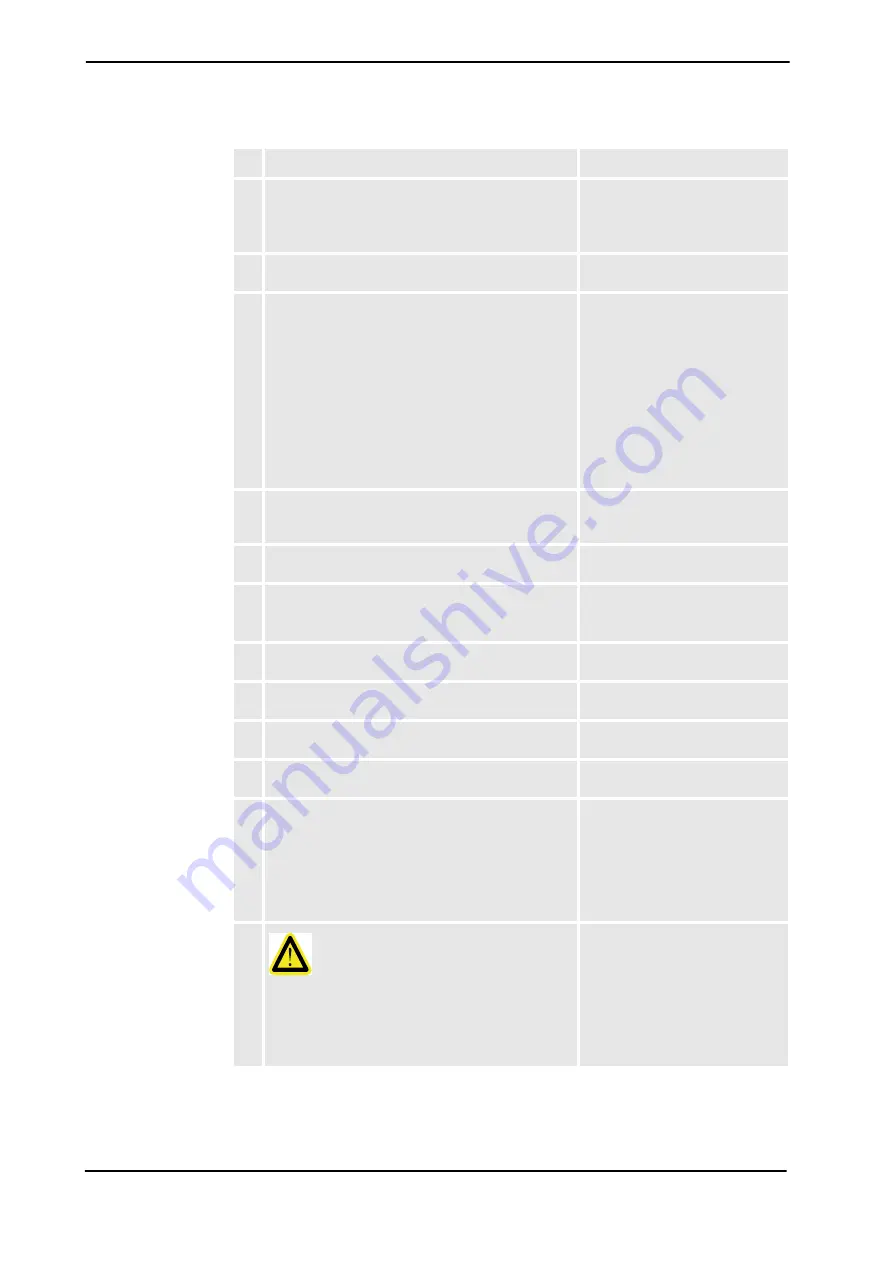
4 Repair
4.7.5. Replacement of gearbox, axis 5
3HAC022033-001 Revision: E
364
©
Co
py
rig
h
t 200
4 - 20
08 ABB.
All r
ig
h
ts r
e
se
rv
ed
.
7. Secure the gearbox with 16 of the 18
attachment
screws
and washers.
18 pcs: M10 x 40: tightening
torque: 65 Nm.
Shown in the figure
8. Remove the guide pins and fit the remaining two
attachment screws as specified in the previous step.
9. Refit the
gear Z3
to the
gearbox, axis 5
with its
attachment screws.
9 pcs: M12 x 50; 12.9 quality
UNBRAKO, tightening torque: 115
Nm.
6 pcs: M16 x 60: tightening
torque: 300 Nm.
Shown in the figure
Reused screws may be used,
providing they are lubricated as
detailed in section
before fitting.
10. Refit the wheel unit.
Detailed in the following
procedures (
).
11. Replace the
gasket
.
Art. no. is specified in
.
12. Refit the
cover, axis 5 gearbox
with its
attachment
screws
and secure with locking liquid.
14 pcs, tightening torque: 10 Nm.
Shown in the figure
13. Refit the motor, axis 5.
Detailed in section
14. Perform a leak-down test.
Detailed in section
.
15. Refill the primary gearbox with oil.
Detailed further in section
oil, gearbox axis 5 on page 196
16. Refill the secondary gearbox with oil.
Detailed further in section
oil, gearbox axis 5 on page 196
17. Recalibrate the robot.
Calibration is detailed in a
separate calibration manual,
enclosed with the calibration
tools.
General calibration information is
included in section
18.
DANGER!
Make sure all safety requirements are met when
performing the first test run. These are further
detailed in section
cause injury or damage! on page 36
Action
Note
Continued
Continues on next page