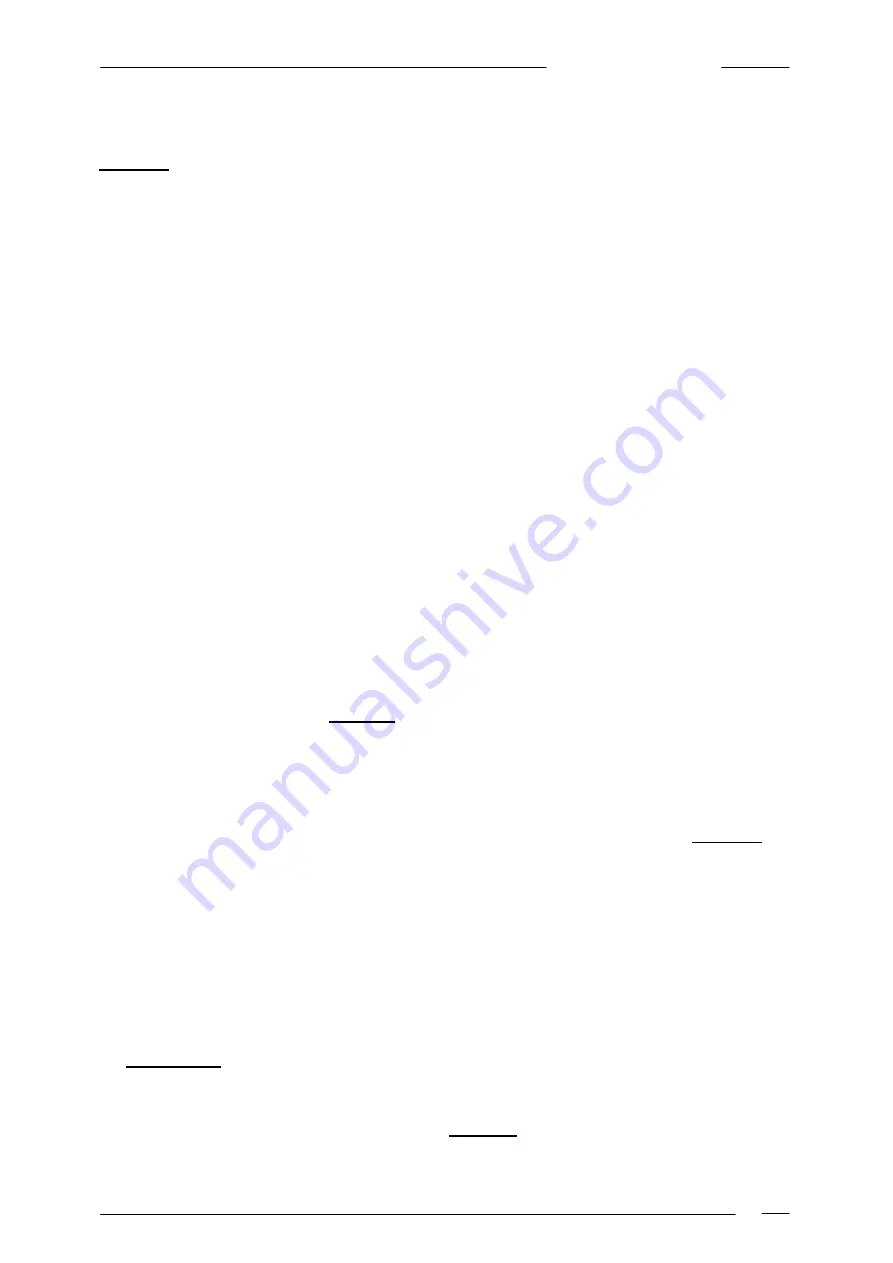
Canadair CL-415
5
Relieve the floats (78) to accept the pylons, and push them onto the float ribs (77). Check that everything
fits correctly, then glue these parts together. Glue the second float shell in place using Stabilit-Express.
Work carefully here, as the floats must, of course, be watertight! Fig. 10.
Fuselage:
we have already mentioned the advisability of sanding back the excess gel-coat in the interests
of saving weight. Drill round the periphery of the air inlets and outlets using a bit of around 1.5 - 2 mm Ø,
and trim them neatly to final size using small files. The wing saddle can also be reduced somewhat: the
flange should be about 6 - 7 mm wide at both sides, and 2 or 3 mm less at the leading edge. The opening
in the top of the stub fin can also be enlarged - see view E. Sand the periphery of the stub fin using fairly
coarse abrasive paper, and also sand the bottom of the fin itself. Check and trim these parts to ensure they
fit accurately. Don’t force the fin onto the stub, otherwise the balsa parts already bonded in may burst!
