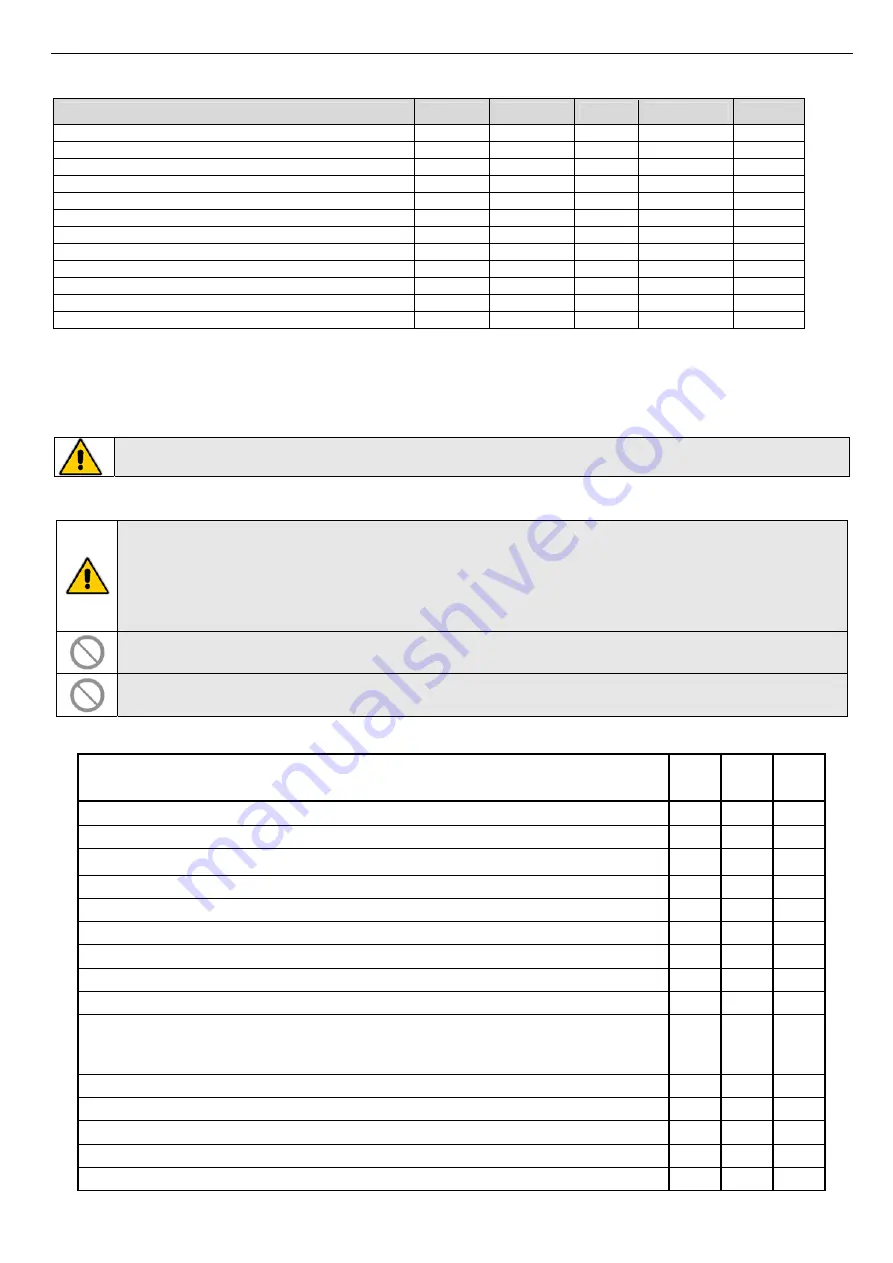
20
9.6
ALARMS
LIST
Error
description
Code
Compressor
Pump
Resistances
Fan
Inverter
hardware
malfunctioning
E75
OFF
OFF
Compressor’s
tension
too
high
E76
OFF
OFF
Power
supply
tension
out
of
bounds
E78
OFF
OFF
Compressor
not
power
supplied
E79
OFF
OFF
Inverter
time
out
malfunctioning
E80
OFF
OFF
Compressor
inlet
sensor
E63
OFF
OFF
OFF
OFF
Compressor
outlet
sensor
E64
OFF
OFF
OFF
OFF
High
pressure
transductor
E65
OFF
OFF
OFF
OFF
Low
pressure
transductor
E66
OFF
OFF
OFF
OFF
Outdoor
air
sensor
for
climate
adjust
E67
OFF
OFF
OFF
OFF
High
pressure
E01
OFF
OFF
Low
pressure
E02
OFF
OFF
10
SHUTDOWNS
FOR
LONG
PERIODS
•
Turn
off
all
the
indoor
terminal
units
of
the
users.
