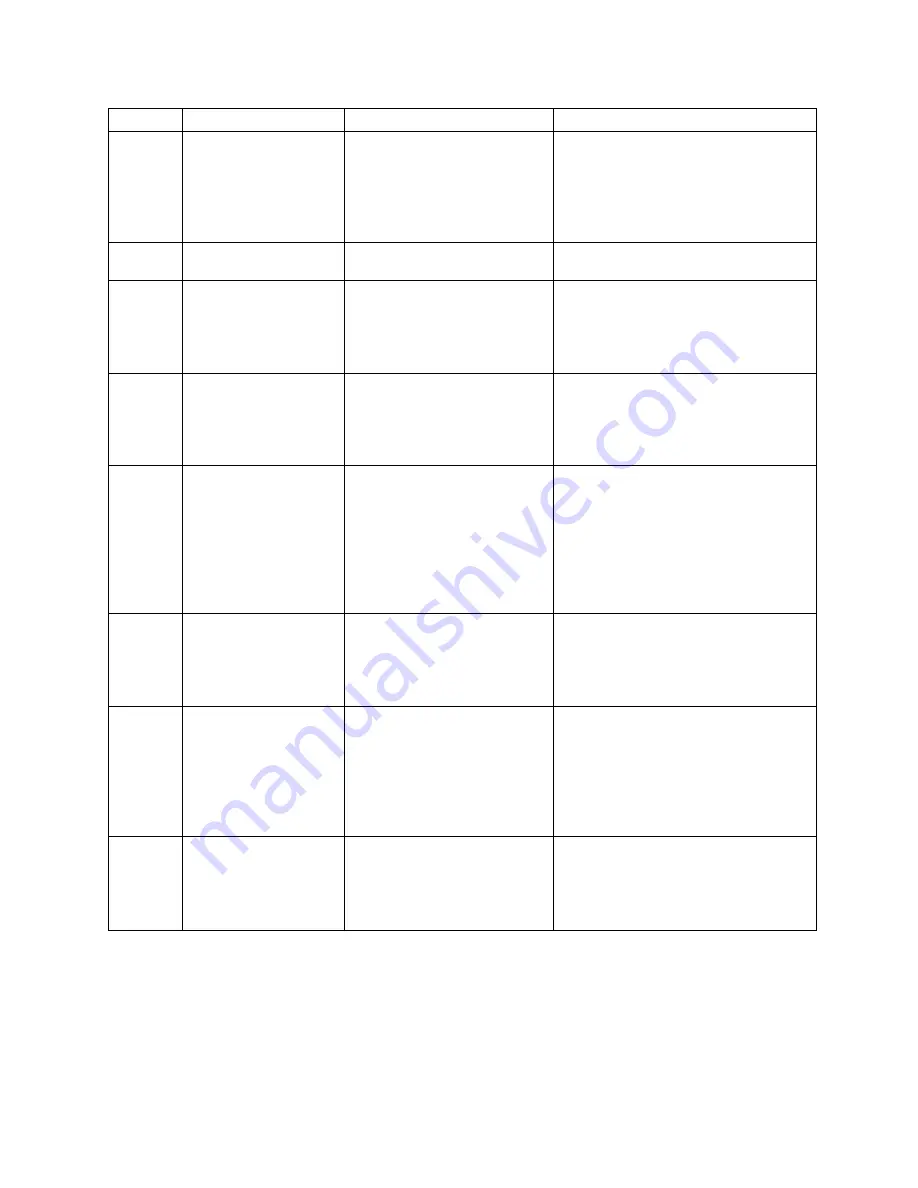
Page
92
of
125
•
Faulty drive
FD14
Drive Fault HW
Drive reporting fault via
IO signal
•
Tool not connected
•
Faulty tool cable
•
Faulty tool motor
•
Application exceeds
capability of drive
•
Faulty drive
FD15
Drive Vbus high
Drives DC bus voltage
exceeds electrical limits
•
AC supply power exceeds
voltage ratings of Controller
FD16
Drive Vbus low
Dives DC bus voltage is
too low to run tool
•
Supply power cycled too
quickly. Five second delay
required after switching off
the Controller before turning
back on.
FS26
Power on throttle
Run command on power
up
•
Tool laying on lever on power
up
•
Tool buttons out of calibration
•
Run command from logic IO
on power up.
FS27
Locked rotor
Motor has stalled for more
than 100 millisaeonds
•
Poor parameter settings for
application.
•
Torque signal out of
calibration
•
Faulty tool gearing or motor
•
Corrupted TID parameters
•
Faulty Controller or tool
electronics
FS28
Target out of range
of tool
Parameter set torque
target out of range of
rated tool capability
•
Target torque exceeds tool
capability
•
Joint Compensation Ratio set
too low.
•
Corrupted TID parameters
FS29
Invalid tool
Tool configuration not
compatible with
parameter set
•
Tube nut tool commanded to
run a parameter set with left
hand thread direction or with
an unfastening stage
•
Tube nut tool commanded to
go in the disassembly
direction
FS31
Lost Master Start
Signal
Lost Connection to Master
Spindle
•
Faulty Ethernet Connection
•
RTOS processor firmware
corrupted or not loaded
•
Faulty SOM board or
connector