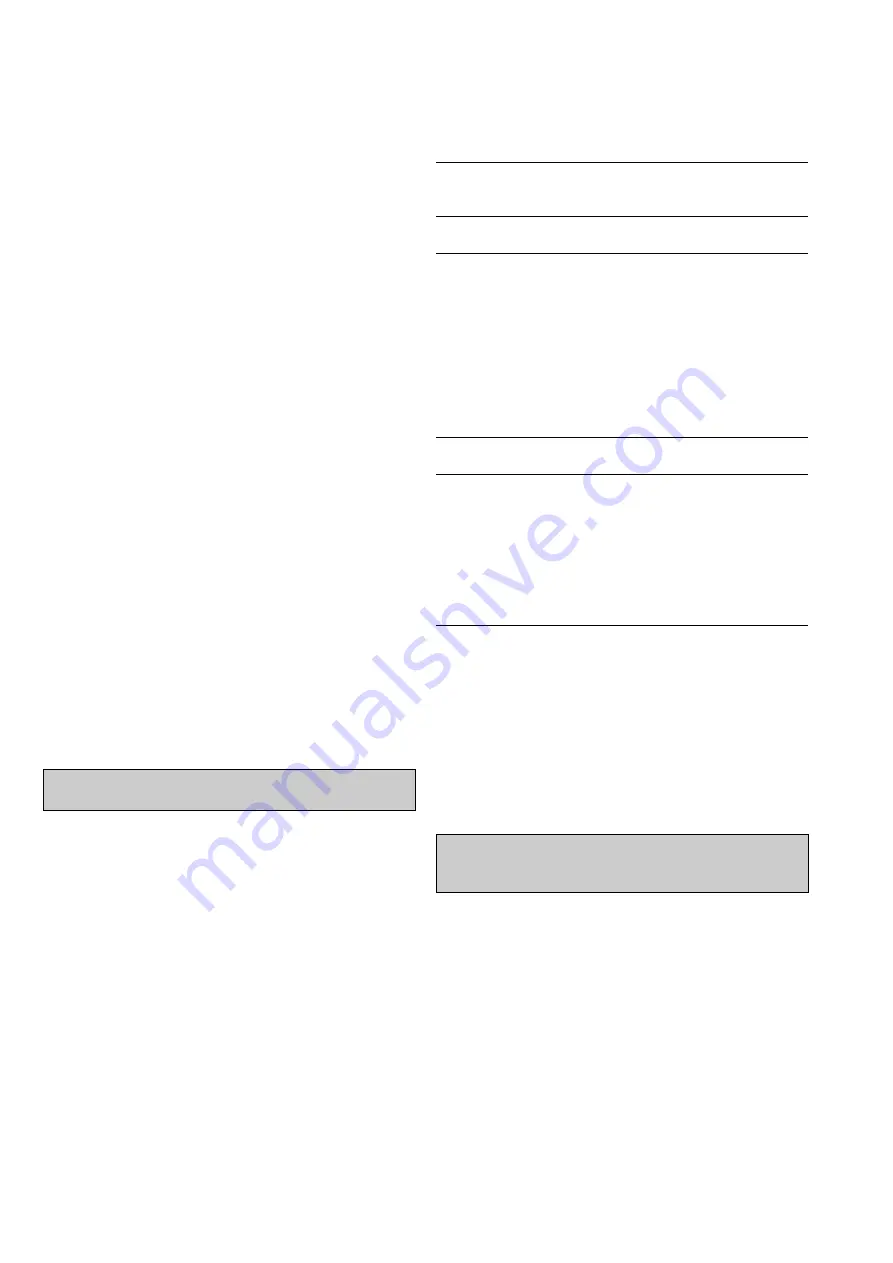
6
LV Motors/Machine Instructions 10-2000
Maintenance and lubrication
General inspection
-
Inspect the machine at regular intervals.
-
Keep the machine clean and ensure free
ventilation airflow.
-
Check the condition of shaft seals (eg V-ring) and
replace if necessary.
-
Check the condition of connections and mounting
and assembly bolts.
