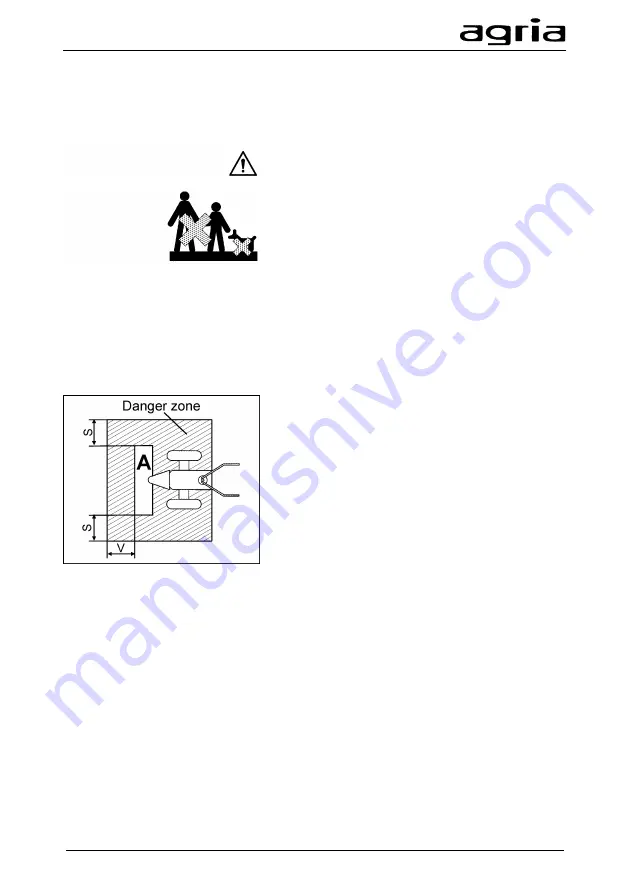
4 Commissioning and Operation
Hydrostatic Implement Carrier
agria 5900 Bison
41
Danger zone
Observe the operating instructions of the
implements and the safety instructions.
Staying in the danger zone of the machine
during startup and operation is not permit-
ted.
If the operator notices that people or animals are
in the working area, the machine must be
switched off immediately and not restarted until
this area is clear.
The user is responsible for third parties in the
working area (entire area to be worked on).
The hazard zone differs with the installed imple-
ment (A) (for work and transport drive):
V
S
Mower head
2 m
1 m
Rotary tiller
*25 m
*25 m
Flail tiller
*20 m
3 m
Safety tiller
*10 m
2 m
Belt rake
2 m
2 m
Baler
3 m
2 m
Sweeping machine
3 m
3 m
Snowplough
2 m
1 m
Reverse tiller
2 m
2 m
Rotary harrow
2 m
2 m
Path maintenance unit
2 m
2 m
Wild plant brush
3 m
3 m
Transport ride with * only 3 m