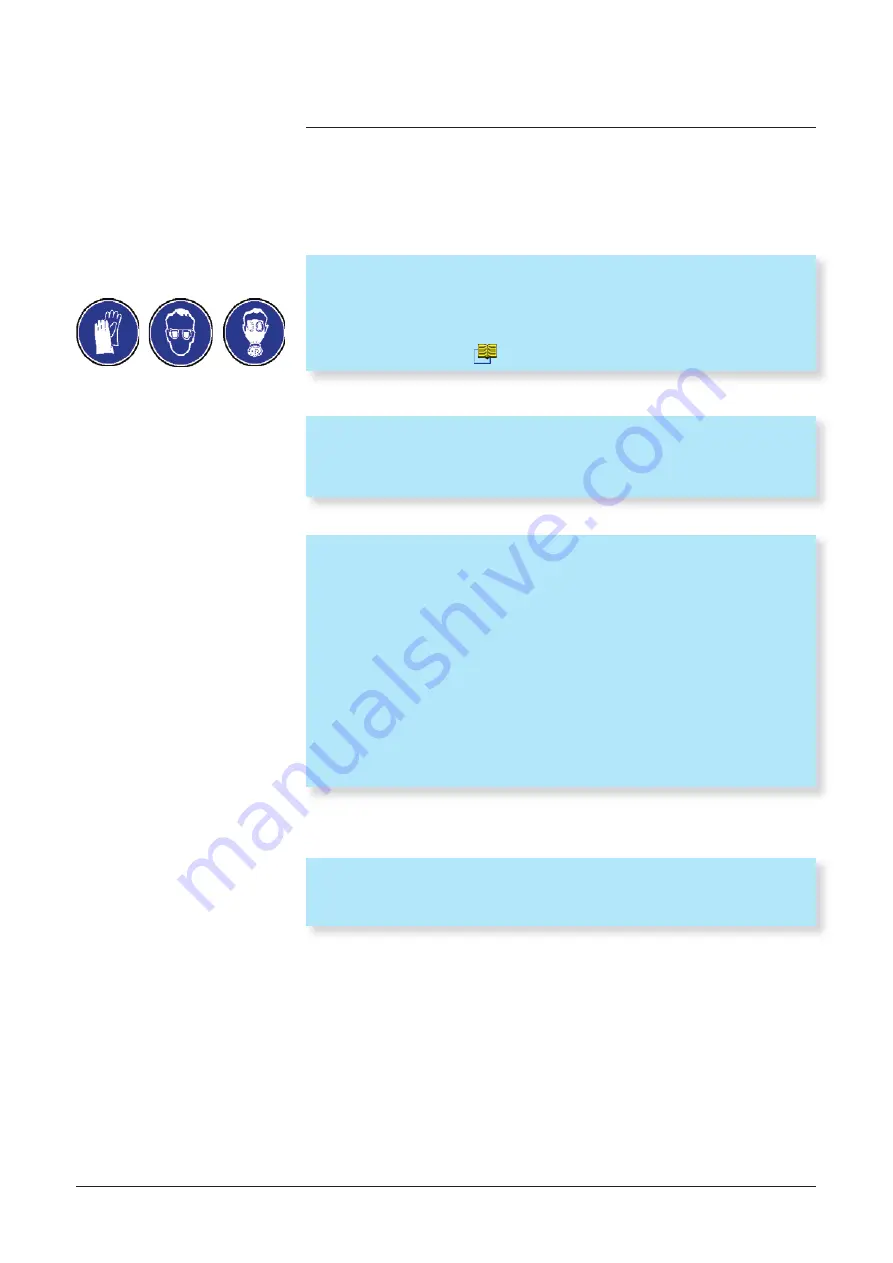
2/2
D 100
Safety instructions for product removal
GB 01739 - Edition 16 - Nov
. 12
Decontamination - product dismantling
According to the regulations 2002/96/CE about Waste of electrical and
electronical equipments, and 2011/65/CE about Restriction of Hazardous
substances, the manufacturer provides a recycling paid service for the end-
of-life of waste electrical and electronic equipment.
Any obligation of the manufacturer to take back such equipment shall apply
only to complete not amended or modified equipment, using adixen Vacuum
Products original spare parts, delivered by Pfeiffer Vacuum, containing i.e. all
its components and sub-assemblies.
This obligation will not cover the shipping cost to an adixen Vacuum Products
service center.
Whenever your return the product to an repair service center, please
make sur ou follow the Service procedure and ill in the declaration of
contamination found on our website.
How to contact us ?
The overhaul must be performed by manufacturer’s trained personnel.
Contact nearest service center or the service support at the following e-mail
address:
The outside of the product and control box can be cleaned with a lint free
wiper. Avoid using cleaning products that deteriorate printed surfaces and
self adhesive labels. All other cleaning operations must be done by our
service centers.
Wear gloves, protective glasses, any appropriated safety equipment.
Ventilate the premises well.
Do not eliminate maintenance waste via standard disposal channels. Have it
destroyed by a qualified company if necessary.
Install the inlet and exhaust blanking plates, thus delivered with the pump or
available as accessories (
E100) .
Users are advised:
adixen Vacuum Products - Operating Instructions - ATP 2300 M