•
Close
the
water
faucet.
•
Turn
off
the
switch
QF
general
differential
to
OFF.
If
the
temperature
drops
below
freezing
point
(0°C)
there
is
serious
danger
of
frost:
providing
a
mixture
of
water
and
glycol
in
the
system,
otherwise
drain
the
water
system
and
the
hydraulic
circuits
of
the
heat
pump.
11
MAINTENANCE
AND
PERIODIC
CHECKS
WARNING:
All
the
operations
described
in
this
chapter
HAVE
TO
BE
CARRIED
OUT
BY
TRAINED
STAFF
ONLY.
Before
any
operation
or
before
entering
the
inner
components
of
the
unit,
be
sure
that
the
power
supply
is
disconnected.
The
compressor’s
heads
and
discharge
piping
are
usually
at
high
temperature
levels.
Be
very
careful
when
operating
in
their
surroundings.
Aluminium
coil
fins
are
very
sharp
and
can
cause
serious
wounds.
Be
very
careful
when
operating
in
their
surroundings.
After
servicing
operations,
re
‐
install
the
cover
panels,
and
fix
them
by
means
of
screws.
The
refrigerant
circuits
must
not
be
filled
with
refrigerant
gas
other
than
that
indicated
on
the
nameplate.
The
use
of
a
different
refrigerant
can
cause
severe
damage
to
the
compressor.
It
is
forbidden
to
use
refrigerant
oils
other
than
those
specified
in
this
manual.
The
use
of
different
oil
can
cause
serious
damage
to
the
compressor.
It
is
a
good
rule
to
carry
out
periodic
checks
in
order
to
verify
the
proper
operation
of
the
unit.
OPERATION
1
month
4
month
6
month
Filling
the
water
circuit.
x
Presence
of
bubbles
in
the
water
circuit.
x
Check
out
that
safety
and
control
devices
work
correctly
(indoor
and
outdoor
units)
x
Check
out
possible
oil
leakage
from
compressor
(outdoor
unit).
x
Check
out
possible
water
leakages
from
the
hydraulic
circuit
(outdoor
unit).
x
Check
out
the
proper
working
of
the
flow
switches
(outdoor
unit).
x
Check
out
that
the
crankcase
resistances
are
properly
supplied
and
functioning
(outdoor
unit).
x
Clean
the
metallic
filters
of
the
hydraulic
circuit.
x
Clean
the
finned
coil
by
means
of
compressed
air
or
water
jet
(outdoor
unit).
x
Check
out
that
all
the
terminals
on
the
electric
board
as
well
as
on
the
terminals
of
the
compressor
are
properly
fixed.
Clean
from
time
to
time
the
remote
control
switch’s
sliding
and
fixed
contacts
(indoor
and
outdoor
units).
x
Tightening
of
water
connections.
x
Check
out
the
tightening
and
the
balancing
of
the
fan
blades
(outdoor
unit).
x
Correct
voltage.
x
Correct
absorption.
x
Check
the
refrigerant
charge.
x
Summary of Contents for PACK DUE 12
Page 1: ......
Page 39: ...38 22 2 OUTDOOR UNITS 22 2 1 Wiring diagram of PACK DUE 9...
Page 40: ...39 22 2 2 Wiring diagram of PACK DUE 12...
Page 41: ...40 22 2 3 Wiring diagram of PACK DUE 16...
Page 44: ......
Page 45: ......
Page 46: ......
Page 47: ......