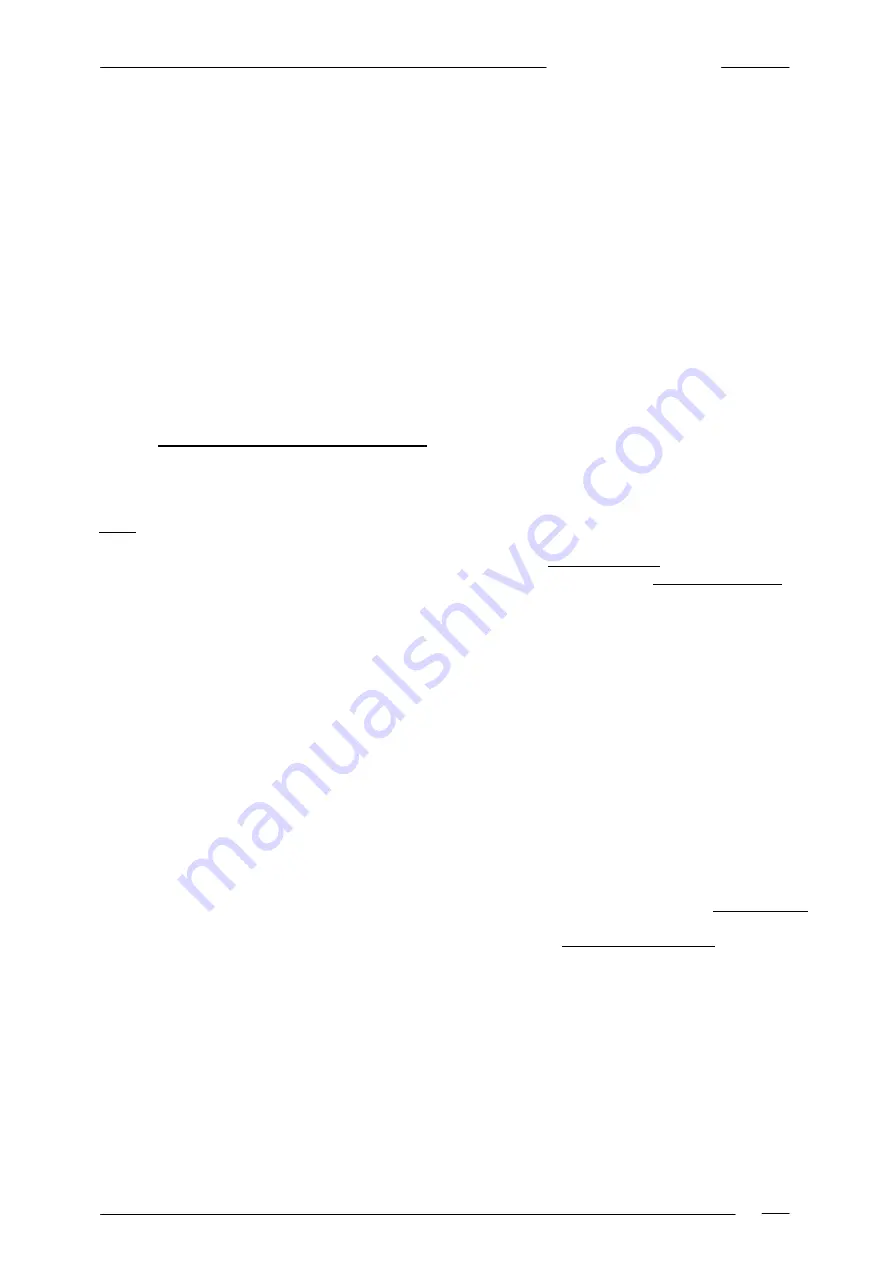
Canadair CL-415
4
(61) to the main spar by running thin cyano along the joint. Slide a tapered-section balsa strip under the
front edge of the leading edge sheeting (61), as shown in section F-F, so that it is pushed up against the
ribs; glue the ribs to part (61). Sand the underside of the false leading edge (70) at a slight angle (see
section F-F), place it in position and attach it to part (61) and the ribs using thin cyano.
Glue the in-fill block (59) and the aileron horn block (60) in place, and install the servo mount (66). Glue the
top trailing edge panel (51) in place using thickened laminating resin; press it down using jig strips as
shown in section D-D, and leave the resin to set hard.
Remove the wing framework from the building board and trim the false leading edge (70) to follow the top
camber of the wing section. Cut the tip and root sheeting panels from part (51) and trim them carefully to fit
between parts (55) and (61). Before gluing them in place check the plan view (tip ribs at right-angles!).
