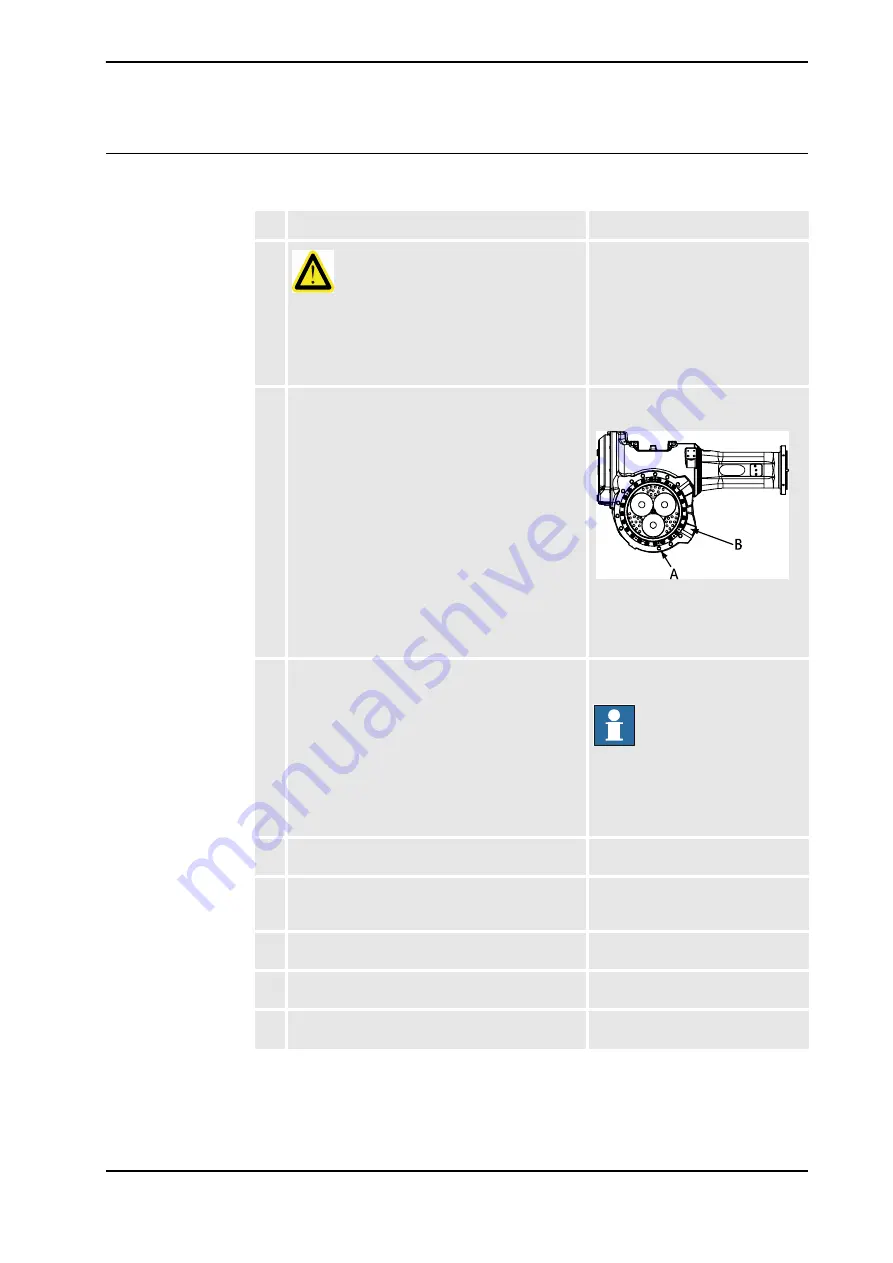
4 Repair
4.7.3. Replacement of gearbox, axis 3
351
3HAC022033-001 Revision: E
©
Co
py
rig
h
t 200
4 - 20
08 ABB.
All r
ig
h
ts r
e
se
rv
ed
.
Removal, gearbox axis 3
The procedure below details how to remove gearbox, axis 3.
Action
Note
1.
DANGER!
Turn off all electric power, hydraulic and
pneumatic pressure supplies to the robot!
For Foundry Prime robots: Do not turn off the air
pressure to motors and SMB.
2. Secure the upper arm in a horizontal position
using a
mechanical stop.
Fit the mechanical stop to the
third and final
attachment hole
, below the
fixed mechanical stop
in the upper arm, shown in the figure to the right.
Tightening torqure: 115 Nm.
Art. no. is specified in
.
xx0300000051
•
A: Third and final attachment
hole
•
B: Fixed mechanical stop
3. Remove the
motor, axis 3
.
Detailed in section
NOTE!
When removing the motor axis 3,
the brake on axis 3 is released.
Make sure the upper arm is secured
and disabled to move!
4. Remove the
upper arm
.
Detailed in section
5. Remove the
sealing, axis 2/3
between the
gearbox and lower arm.
On reassembly a new sealing must
be used! Art. no. is specified in
Required equipment on page 349
6. Place the upper arm safely on a workbench, in a
fixture or similar.
7. Remove the
attachment screws, gearbox.
Shown in the figure
.
8. Fit the two
guide pins
in 180° relation to each
other in the gearbox attachment screw holes.
Art. no. is specified in
.
Continued
Continues on next page