-
Check the bearing condition by listening for
unusual noise, vibration measurement, bearing
temperature, inspection of spent grease or SPM
bearing monitoring.
* When changes of condition occur,
dismantle the machine, check the parts
and replace if necessary.
Lubrication
Machines with permanently greased bearings
Machines up to frame size 180 are normally fitted with
permanently greased bearings of either Z or 2Z types.
Bearing types are specified in the respective product
catalogues and on the rating plate of each motor from
size 112 and larger.
As a guide, adequate lubrication can be achieved for the
following duration, according to L1 at ambient
temperature of 25° C.
32 000 - 45 000 duty hours for 4 pole machines.
1)
16 000 - 26 000 duty hours for 2 and 2/4 pole
machines.
1)
The shorter times apply to larger frame sizes.
1)
Depending on application and load conditions, see
applicable product catalogue.
Hours of operation for vertical motors are half of the
above values.
Machines with relubrication system
WARNING
Beware of all rotating parts!
Relubrication procedure:
- Remove grease outlet plug if fitted.
- Press fresh grease into the bearing until all old grease
has been forced out
- Let the motor run 1-2 hours to ensure that all excess
grease is forced out of the bearing. Close the grease
outlet plug if fitted.
Regrease motors while running. If this is not possible,
lubrication can be carried out while the machine is at a
standstill. In this case, use only half the quantity of
grease, then run the motor for a few minutes at full
speed. When the motor has stopped, the remaining
quantity of grease can be forced in until the old grease
has been replaced.
After 1-2 running hours close the grease outlet plug (if
fitted).
The grease outlet plug must be removed permanently
with automatic lubrication.
If the machine is fitted with a lubrication information
plate, follow the given values, otherwise use the values
in table below.
ABB Motors policy is to have reliability as a vital issue
in bearing lubrication intervals. That is why we follow the
L1-principle (meaning that 99 % of the motors are sure
to make the interval time). According to L1 policy the
lubrication intervals are as follows:
Frame
Amount 3600
3000
1800
1500
1000
500-900
size
of grease r/min
r/min
r/min
r/min
r/min
r/min
g/bearing
Ball bearings
Lubrication intervals in duty hours
112 10
10000 13000 18000 21000
25000
28000
132 15
9000 11000 17000 19000
23000
26500
160 25
7000
9500 14000 17000 21000
24000
180 30
6000
8000 13500 16000
20000
23000
200 40
4000
6000
11000 13000
17000
21000
225 50
3000
5000 10000 12500
16500
20000
250 60
2500
4000
9000
11500 15000
18000
280 70
2000
3500
8000 10500
14000
17000
315 90
2000
3500
6500
8500 12500
16000
355 120
1200
2000
4200
6000
10000
13000
400 120
1200
2000
4200
6000
10000
13000
Roller bearings
Lubrication intervals in duty hours
160 25 3500 4500
7000
8500
10500
12000
180 30 3000 4000
7000 8000
10000 11500
200 40 2000 3000
5500
6500
8500
10500
225 50 1500 2500 5000
6000 8000
10000
250 60 1300 2000
4500 5700
7500
9000
280 70 1000 1700 4000 5300
7000
8500
315 90 1000 1700 3300
4300
6000
8000
355 120 400 1000 2000 3000
5000
6500
400 120 400 1000 2000 3000
5000
6500
Lubrication intervals for vertical machines are half of the
above values.
The amount of grease stated in the table should be
doubled if an automatic regreasing system is used.
The table values are based on the motor running at rated
output in an ambient temperature of about + 25° (approx.
80°C bearing temperature). The values should be halved
for 15°C increase in bearing temperature and may be
doubled for 15°C decrease in ambient temperature.
WARNING
The maximum operating temperature of the
grease and bearings must not be exceeded.
Higher speed operation, eg in frequency converter
applications, or lower speed with heavy load will require
shorter lubrication intervals. Consult ABB Sales Office in
such cases.
Typically a doubling of speed will require a reduction of
lubrication intervals to approx. 40 % of values tabulated
above.
Suitability of bearings for high speed operation must be
checked.