Glue the capstrips (50) to the unsheeted ribs. Caution - two of the capstrips are 10 mm wide - see plan.
Fit the pushrod connector on the aileron servo output arm (check the servo is at neutral first), then install
the servo mount and servo - see section F-F. Cut one 25 mm wide capstrip from part (51), and cut a slot in
it at this early stage to accept the pushrod guide sleeve (25) - see section F-F and the wing plan view. Cut
an opening about 8 mm in diameter under the pushrod connector to provide access for the allen key.
From part (60) make the reinforcements for the motor nacelle mountings and the supports for the dowels
(88) - see sections D-D and E-E. Parts (66) to (69) are plywood reinforcements for the wing ribs (57); trim
them to fit and glue them in place as shown on the plan.
It is important that there should not be a gap between the root ribs when the wing panels are joined, and
this means that the root rib should be fitted very carefully at this stage. The main point is that the root rib
must be at right-angles when viewed from above. The slots for the dihedral braces (62) and (63) are best
cut using a hacksaw blade. Fix the dihedral braces in place using plenty of glue. Thread the prepared
motor wiring and servo leads through the wing structure. The top wing leading edge sheeting (61) can now
be attached using white glue. Press the panel into place using jig strips as shown in section D-D. Working
from the plan, mark the position of the 4 mm Ø holes for attaching the motor nacelles, and drill them with a
sharp drill bit (using a pillar drill for preference). Open up the holes in the bottom wing sheeting (51) to 10
mm Ø.
Mark the position of the holes for the float pegs on the ribs (57) from underneath, using part (76) as a
guide. Lay the wing on the drilling table, and drill the 3 mm and 4 mm Ø holes from the underside, as
shown in section B-B. Run thin cyano into all the holes to harden the wood, allow it to cure, then run the
drill through again. Refer also to Figs. 1 to 4 during this stage.
Mark the position of the ailerons on parts (55) top and bottom as accurately as you can, noting the width of
the slot required for the lining strips (73) as shown in section F-F. Cut out the slots neatly using a sharp,
pointed-tip balsa knife; see Fig. 5.
The second wing panel can now be assembled in exactly the same way, but initially without the top leading
edge sheeting (61); this is only attached after the wing panels have been glued together.
Initially offer up the wing panels “dry” (no glue), and check that they fit together really accurately; trim if
necessary. Protect the building board with plastic film and pin down one wing panel. The panels are joined
using thickened laminating resin. Join the panels, and carefully remove all excess glue using kitchen paper
where it is squeezed out of the joint. Allow the glue to cure fully, and only then glue the top leading edge
sheet panel (61) in place - see Fig. 6. Cut out the top sheeting panels from part (51), trim and glue them in
place, and install the capstrips (50). Caution: a 10 mm wide capstrip must be fitted where the boundary
layer fence is to be located.
Remove the wing from the building board, glue the leading edge (71) to the structure and carefully sand it
to section as shown in the pictures and on the plan. Cut the openings as indicated in the illustrations and
on the plan. Attach the tapered-section balsa strips (72) to the tip ribs, mark the line of the wing section on
them and cut off the excess. Mark the position of the holes for the M4 screws and drill them at right-angles
to the mating surface (= tip rib). Run thin cyano into the holes, then run the drill through again. Parts (72)
can now be pressed against the tip rib; mark the position of the holes using a 4 mm Ø drill bit. Drill the hole
itself using a 3.2 mm Ø bit, then cut an M4 thread using the appropriate size of tap. Harden the threads
with thin cyano, then run the tap through again. Fix parts (72) in place using M4 screws, and sand these
parts back flush with the wing surface. The winglets are made as shown on the plan; Fig. 8 shows the
correct profile.
Cut out the float half-shells (78) along the marked lines, and check that the pairs of shells fit together
accurately. If the float ribs (77) are not flat, straighten them by gluing a strip of wood to them. Inset the rib
in one shell (78) and glue it in place using Stabilit-Express - see Fig. 9.
Glue the balsa sheet cladding panels (75) to both sides of the float pylons (76), then sand them to the
profile shown. Relieve parts (75) to form a socket for the M4 nuts. Fit the float pegs (dowels) (32) in the
holes in the wing, apply a little glue in the recesses in parts (76) and fit the pylons on the projecting dowels.
When the glue has set hard, push the M4 nuts into place, secure them with the M4 screws, then glue them
to the float pylons (76 + 75) using Stabilit-Express.