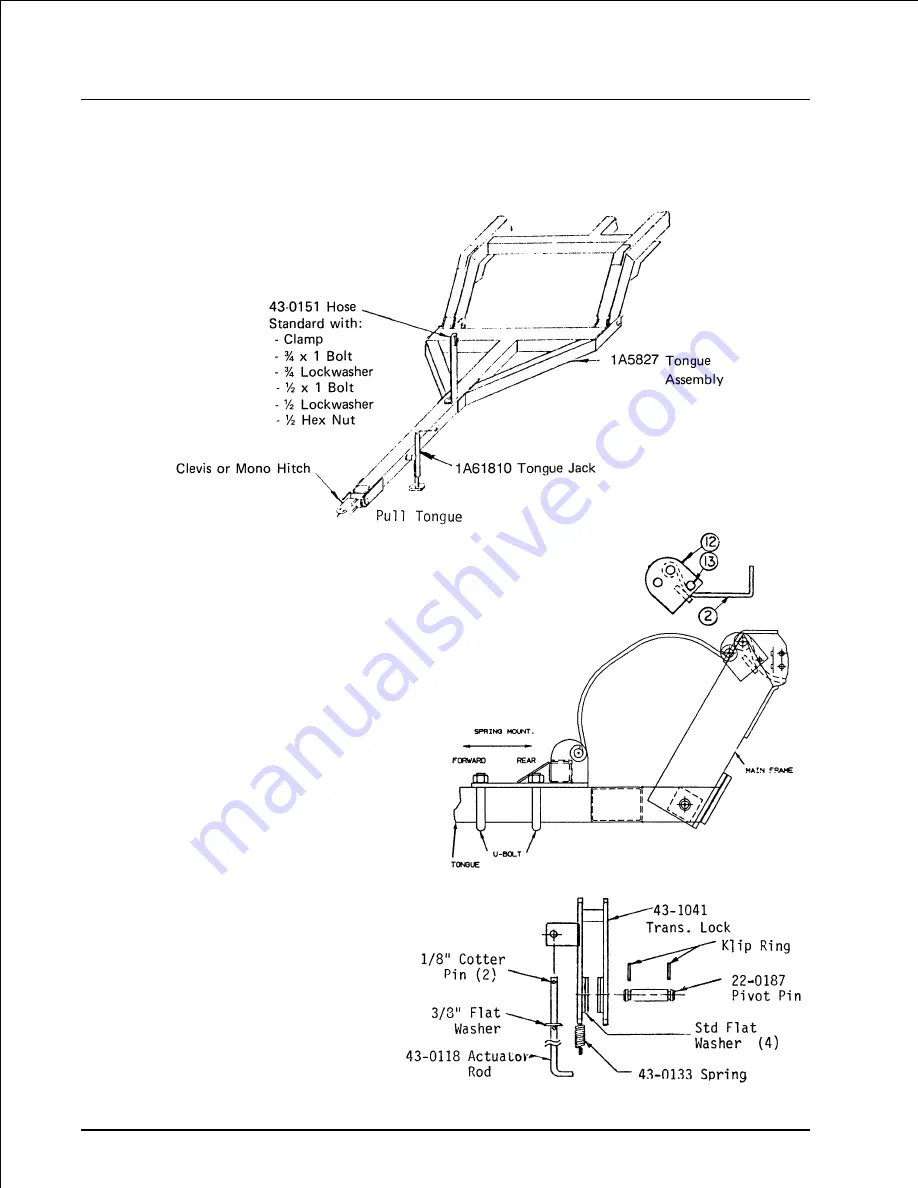
ASSEMBLY
PULL TONGUE
Attach the tongue to the main frame using tongue
pull pins and spring pins. Attach the tongue jack and
the hose standard.
TRANSPORT LEVEL
For stability when raising or lowering the mulcher
during set-up, the transport mechanism should be
installed. Item 12 has to be rotated until the inner
block is against the mounting spring, item 2. The
1/2” x 5-1/2” bolt (item 13) passes on the opposite
side of the spring mount, sandwiching it between
the bolt and the inner block. Item 12 should not be
able to rotate.
By loosening the u-bolts on the tongue, the mount
assembly may be adjusted until the machine is level
in transport. For leveling in transport, see page 13.
AUTOMATIC TRANSPORT LOCK
Assemble hardware as shown.
28
Summary of Contents for Glencoe ULTRAMULCHER UM43 21'
Page 1: ...Glencoe UM43 ULTRAMULCHER 21 25 MODELS OPERATOR S MANUAL Form number 1PD784798 July 1998...
Page 2: ......
Page 4: ...NOTES ii...
Page 26: ...NOTES 22...
Page 29: ...25...
Page 46: ...42...
Page 47: ...ASSEMBLY OPTIONAL EQUIPMENT See page 41 for part number and description reference...
Page 48: ...ASSEMBLY OPTIONAL EQUIPMENT...
Page 49: ...ASSEMBLY OPTIONAL EQUIPMENT 45...
Page 52: ...48...
Page 53: ...Glencoe AGCO CORPORATION 4205 River Green Parkway Duluth Georgia 30096 Printed in U S A 49...