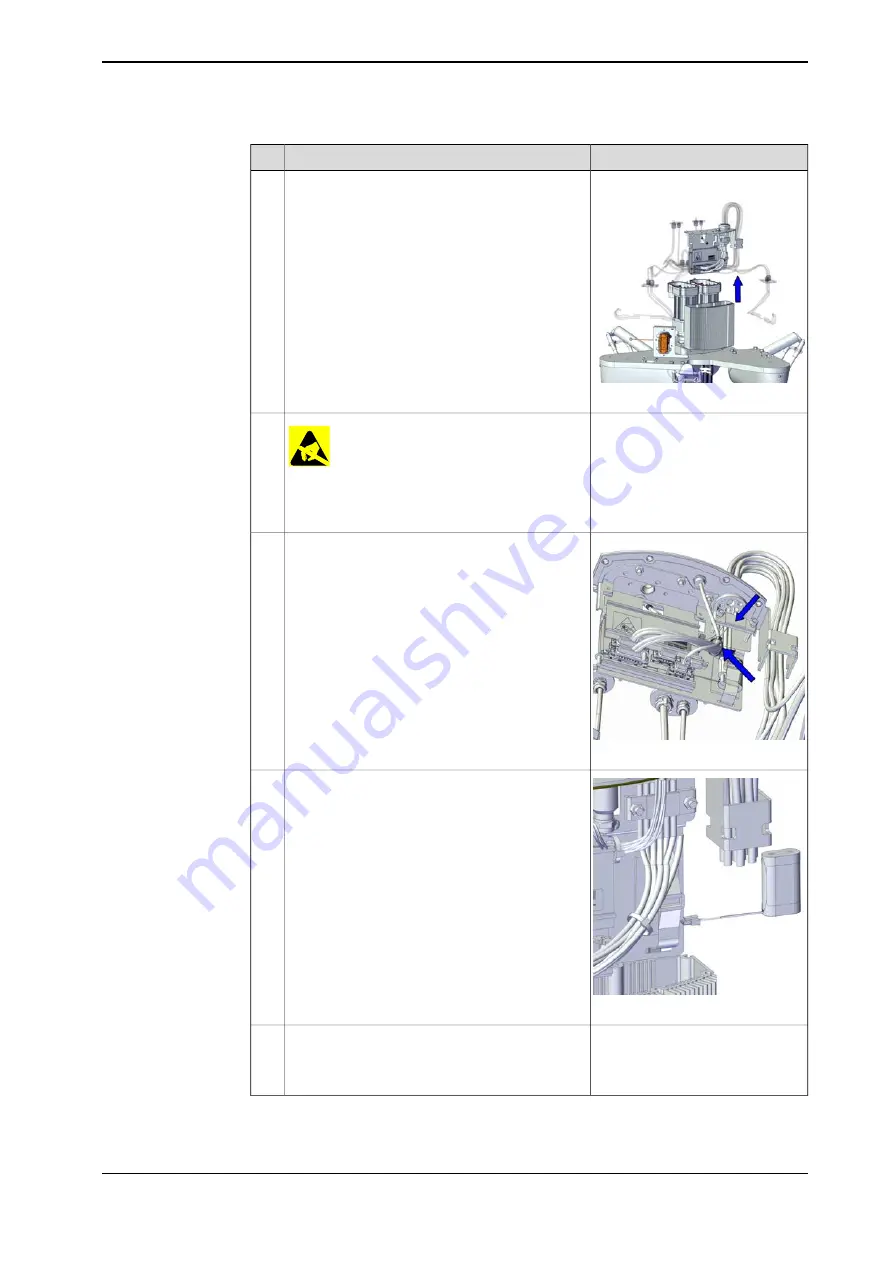
Note
Action
xx2100002739
ELECTROSTATIC DISCHARGE (ESD)
When handling the computer outside of the con-
troller, use the wrist strap button located on the
side of the computer.
10
xx2100001977
Cut cable straps
Remove the screen grounding plate
11
xx2100000957
Carefully pull out the battery and disconnect the
battery cable.
•
Battery cable connector R2.G.
12
Remove the SMB battery
.
Battery includes protection circuits. Only replace
with a specified spare part or with an ABB-ap-
proved equivalent.
13
Continues on next page
Product manual - IRB 365
103
3HAC079185-001 Revision: A
© Copyright 2022 ABB. All rights reserved.
5 Repair
5.3.1 Replacing the manipulator harness
Continued
Summary of Contents for IRB 365
Page 1: ...ROBOTICS Product manual IRB 365 ...
Page 8: ...This page is intentionally left blank ...
Page 14: ...This page is intentionally left blank ...
Page 198: ...This page is intentionally left blank ...
Page 216: ...This page is intentionally left blank ...
Page 232: ...This page is intentionally left blank ...
Page 234: ...This page is intentionally left blank ...
Page 238: ......
Page 239: ......