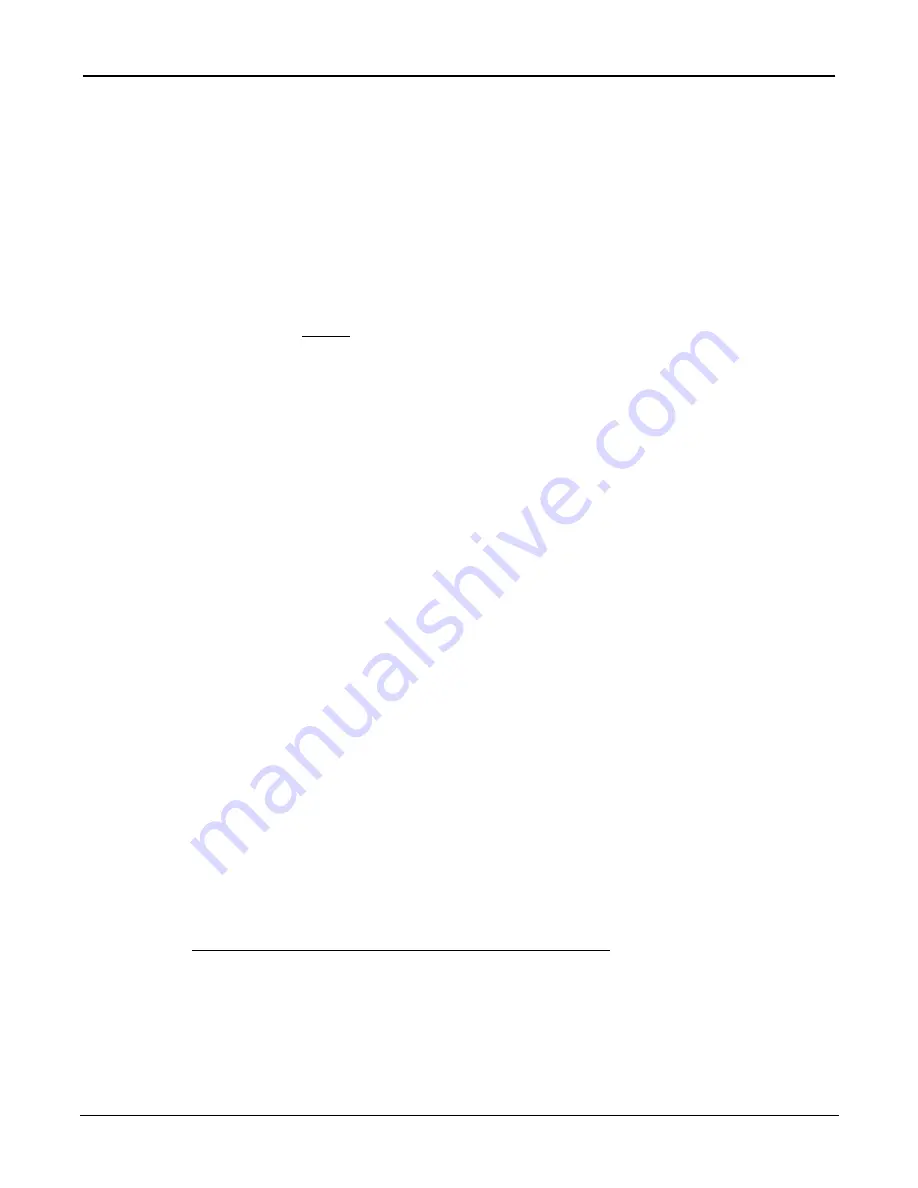
PCBRM100 User’s Guide
Chapter 5: Process Development
4101.00.902
5-4
5.1
Process Advice
1)
Make sure you are running the correct program
2)
You should never have to reach into the machine to change a flow well or nozzle
3)
If a flow well is “stuck” flow solder for 15-30 seconds. Shut off the solder. The flow well
should remove easily.
4)
For barrel cleaning Pass 2 apply flux as this will help to draw solder up from the bottom of
the barrels.
5)
Check that the flow well is fully seated (metal to metal sound). If it is not the board may hit the
top of the flow well.
6)
If you forget to attach TC#1 or if the Kapton tape falls off the board will come out of the pre-
heater after 150 seconds and the process will stop. 150 seconds is based on the typical time
of 90 seconds to reach 150C plus a 60 second time cushion. The 150 seconds is program-
mable/adjustable.
