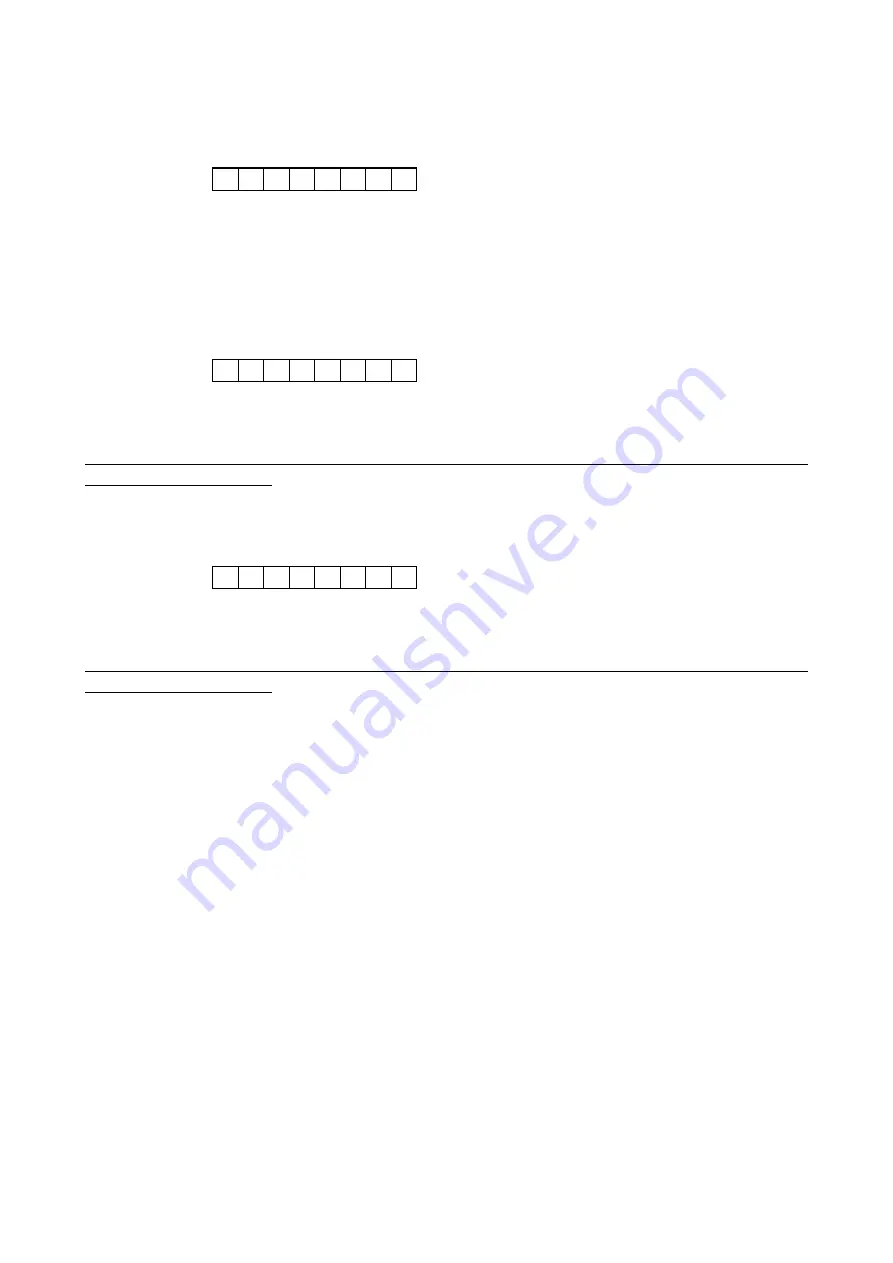
ADOS S.R.L. Buccinasco (MI)
417-MTA200I1
Rev. 9
Page 65 of 77
5.3.20 D/A converter function
D / A M o d
e
Parameter 38
It is possible to set the following values:
•
Gross (default
configuration)
•
Net
5.3.21 D/A Zero
D / A Z e r
o
Parameter 39
It is possible to set a value ranging from 0 (default configuration) to the full scale (given by the
product of graduation by resolution).
At this configuration step is possible to adjust the Zero analog output (see “analog output
management” paragraph).
5.3.22 D/A Full Scale
D / A S p a
n
Parameter 40
It is possible to set a value ranging from full scale (default configuration), given by the product of
graduation by resolution, to 0.
At this configuration step is possible to adjust the Full Scale analog output (see “analog output
management” paragraph).