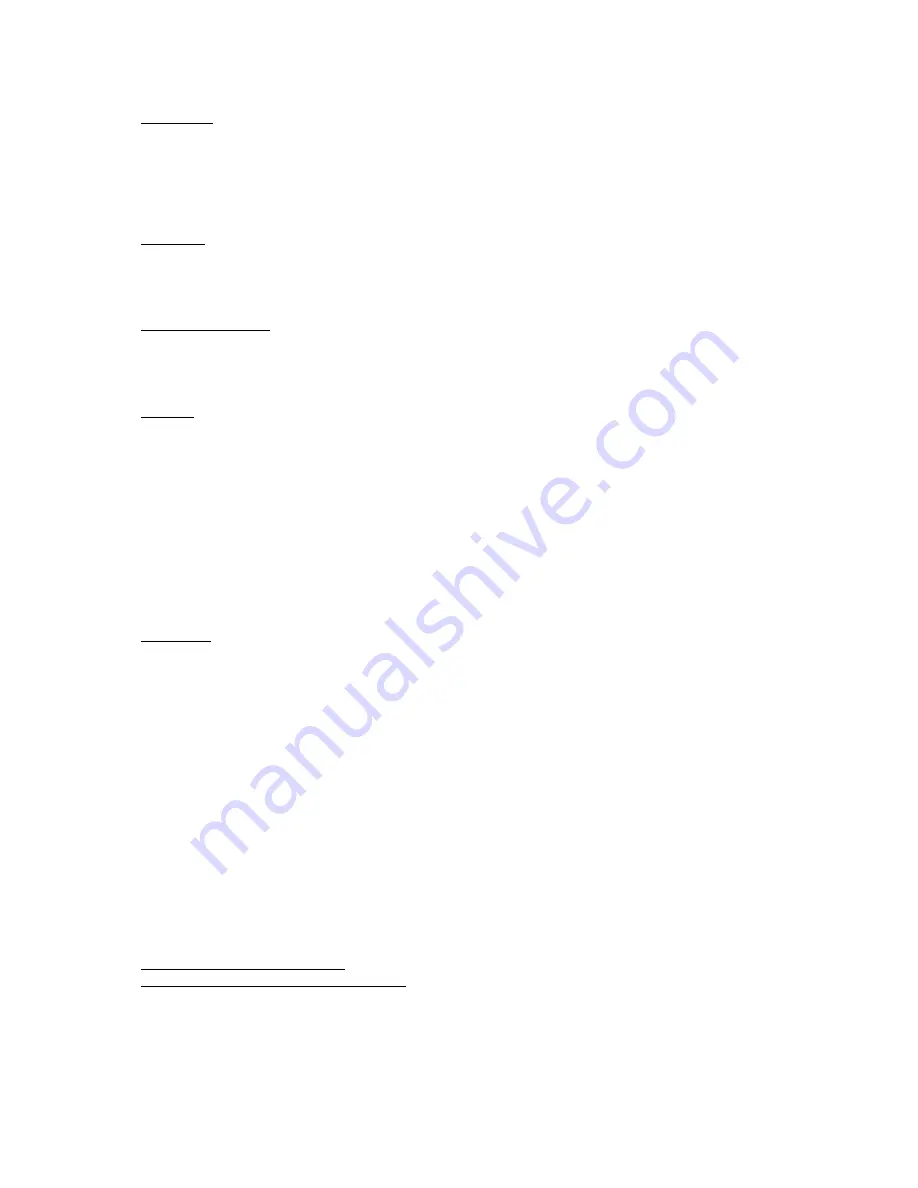
Document Q101, Revision W
(Printout Uncontrolled)
Page 10 of 23
Verification
The responsible engineer develops a Design Verification Test (DVT) to ensure that the design meets the intended
requirements. The results of these tests are recorded and maintained by Document Control. (EN10)
During product qualification testing, user documentation is verified; stress testing, system testing and abnormal
conditions tests are performed. (PQ01)
Validation
In addition to design verification tests, Product Qualification/Validation is performed in accordance with planned
arrangements by the Product Qualification group, which tests the product in a user intended environment. The Product
Qualification department maintains records of the results of these tests. (PQ01)
Release Management
Product Management and Marketing review the product schedules and status. This information is communicated to
the customer in advance. This information aids the customer in planning for upcoming product hardware and software
releases. (EN06, SL02, GEN21.2)
Changes
Any changes to released documentation require approval of the Responsible Engineer, Responsible Manager,
Configuration Control, and the Quality Assurance department, as a minimum. Design Engineering ensures that fixes to
problems are incorporated into future designs. Approval by other departments is on an as-needed basis when affected
by the Engineering Change Order (ECO). Records of the results and review of changes are maintained by the
Document Control department. (GEN05.4)
Documented procedures are established to define change processes and for informing customers of changes that affect
contractual commitments. (EN06, GEN05.4 and SL02)
Component Engineering evaluates, per procedures, all component changes and substitutions to ensure quality product
performance. (GEN0401, PG13)
Purchasing
The quality of finished products and ultimately the customer’s satisfaction depends on procured materials and
subassemblies. Effective supplier selection, procurement, measurement, disposition of discrepant materials, supplier
rating reports, and joint ADTRAN/supplier participation are essential to providing high quality products. Documented
Purchasing procedures are in place to facilitate these activities. (GEN06.1, GEN06.2, GEN06.8, GEN06.11, PG13)
ADTRAN suppliers are evaluated, per documented procedures, by Purchasing, Component Engineering, and Supplier
Quality. Records of these reviews are maintained. (GEN06.11)
Purchase Orders (Pos) are placed using ADTRAN assigned released part numbers that are unique to the specific part.
Purchase Orders include the applicable Quality System to be applied and all contract requirements. The supplier has
the responsibility for ensuring that purchased products meet ADTRAN specifications for quality. (PG13)
All purchased material is confirmed to meet required specifications. This confirmation is by use of sampling plans
either at ADTRAN Component Inspection, Quality Assurance or by ADTRAN Source Inspection. A Dock-To-Stock
program is in place expediting material from suppliers that consistently meets ADTRAN requirements. Purchasing
documents define verification arrangements and the method of product release when product acceptance is determined
to be at the supplier’s facility.
Production and Service Provision
Control of production and service provision
ADTRAN controls the process with documented requirements and audits of the processes. Each work order and each
purchase order for subcontractors specify process requirements. A Bill of Material (BOM) is generated for each work
order. On the Bill of Material, special assembly instructions relating to specific components are written. One item on
the Bill of Material is a drawing specifying the process flow. These drawings are released and controlled by