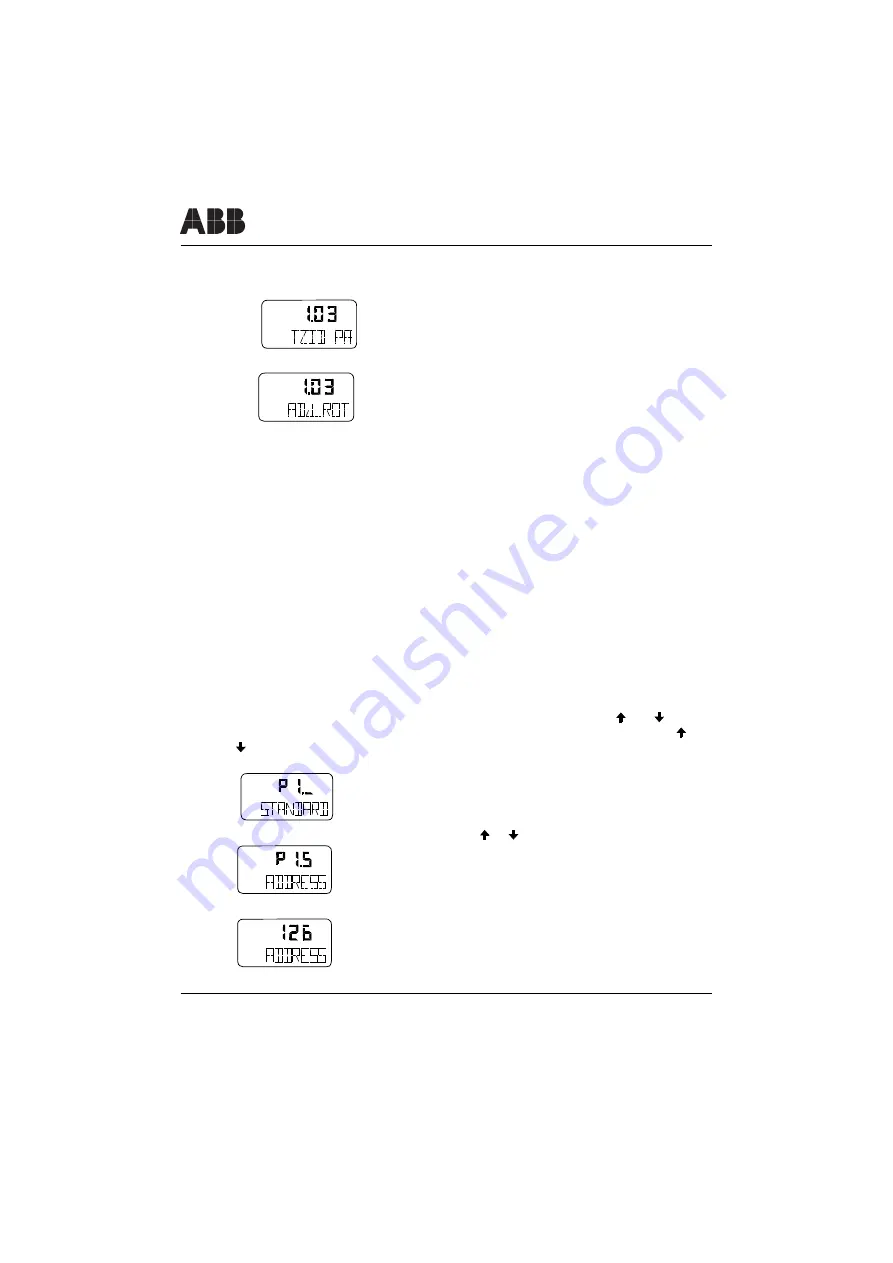
Installing and commissioning
20
Installing and commissioning
41/18-77 EN
b) For rotary actuators
-
Press and hold
ENTER
.
-
is
displayed.
-
Wait until the display has changed to
-
Release
ENTER
.
-
Press and hold
ENTER
again
until the countdown has run down from 3 to 0.
-
Release
ENTER
.
Autoadjust is started automatically, and the progress is displayed as in P1.1.
When Autoadjust has completed successfully, the determined parameters are saved
automatically, and the remote level is activated again.
If any errors should occur during Autoadjust, the respective error code is displayed as in
P1.1. In this case press
ENTER
to acknowledge. The operating level, mode 1.3
(MAN-SENS) will be activated automatically, then.
3.4.2 Setting the bus address
•
When the positioner is on the remote level, first change over to the operating level by
pressing and holding
MODE
and
ENTER
simultaneously until the countdown has
run down from 3 to 0. Release
MODE
and
ENTER
.
The positioner changes over
to the operating level.
•
Switch the positioner over to the configuration level: Press and hold and simulta-
neously and then additionally briefly press and release
ENTER
once. Keep and
pressed until the countdown from 3 to 0 is finished (approx. 3 seconds) and only
then release them. Otherwise, the change-over to the configuration level will fail.
is
displayed
•
Press and hold
MODE
. Additionally press or until
is displayed
•
Release
M
ODE
.
is displayed (factory setting)
conf
mA
%
C
°
conf
mA
%
C
°
conf
mA
%
C
°
conf
mA
%
C
°
conf
mA
%
C
°
Summary of Contents for TZIDC-110
Page 1: ...TZID C110 Intelligent positioner for PROFIBUS PA Short manual 41 18 77 EN Rev 01...
Page 33: ...Certificates 41 18 77 EN Certificates 29 5 Certificates...
Page 34: ...Certificates 30 Certificates 41 18 77 EN...
Page 35: ...41 18 77 EN 31...
Page 36: ...Certificates 32 Certificates 41 18 77 EN...
Page 37: ...41 18 77 EN 33...
Page 38: ...Certificates 34 Certificates 41 18 77 EN...
Page 39: ...41 18 77 EN 35...
Page 43: ......