Section J-J shows all the dimensions for the main undercarriage holes; these must be marked out as
accurately as possible. Start by drilling 1.5 mm Ø pilot-holes (for the struts (11) and (12) the holes must be
at the appropriate angle), then open them up to 3 mm Ø and 2 mm Ø to accept parts (11 + 12). Use two
pieces of 3 mm Ø steel rod to check the position: they should be exactly horizontal and parallel.
Cut the openings in the undercarriage bearer (5) as shown in view G (drill, fretsaw if required), and place
the bearer in the fuselage. Both ends must be cut at an angle as shown in section J-J. It must be possible
to fit the bearer low enough to allow the steel rods to be pushed into the channels in the component. Once
the bearer is correctly located, remove it from the fuselage. Make up the aluminium straps and drill 1.5 mm
Ø holes in the bearer as shown. Roughen the joint area with coarse abrasive paper, and glue the bearer in
place using thickened laminating resin. Fit the steel rods. The half-former (4) can be glued in place at the
same time. The half-former (3) is not strictly essential.
Sand back the solder joint areas of the undercarriage wires (9) and (10) to bright metal, install them, align
them carefully, and tighten the aluminium straps to secure them. The strut (11) can now be fitted in the
fuselage side, aligned, and bound to parts (9) and (10) using soft binding wire. Apply flux to the joints on a
paintbrush, then solder the parts together using a heavy-duty soldering iron (approx. 100 W). Make sure
the joints are strong. Install both parts (12), secure them with binding wire, align them and solder the joints
in the same way. To remove the undercarriage the straps must be undone. Clean the soldered joints with
paint thinners, and file the joints smooth where necessary.
Section J-J shows the guide sleeves for parts (11 + 12) which are cut from part 20. Carefully enlarge the
holes in the fuselage to 3.2 mm Ø. Slip pieces of part (20) in the fuselage side, install the undercarriage
and tighten the strap retaining screws. Now carefully glue the guide sleeves to the fuselage side using
epoxy resin. Cut off the excess sleeve length using a sharp chisel or plane blade.
Landing loads are absorbed by the lower wires (9 + 10) alone, whereas parts (11 + 12) are dummies; they
must be free to slide into the guide sleeves when the undercarriage is compressed. See Figs. 11 to 13.
Section A-A shows the noseleg support; these parts are best glued using laminating resin, leaving the
guide sleeve (8) projecting on the underside. The sleeve must project out of the fuselage! From the brass
sheet supplied make up a U-shaped strap as shown and install it using two M2 screws. Drill it out from the
underside using a 3 mm Ø drill. Use a length of 3 mm Ø rod as a guide for soldering the collet (the M3
thread in the collet must face the tail).
Place the noseleg support in the fuselage, check that it fits properly and trim if necessary. If everything is
correct, tack it in place using thin cyano, then apply plenty of epoxy round the joints. Take care that the
guide sleeve is truly vertical.
Sand the soldered joints of the noseleg unit smooth, align it and solder the parts together thoroughly.
At this point you have a decision to make. The kit is supplied with perfectly serviceable wheels, but
nowadays there are significantly lighter alternatives available, and every gramme saved is valuable. If you
wish to buy new ones we recommend Sullivan Sky Lite wheels, Order No. 7353/02 (45 mm Ø) and
7353/08 (64 mm Ø).
The height of the main undercarriage is fixed, but the height of the noseleg depends on the wheel diameter
- the fuselage must stand horizontally on the workbench!
Glue the wing retainer plates (2) together in pairs using epoxy (after lightening the plates if possible), then
glue them in the fuselage using thickened resin. Position the wing accurately on the fuselage, and mark
the position of the dowel holes. Drill 3 mm Ø pilot-holes, then open them up to 5 mm Ø. Fit the locating
dowels in the wing, and check that the wing can be fitted into the fuselage. Adjust the dowel holes as
required until a perfect fit is obtained. The next step is to mark the position of the holes for the M5 screws:
align the wing accurately on the fuselage, tape the wing in place, then drill 4 mm Ø holes, taking care to
drill at right-angles. Remove the wing.
Now run an M5 tap through the holes, harden the wood with thin cyano and re-cut the threads. Open up
the holes in the wing to 5 mm Ø, and countersink the holes for the screw-heads. Harden the material with
thin cyano in the usual way. Assemble the servo mounts from parts (21) to (24), taking care to produce a
handed pair. The rudder linkage should be on the right-hand side of the fuselage. Cut the slots for the
“snakes” in the stub fin as shown in view E, and file them out at the appropriate angle. The snake outers
must not bend sharply at this point - this applies in particular to the rudder. Prepare the support plate (95)