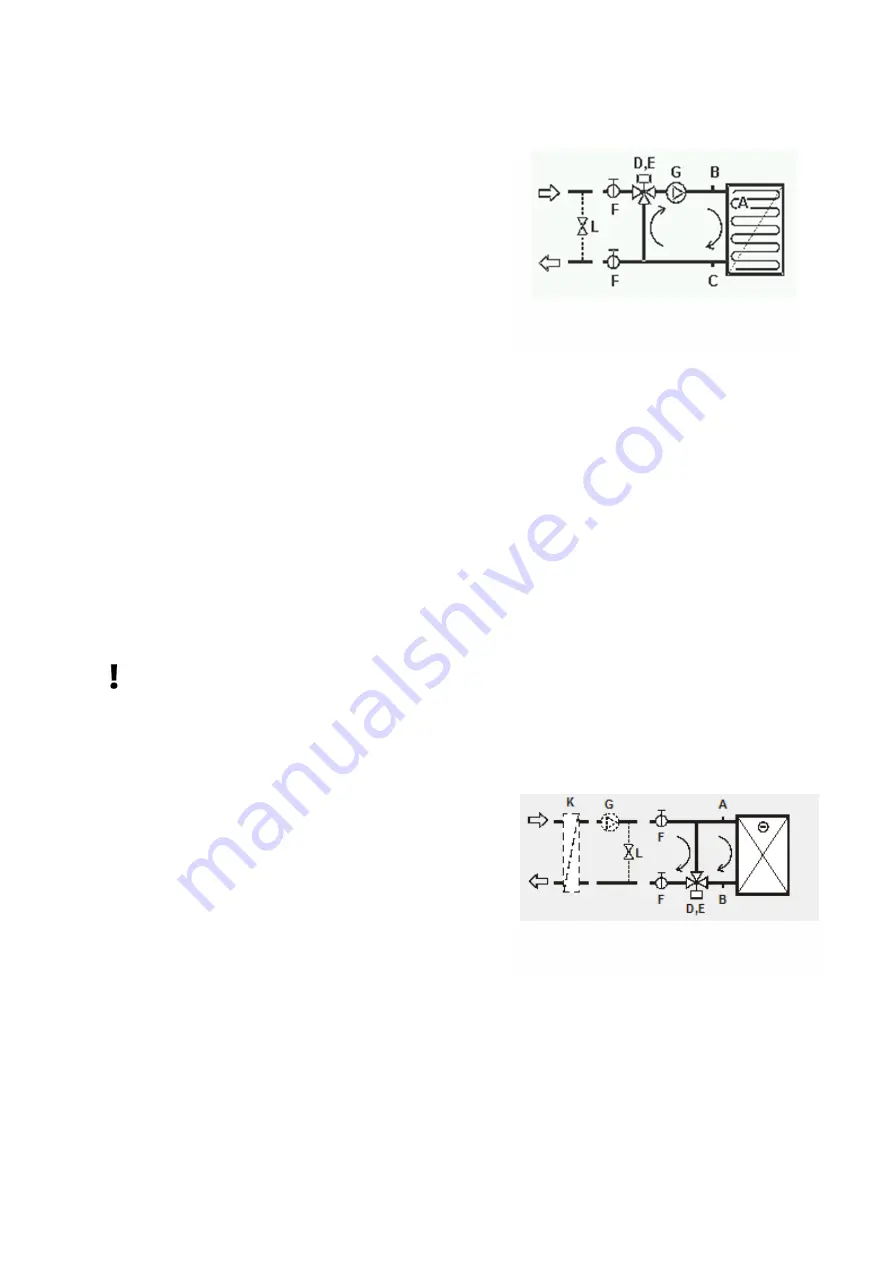
22
2.10.
Connecting hot-water heating coil to a heating water supply
When connecting the water heating coil follow the instructions below:
1.
Maximum allowable heating medium temperature is
110°C. The max. operating pressure is 1.0 MPa.
2.
To ensure correct performance of the heating coil
hydraulic kit, fit the system with a pump with sufficient
performance that covers the entire pressure drop. The
pump supplied with the hydraulic kit is only designed to
cover pressure drop of the water heating coil!
3.
If the equipment is not equipped with a shutoff damper
on outside air intake (e1) put a tight shutoff damper in the
outside air inlet duct (we recommend a type with a spring
return actuator, closing on power interruption).
4.
Fit a strainer in the equipment heating system inlet pipe.
5.
When using a 3-way mixing, we recommend installing a
short circuit according to the diagram in Selection software (Operation point > Water heating coil).
When connecting the pre-heater, observe the following principles:
1.
The maximum permitted temperature of the heating fluid is 110°C and operating pressure is up to
1.0 MPa.
2.
Antifreeze must be used for circulation in all units fitted with the thermal fluid air pre-heater.
3.
The heating system must have a sludge filter fitted in the inlet to the unit.
4.
When a 3-way mixing manifold is used, we recommend installing a short-circuit by-pass.
Fluid pre-heater power control:
1.
The pre-heater is used for protecting heat recovery exchangers from freezing.
2.
The RD5 control system has a power control output.
3.
Pre-heater control is continuous.
4.
Pre-heaters are installed by service technicians.
For the wiring diagram see the selection software (Controls > Wiring diagram) or service
documentation.
2.11.
Connecting chilled-water cooling coil to a chilled water supply
When connecting the water cooling coil follow the instructions below:
1.
Fill the water cooling coil with a non-freezing mixture
with sufficient low-temperature resistance. Or drain the
coil for time period with risk of temperatures below
+3°C.
2.
The max. operating pressure is 1.0 MPa!
3.
Fit a strainer in the equipment chilled water system
inlet pipe.
2.12.
Connecting direct-expansion cooling coil
When connecting the DX cooling coil follow instructions of your supplier of condensing unit and
refrigeration system.
2.13.
Installation and connection of manometers for constant flow and
constant pressure feature
When installing the accessory mechanically and connecting its electronics please follow the guide
enclosed to this optional accessory.
A: frost thermostat; B: drain valve; C: drain
valve; D: mixing valve; E: actuator; F: ball
valve; G, pump L, short-circuit bypass
A: strainer; B: strainer; D: 3-way ball tap;
E: servo drive; F: ball valve; G: pump; L: short-
circuit by-pass; K: water / ethylene glycol coil