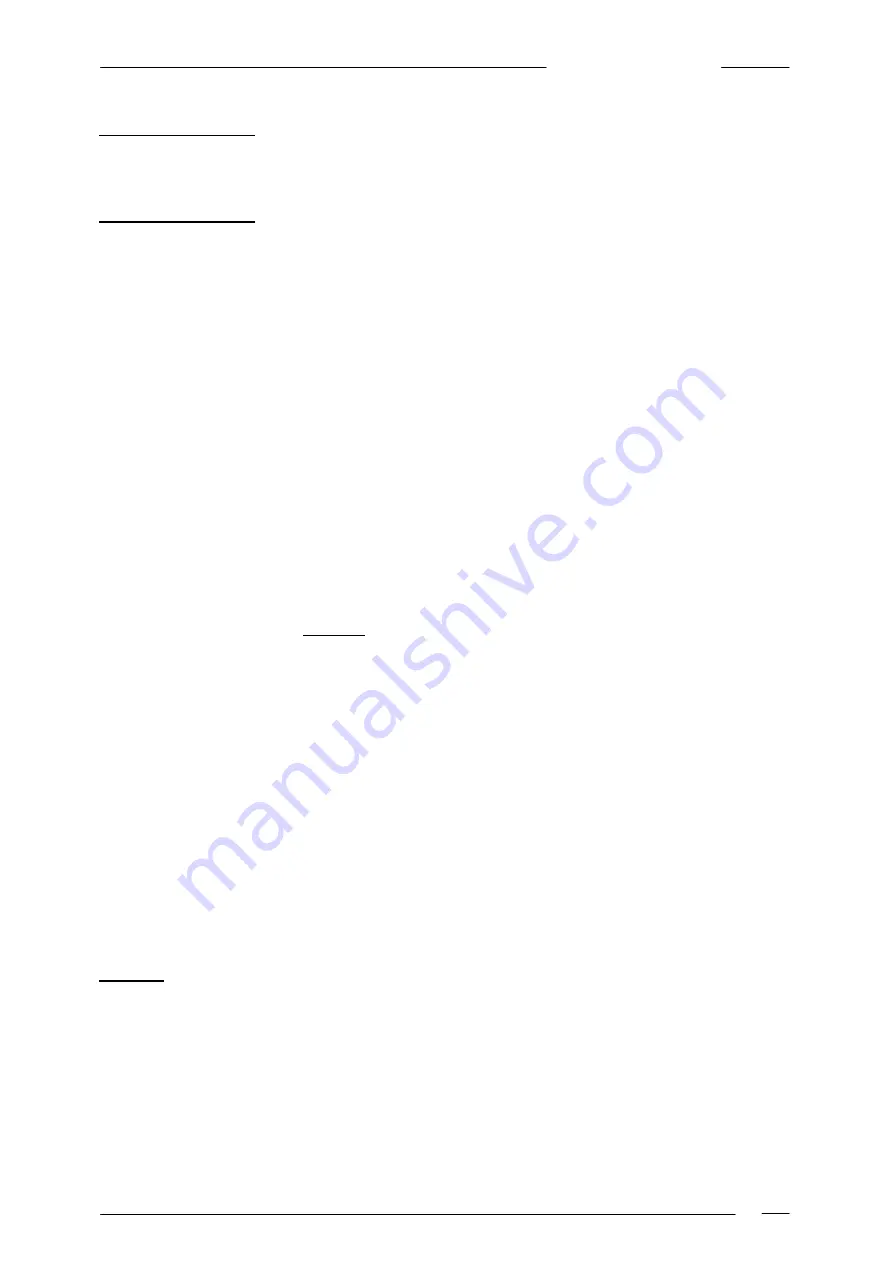
Canadair CL-415
2
10-cell power system:
1.) Race 400 / 6.0 V with gearbox
2.64 : 1
7121/06
with propeller
8.5 x 6
7229/28
12-cell power system:
1.) Race 400 / 6.0 V with gearbox
2.64 : 1
7121/06
or
3.00 : 1
7121/07
with propeller
8.5 x 6
7229/28
2.) Race 400 / 7.2 V with gearbox
2.23 : 1
7120/05
or
2.64 : 1
7120/06
with propeller
8.5 x 6
7229/28
For the 10-cell power system we recommend the Micro-Mos mc-410 speed controller, Order No. 7019/34,
with the EMF brake switched off. For the 12-cell system a different controller should be used. Make sure it
features a suitably rated BEC system and a switchable EMF brake.
In this model the whole power system is very highly stressed, and to ensure reasonable motor life we
strongly recommend that you carry out the following work:
Use the motor timing adjustment tool, Order No. 7329/34 to rotate the rear bearing plate through 20° to 30°
in the opposite direction to shaft rotation. In linear terms this means a distance of 5 to 7 mm, measured at
the motor can.
Dismantle the gearboxes. Originally these gearboxes featured a glued brass bush (hub for plastic output
gear), but in later models the bush is made of steel. If your gearboxes have the earlier brass bush, it is
necessary to bond the output gear to the hub: carefully pull the output gear almost off the hub (don’t
remove it entirely). Moisten the bush with a few drops of Loctite adhesive No. 601 or 603, then push the
gear back onto it. This joint will never fail. At the same time you may wish to glue the ballraces in the
housing with a drop of Loctite (take care!).
Lubricate the gears with a little high-viscosity (thick) grease, e.g. titanium grease (for helicopters), then re-
assemble the gearboxes.
The motors should also be run-in: connect them to the speed controller and operate the controller using a
servo tester. Run the motors under minimal load (e.g. with a 6 x 5” electric prop, Order No. 7228/11) until
they have accumulated about 10 to 15 minutes’ running; the flight propellers can then be fitted. During this
period there should be a steady decline in sparking at the brushes. It is important that the motors should
run at the same speed; to set this up you will either need four hands or a “T”-mount consisting of hardwood
rails. The plan shows how both motors are wired up (the wiring is later threaded through the wing
structure), but you can use the cables to connect both motors; speed measurements only make sense if
both motors are running simultaneously. Do balance the propellers as accurately as you can. If the motors
run at different speeds, adjust their timing using the adjustment tool so that the speed difference is
acceptable (+/- 100 - 150 rpm). If it proves to be impossible, either buy a third geared motor or a bare
motor, with or without gear set. This gives you a much better chance of achieving perfectly synchronous
running.
When you are satisfied, attach the suppressor capacitors to each motor: the absolute minimum is to solder
one capacitor of 0.1 - 1 nF between the motor terminals, plus two more of around 47 nF, one from each
motor terminal to the motor can.
Warning!
the motors will become hot relatively quickly under load. You can check the motor temperature
by hand if the fairings are not in place, and for this reason they should not be fitted until all test-runs have
been completed. Do not run the motors for more than about 20 seconds at a time under static conditions.
Before final installation dismantle the gearboxes, wash them out with white spirit, and lubricate the parts:
use high-quality oil on the ballraces, and high-viscosity grease on the gears. In flight the motors spin at
around 30,000 rpm. After the first two hours of flying open the gearboxes and repeat the procedure. If their
condition is satisfactory, the maintenance intervals can be extended.
Alternative geared motors can also be fitted at the builder’s discretion. Motors such as the Speed 480BB
Race 7.2 V, Kyosho AP 29BB, Permax 400BB with Reisenauer planetary gearbox (approx. 4:1), 8.5 x 6”
propellers and 10 cells are likely candidates. Aim for a propeller speed of around 8300 rpm, and a current
of about 12 - 13 A per motor. With 12 cells the reduction ratio would need to be around 4.5 - 5 : 1.