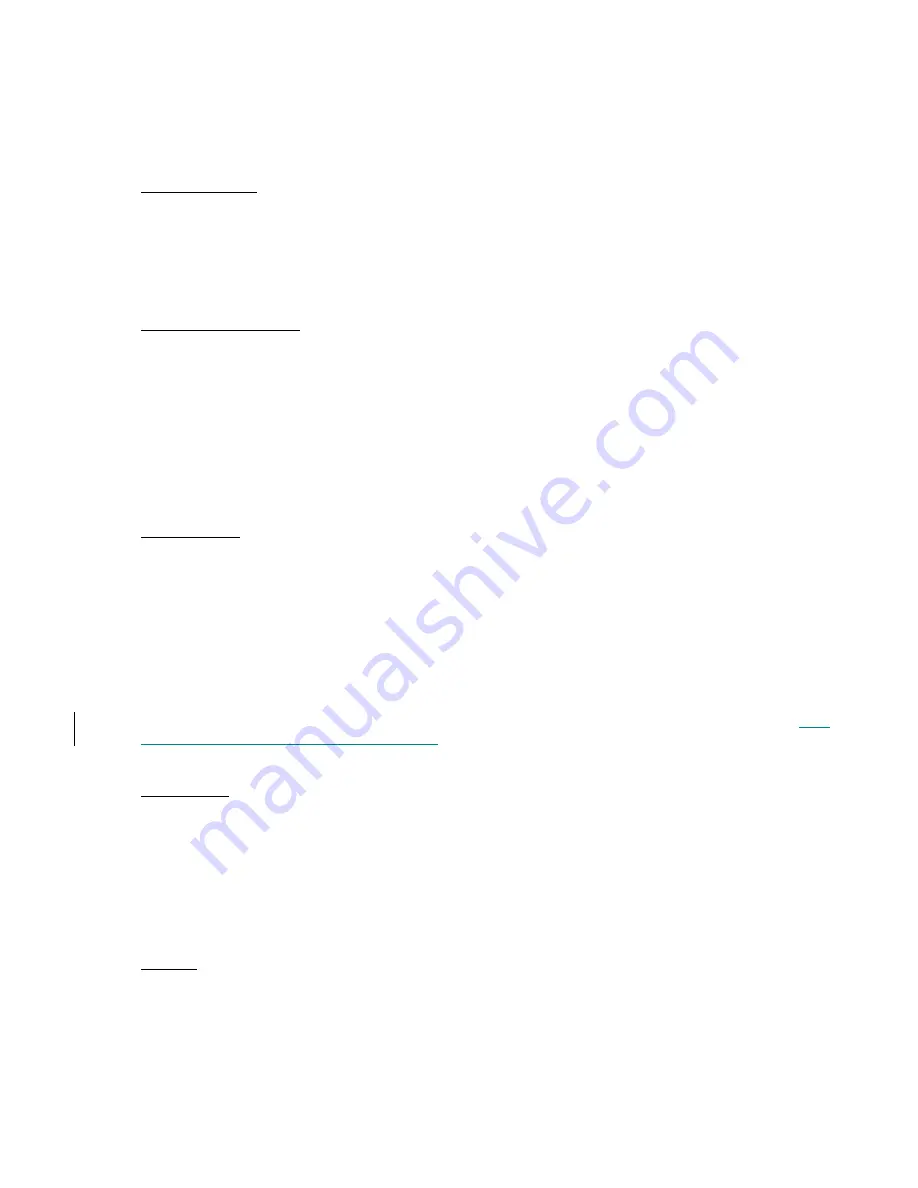
Document Q101, Revision W
(Printout Uncontrolled)
Page 5 of 23
Archiving of obsolete documents is controlled by each department and is audited by the Quality Auditor. In some
appropriate cases, obsoleted documents are identified and maintained in a history file. Factory service is an example of
a need to maintain historical information.
Control of Records
The Vice President of Quality is responsible for identifying the information necessary to measure the effectiveness of
the QMS. These records and their retention are identified in ADTRAN work instructions. This information is
collected, analyzed and acted upon to assure continuous improvement. The data is maintained so that retrieval and
review by management or customer representatives may be easily accomplished. All data associated with product
quality is kept in secure areas to avoid loss or damage. (GEN05.1)
5.0
MANAGEMENT RESPONSIBILITY
Management Commitment
ADTRAN’s QMS Steering Committee, comprised of top management, is committed to developing, implementing and
overseeing continuous improvement of the QMS. Corporate Quality documents committee-meeting minutes, which are
maintained on ADTRAN’s internal network.
The Steering Committee is responsible for communicating to the organization the importance of meeting customer as
well as legal and regulatory requirements, establishing and reviewing the quality policy, ensuring quality objectives are
established, conducting management reviews and ensuring the availability of resources. (GEN01.1)
Management exhibits its commitment to, and active involvement in, the administration of the QMS by providing
employees with periodic updates on the systems performance.
Customer Focus
Top management ensures that customer requirements are communicated and provided as agreed upon.
Sales/Marketing and Engineering have the primary responsibilities for determining and defining customer needs,
expectations, and product requirements.
ADTRAN’s management is committed to establishing and maintaining effective relationships with its customers and
continuously improving customer satisfaction.
Customer information is sought to secure an understanding of customer expectations and to track resolutions of issues
stemming from this communication.
Documented procedures have been established to define methods of communicating with select customers to
share
expectations, solicit, and consider customer input
, a method to share joint expectations with our customers, and to
periodically review the status of expectations and the resolution of issues. (GEN21.2)
Quality Policy
The Quality Policy Statement is defined by ADTRAN top management and re-examined at least once a year when this
document is reviewed and revised. Acceptance by the Executive staff is recorded as the signature of the Vice President
of Quality. See Attachment 1, Quality Policy Statement.
The Vice President of Quality ensures overall quality of ADTRAN products and services by communicating the
Quality Policy to all ADTRAN associates. Top management is authorized to ensure the Quality Policy is understood,
implemented, and maintained at all levels in the organization by setting direction, methodology, and quality goals,
which are aimed at total customer satisfaction and continuous improvement.
Planning
Top management establishes at relevant functions and levels of the organization, quality objectives that are measurable
and consistent with the quality policy. The objectives include targets for the TL9000 measurements and those that are
required to meet product requirements.
ADTRAN’s QMS Steering Committee develops a generic Quality Plan involving all the processes determined
necessary to ensure conformance of products and services. In addition, top management develops business plans for