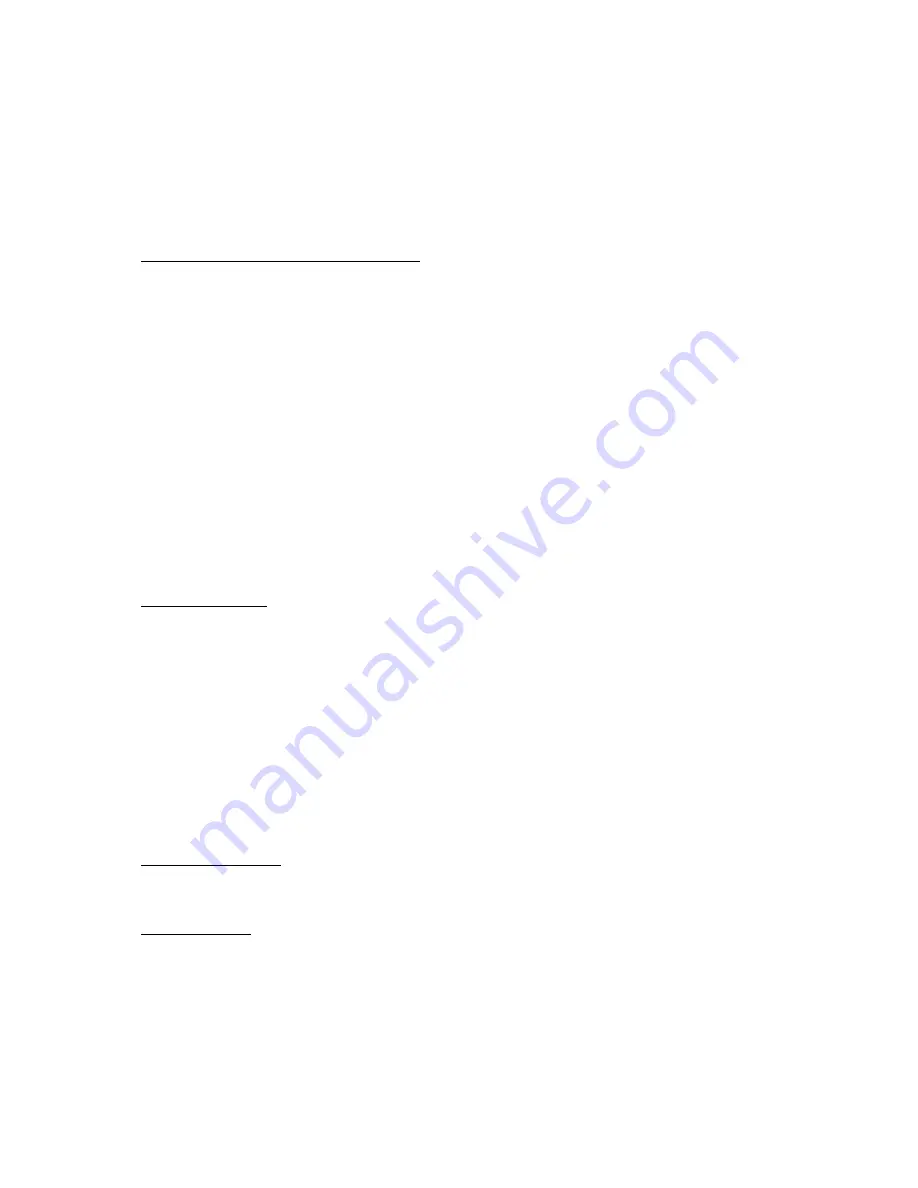
Document Q101, Revision W
(Printout Uncontrolled)
Page 6 of 23
both CND and END divisions. Contributions are solicited from interfacing organizations, as well as customers and
subcontractors. These plans include short and long-term plans for improving quality and customer satisfaction, cycle
time, customer service, training, cost, delivery commitments, product reliability and targets for TL9000 measurements
as defined in the current release of TL9000 QMS measurements handbook. The plans are periodically reviewed to
ensure that the methods and processes involved remain current to the Quality Policy and Objectives, including the
systems methods for disaster recovery. These plans set quality goals to assure continuous improvement of ADTRAN
processes, products and services. (GEN01.1, GEN01.2)
Responsibility, Authority, and Communication
An organization chart is attached as Attachment 2. The Corporate Quality function reports to ADTRAN’s Chief
Executive Officer (CEO). The Corporate Quality organization consists of Quality Assurance, Quality Management,
Customer Quality Engineering, Component Engineering, Reliability Engineering, Product Qualification, Product
Service and Document Control.
The responsibility for quality belongs to each individual within the company. Management provides all personnel with
the training and resources needed to deliver “Quality Performance”. All personnel at ADTRAN have the authority to
stop production if the product quality is suspect. Corporate Quality is responsible for assuring systems and processes
are established that will produce products or services that satisfy or exceed customer expectations. Data collection and
analysis, measurements, audits, corrective actions, and preventative actions are some of the methods used to confirm
that ADTRAN processes result in quality outputs.
The Vice President of Quality is the management representative, and has the authority and responsibility for ensuring
that the QMS is implemented and maintained.
The effectiveness of the QMS is communicated to ADTRAN personnel through, postings, electronic reporting, Town
Hall meetings and departmental meetings. Each manager is responsible for ensuring that responsibilities are defined
and communicated to all associates.
Management Review
The QMS at ADTRAN is in review on a continuous basis. However, specific audits by qualified personnel occur on a
scheduled basis so that each process of ADTRAN’s QMS is audited to ensure continued system effectiveness and
improvement. With recommendations, the result of this audit is published to upper management.
On an annual basis, as a minimum, Corporate Quality shall present data from the QMS to top management for their
review and support of improvements and resource needs. This data includes the review and establishment of the
company quality policy, quality objectives, audit results, customer feedback, process performance, product conformity,
status of preventive and corrective actions, follow-up of actions from previous management reviews, changes that
could affect the QMS, and recommendations for improvement. Minutes of these reviews are generated which may
include any decisions or actions relative to the QMS effectiveness, improvement of product quality, customer
satisfaction or resource needs. These records are maintained by Corporate Quality for a minimum of one year.
(GEN01.1)
6.0
RESOURCE MANAGEMENT
Provision of Resources
ADTRAN management determines and provides the resources needed to implement and maintain the QMS, and
continually improve its effectiveness, and to enhance customer satisfaction by meeting customer requirements.
Human Resources
To ensure the highest quality of products and services at ADTRAN, training programs are developed to match skills
with job functions. All new associates receive orientation, at which time they are made aware of ADTRAN policies,
procedures, and expectations regarding quality and customer satisfaction. Additionally ADTRAN training programs
provide training in soldering, component recognition, ESD, Problem Solving, and Hazardous Materials.
Advanced
Quality Improvement training and product training are offered as well. A proficiency test is administered in some
classes prior to job assignments. Records of all classes and training hours completed are maintained electronically. The
supervisor is responsible for identifying specific regulatory, job-related education and training requirements.
(GEN18.1)