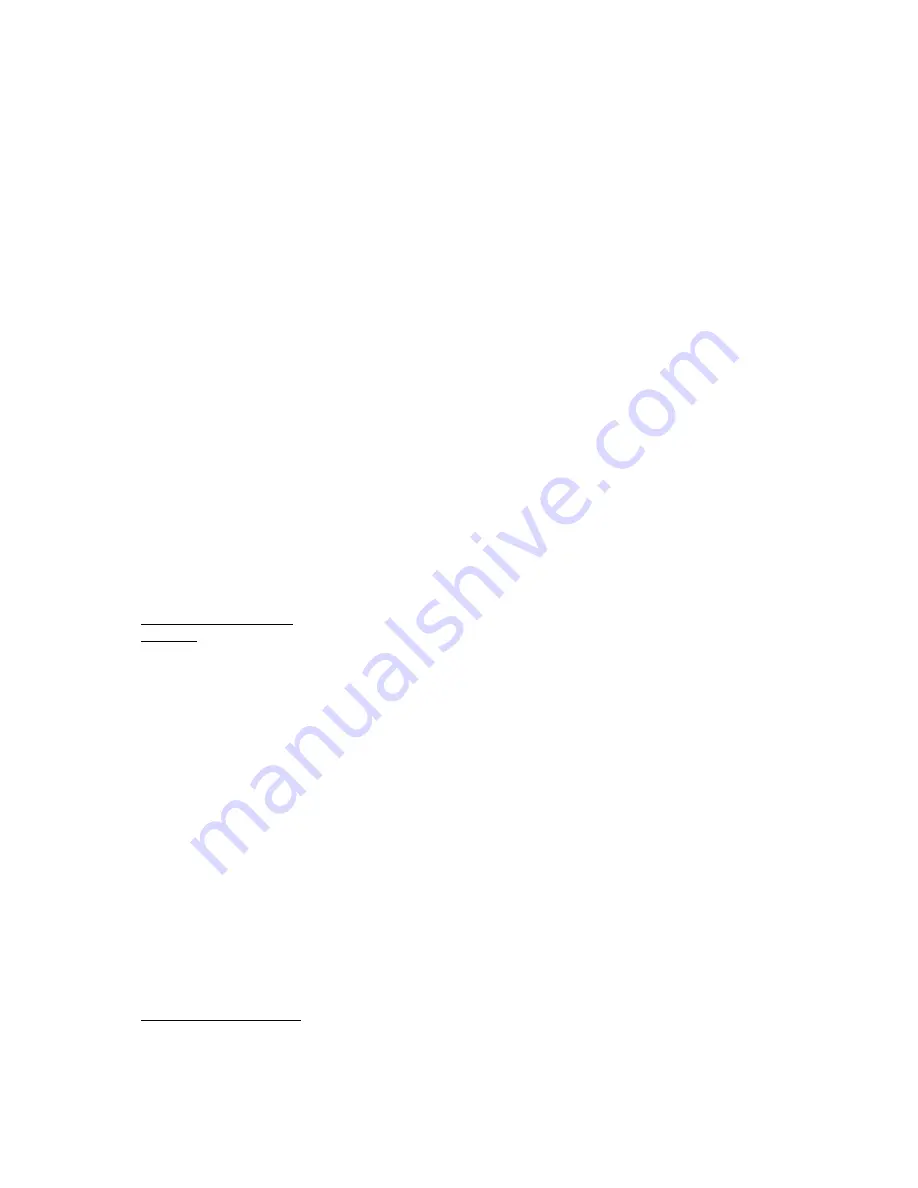
Document Q101, Revision W
(Printout Uncontrolled)
Page 8 of 23
contracts to assure the capability and desire to meet the requirements. Any exceptions are communicated through Sales
and Marketing, and negotiated to resolve or obtain the most favorable terms prior to contract execution; however, the
CEO or appropriate Division General Manager is authorized to finalize contract negotiations with unresolved
issues if
an impasse occurs that could jeopardize the pending business relationship. Records of each contract review are
maintained by the appropriate organization. A copy of the executed contract is distributed to the cognizant departments
for reference in performing the contract. (GEN03.1, SL15)
The Sales and Marketing department communicates with our customers on product information, contracts, order
handling, amendments, customer feedback, including customer complaints. Sales and Marketing maintains a
documented customer notification process to ensure that customers are notified of any product problems or changes
that may affect them. The ADTRAN/Customer Purchase Contract and/or the latest issued Telcordia technical
publication GR-209-CORE are used as a guide for determining whether a product change warrants a customer
notification. (SL02)
Product repairs are coordinated by the Customer and Product Service group (CaPS). The warranty period and any
special handling requirements are outlined in the repair warranty agreement or customer contract. (GEN02.3)
ADTRAN maintains a dedicated Technical Service function whose responsibilities include: providing answers to
technical and application questions, assisting in resolution of problems, and Marketing for product training. Product
training is available for ADTRAN personnel and customers.
Documented procedures have been developed and implemented defining processes for notifying the customer of
reported problems, resolution of customer reported problems and providing the customer with feedback. Documented
procedures are in place for assigning severity level to customer reported problems to ensure timely resolution.
(GEN14.1, SL12, TS19.5)
ADTRAN has a documented recall process to ensure the identification and recalling of products that are unfit to
remain in service. (SL12)
Design and Development
Planning
As an integral part of the QMS, Engineering assures all product designs and specifications are reviewed, tested,
verified and validated, when appropriate, prior to production. This is accomplished by guidance documents and control
documents. ( EN02, EN07, EN10, EN11, and PQ01)
Upon request, ADTRAN communicates, jointly agreed upon, design and development measurements with the
customer.
The organizational and technical interfaces between groups, in which design input is received, are defined in
procedures outlining design engineering responsibilities. The design input information is captured by the designated
responsible engineer and regularly reviewed during design review meetings. (GEN04.4 and GEN05.5)
The Engineering Manager plans projects, schedules and assigns activities. The Project Engineer interfaces with groups
to assure requirements are transmitted so that the project progresses on schedule. Typical interfaces are with: Sales and
Product Management for specification and customer requirements, Component Engineering for new part qualification,
Purchasing and Component Engineering for Supplier Qualification, Technical Publications for document preparation,
Material Control for planning material, Manufacturing Engineering for testability and manufacturability, Test
Engineering for Test Plans, and Technical Support Services for end of life planning. (GEN04.4)
Product schedules are maintained by the Engineering Planners and available on the ADTRAN internal network.
Engineering Planners revise product schedules as the design and development progresses. (GEN04.4)
Requirements Traceability
The responsible engineer ensures that the design meets all specifications and that all specifications are verified by
verification testing. (EN10)