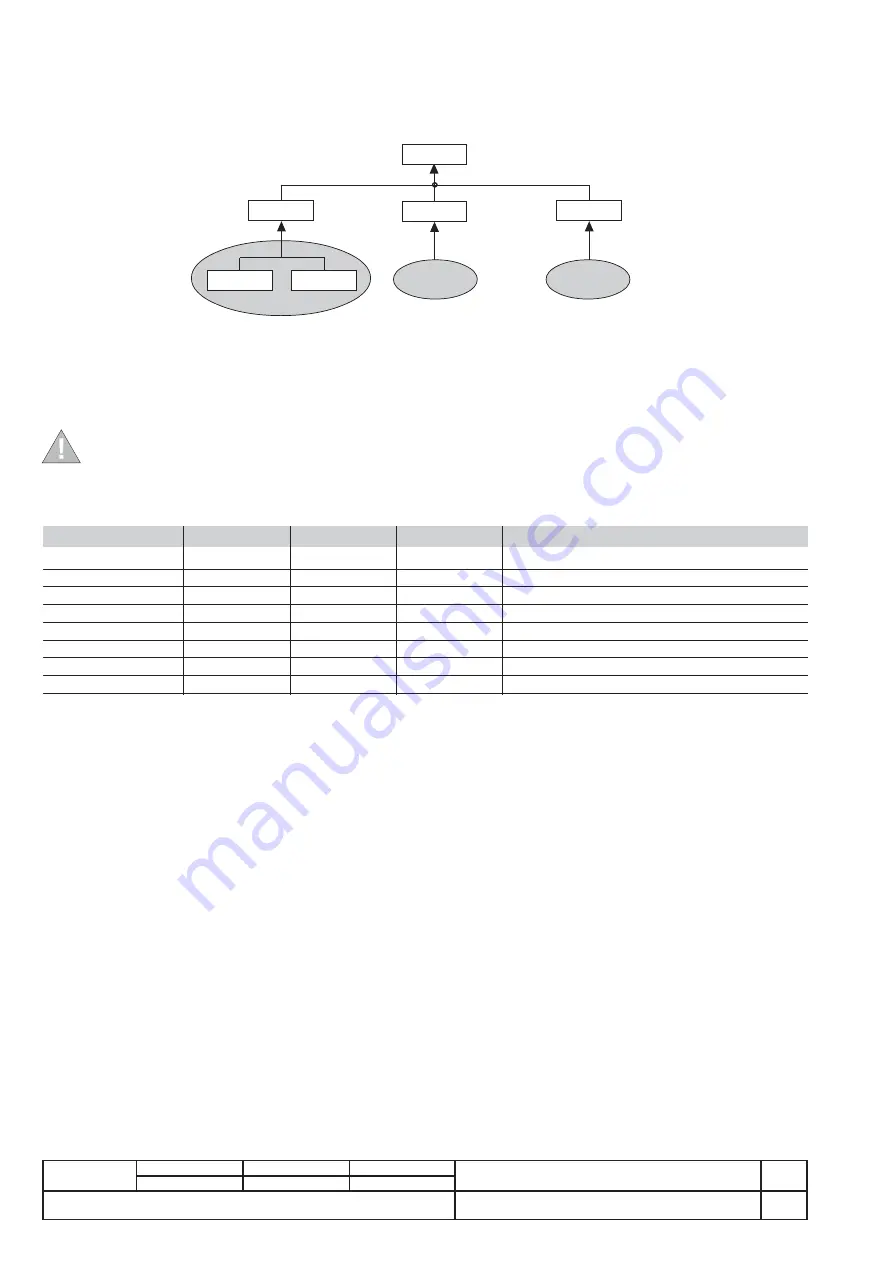
L3447
Emax DC
52/108
L3728
Model
Scale
Page No.
Doc. No.
Apparatus
1SDH000635R0002
13.2.9.2.3 Zone selectivity “S”
The zone selectivity function, guaranteed only if an auxiliary voltage is provided, enables the area of the fault to be isolated, only isolating the part
of plant nearest to the fault, while keeping the rest of the plant operational.
This is done by connecting all the zone selectivity outputs of the releases belonging to the same zone to one another (ZSO=K51/SZout) and taking
this signal to the zone selectivity input (ZSI=K51/SZin) of the next release on the supply side. If the wiring has been done correctly, all the zone
selectivity inputs of the last circuit-breakers in the chain and all the outputs of the circuit-breakers at the head of each chain must be empty.
13.2.9.3
Double S
Thanks to the new PR123/DC release that enables two independent and simultaneously active protection S thresholds to be specified, selectivity
can assured even in critical conditions.
This function enables a better selectivity level to be obtained than using a release without a "double S". This function is valid for t=K only.
As a practical example, the figure above shows a fault on the load side of the "Relay 1a" isolated by the latter without the "Relay 1" or the "Relay
0" being affected; a fault immediately downstream from the "Relay 1" will be isolated by the latter without the "Relay 0" being affected, thus ensuring
that the Areas 2...n remain operational.
The ZSO output can be connected to a maximum of 20 ZSI relays on the supply side in the selectivity chain.
The maximum length of cable for zone selectivity, between two units, is 300 meters.
Use corded shielded two-wire cable (see note A to par. 11.2.2).
The shield must only be earthed on the circuit-breaker of the supply-side relay (ZSI side).
The operation is only guaranteed when there is an auxiliary voltage.
The following logical table is implemented to manage the Zone Selectivity Input (ZSI) and Zone Selectivity Output (ZSO) signals:
Zone selectivity
Imax > I
2
ZSI signal
ZSO signal
Trip T
Excluded
NO
0
0
No trip
Excluded
NO
1
0
No trip
Excluded
YES
0
0
t
2
programmed
Excluded
YES
1
0
t
2
programmed
Inserted
NO
0
0
No trip
Inserted
NO
1
1
No trip
Inserted
YES
0
1
t
selectivity
Inserted
YES
1
1
t
2
programmed
The time t
2
must be set at a value corresponding to at least t
selectivity
+50ms, on CB on supply side, not required on the first one in the chain.
Area 1
RELAY
1a
RELAY
1b
ZSO
ZSO
1a
1b
RELAY
1
ZSI
1
ZSO
1
Area 2
Area n
○
○
○
○
RELAY
2
ZSI
2
ZSO
2
RELAY
0
ZSI
0
RELAY
n
ZSI
n
ZSO
n
○
○
○
○
13.2.9.4
Protection “I”
The protection is enabled/disabled from the menu.
In the case where zone selectivity "S" is active, during the trip of the relay for "I", the ZSO output signal is activated in any case to guarantee correct
operation of the relay on the supply side (and on the load side).
13.2.9.4.1 Start-up threshold “I”
The start-up function can be selected.
The function can be enabled from the menu on the protection "I" page.
The function behaves in exactly the same way as the protection "S" (see par. 13.2.9.2.2).
13.2.9.5
Protection against closing on short-circuit “MCR”
The MCR can be used to protect the system from any closing on short-circuit.
This protection goes on when the CB is closed, within a time window ranging from 40 to 500ms and with a threshold as set by customer, using
the same algorithm as protection I. This protection can be disabled and is an alternative to protection “I”.
This function can be activated through a hand-held PR010/T unit via an SD-Testbus2, SD-Pocket software or through a remote system via the system
bus. This function has one single fixed-time protection curve.