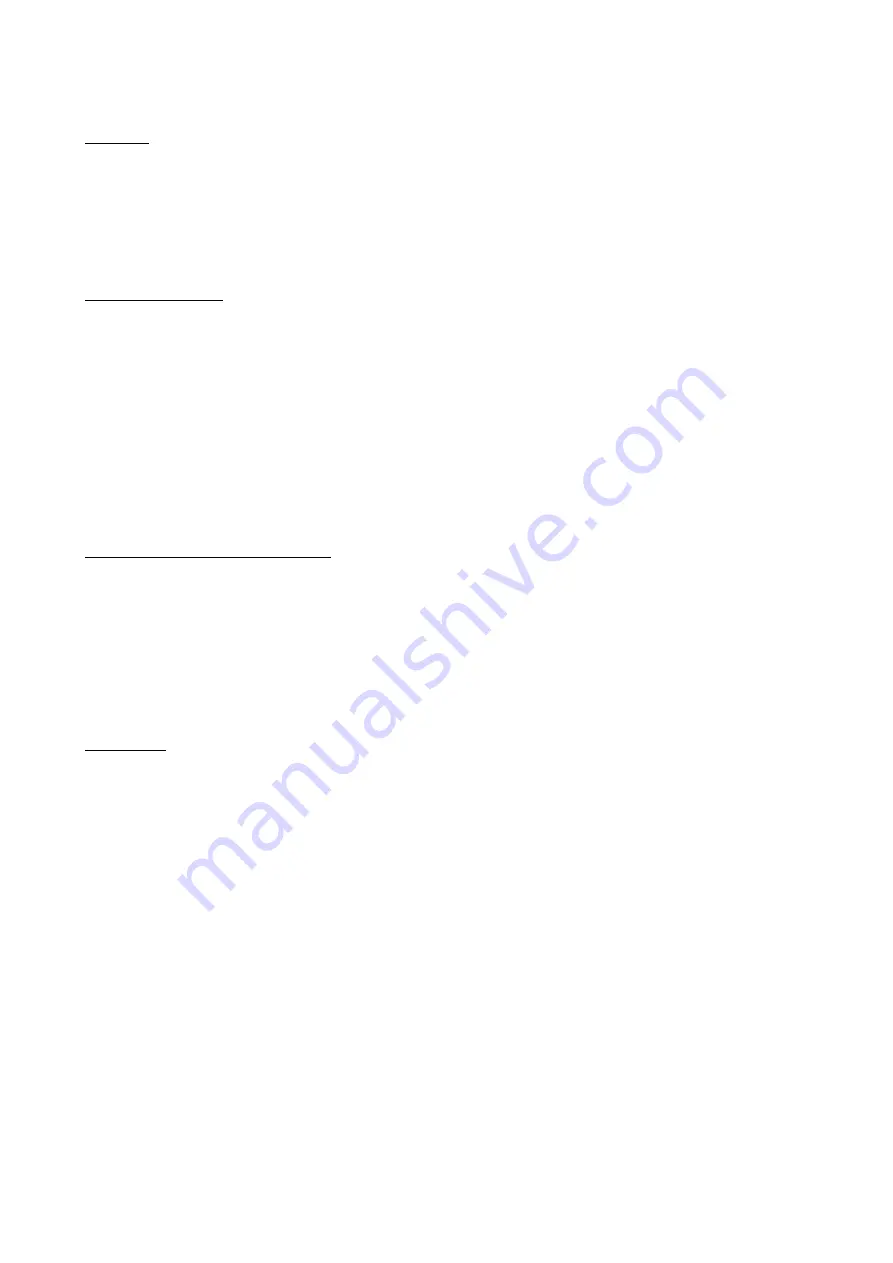
Copyright
The copyright for this manual belongs to ADDI-DATA GmbH.
These operating instructions consist of the OM, CM and PM parts and are only intended for use by the
operator and the operator’s staff. They include regulations and notes, which must not be
•
duplicated
•
published or
•
otherwise distributed, either in part or in full.
Non-compliance with this could lead to criminal proceedings.
Warranty and liability
Warranty and liability claims for personal injury and damage to property shall be excluded, if they are
attributable to one or more of the following causes:
•
Use of the board not in accordance with the regulations
•
Improper installation, commissioning, operation and maintenance of the board
•
Operation of the board in defective security installations or in improperly fitted or non-operational
security and protection appliances
•
Non-compliance with the notes in the operating instructions regarding transport, storage, installation,
commissioning, operation, thresholds, maintenance of the board, standard software
•
Arbitrary changes to the board
•
Arbitrary changes to the source code files
•
Insufficient monitoring of parts which are subject to wear
•
Catastrophes due to effects by foreign bodies or acts of God.
ADDI-DATA software product licence
Please read this licence carefully before using the standard software. The customer is only granted the right
to use this software if he/she agrees with the conditions of this licence.
•
The standard software must only be used to set up the ADDI-DATA boards
•
Reproduction of the software is forbidden (except for back-up and for exchange of faulty data
carriers)
•
Disassembly, decompilation, decryption and reverse engineering of the software are forbidden.
•
This licence and the software may be transferred to a third party if this party has acquired a board by
purchase, has agreed to all the conditions in this licence contract and the original owner does not
keep any copies of the software.
Trademarks
Borland C++ and Borland Delphi are registered trademarks of Borland Software Corporation.
MIPS is a registered trademark of Mips Technologies, Inc.
RM5231 is a registered trademark of PMC Sierra, Inc.
Microsoft, MS-DOS, Visual Basic, Visual C and Windows are registered trademarks of Microsoft Corporation.
Summary of Contents for APCI-8001
Page 4: ......
Page 47: ...CM COMMISSIONING MANUAL 47 5 4 APCI 8001 component mounting diagram ...
Page 48: ...48 CM COMMISSIONING MANUAL 5 5 APCI 8001 component mounting diagram bottom side ...
Page 49: ...CM COMMISSIONING MANUAL 49 5 6 APCI 8008 component mounting diagram ...
Page 50: ...50 CM COMMISSIONING MANUAL 5 7 APCI 8008 component mounting diagram bottom side ...
Page 51: ...CM COMMISSIONING MANUAL 51 5 8 APCI 8008 STP EVAI component mounting diagram ...
Page 52: ...52 CM COMMISSIONING MANUAL 5 9 APCI 8008 STP EVAI component mounting diagram bottom side ...