7)
Possible reasons for a nozzle alignment (laser) failure.
a. You installed the wrong nozzle
b. The nozzle was installed too far from square
c. Nozzle not installed correctly (not fully seated, wrong orientation)
8)
Solder pump override allows the operator to change the solder pump process setting in the
run screen. The programmed pump process setting is shown to let the operator know the
magnitude of change they are making. The override setting applies for as long as the opera-
tor remains in the run screen. As soon as they exit the run screen the pump process setting
reverts to the programmed setting. Note: the need to increase pump speed to get the desired
flow indicates that additional solder may be required.
9)
Use caution when manually increasing the pump speed to high levels (in excess of 65%).
Move the bottom hot gas jets away from the flow well so solder does not try to enter the jets.
If a jet becomes closed by solder, the heating element may burn out.
10)
When doing solder pot maintenance move the hot gas jets out and away as far as possible
from the pot. Always remember to move the jets back in as close to the flow well as possi-
ble. Failure to move the jets back in will cause process failure.
11)
The RJ45 connector has tight fitting plastic locating pins. Use caution removing this compo-
nent as the board is not locked down and will tend to lift.
12)
Be sure to take note of the center support bar instructions in the programs. If the center sup-
port bar is not moved away from the flow well and the angled portion of the hot gas jets, the
center support bar will hit and the process will fail.
Summary of Contents for PCBRM100
Page 1: ...PCBRM100...
Page 2: ......
Page 4: ...PCBRM100 User s Guide 4101 00 902...
Page 6: ...PCBRM100 User s Guide Chapter 1 Introduction Overview 4101 00 902 1 2...
Page 16: ...PCBRM100 User s Guide Chapter 1 Introduction Overview 4101 00 902 1 12...
Page 17: ...PCBRM100 User s Guide Chapter 1 Introduction Overview 4101 00 902 1 13 Left Side...
Page 18: ...PCBRM100 User s Guide Chapter 1 Introduction Overview 4101 00 902 1 14 Center Right Side...
Page 19: ...PCBRM100 User s Guide Chapter 1 Introduction Overview 4101 00 902 1 15 Rear...
Page 20: ...PCBRM100 User s Guide Chapter 1 Introduction Overview 4101 00 902 1 16...
Page 22: ...PCBRM100 User s Guide Chapter 1 Introduction Overview 4101 00 902 1 18...
Page 23: ...PCBRM100 User s Guide Chapter 1 Introduction Overview 4101 00 902 1 19 Left Side...
Page 24: ...PCBRM100 User s Guide Chapter 1 Introduction Overview 4101 00 902 1 20 Center...
Page 25: ...PCBRM100 User s Guide Chapter 1 Introduction Overview 4101 00 902 1 21...
Page 26: ...PCBRM100 User s Guide Chapter 1 Introduction Overview 4101 00 902 1 22 Laser Warnings...
Page 27: ...PCBRM100 User s Guide Chapter 1 Introduction Overview 4101 00 902 1 23 Front...
Page 28: ...PCBRM100 User s Guide Chapter 1 Introduction Overview 4101 00 902 1 24 Rear...
Page 30: ...PCBRM100 User s Guide Chapter 2 Facility Requirements 4101 00 902 2 2...
Page 32: ...PCBRM100 User s Guide Chapter 2 Facility Requirements 4101 00 902 2 4...
Page 33: ...PCBRM100 User s Guide Chapter 3 Start Up 4101 00 902 3 1 3 Start Up 3 Start Up 3...
Page 34: ...PCBRM100 User s Guide Chapter 3 Start Up 4101 00 902 3 2...
Page 38: ...PCBRM100 User s Guide Chapter 3 Start Up 4101 00 902 3 6...
Page 40: ...PCBRM100 User s Guide Chapter 4 Software Overview 4101 00 902 4 2...
Page 90: ...PCBRM100 User s Guide Chapter 4 Software Overview 4101 00 902 4 52 Adjustments...
Page 96: ...PCBRM100 User s Guide Chapter 4 Software Overview 4101 00 902 4 58...
Page 118: ...PCBRM100 User s Guide Chapter 4 Software Overview 4101 00 902 4 80...
Page 120: ...PCBRM100 User s Guide Chapter 5 Process Development 4101 00 902 5 2...
Page 158: ...PCBRM100 User s Guide Chapter 6 Maintenance 4101 00 902 6 2...
Page 180: ...PCBRM100 User s Guide Chapter 6 Maintenance 4101 00 902 6 24...
Page 182: ...PCBRM100 User s Guide Chapter 7 Error Messages 4101 00 902 7 2...