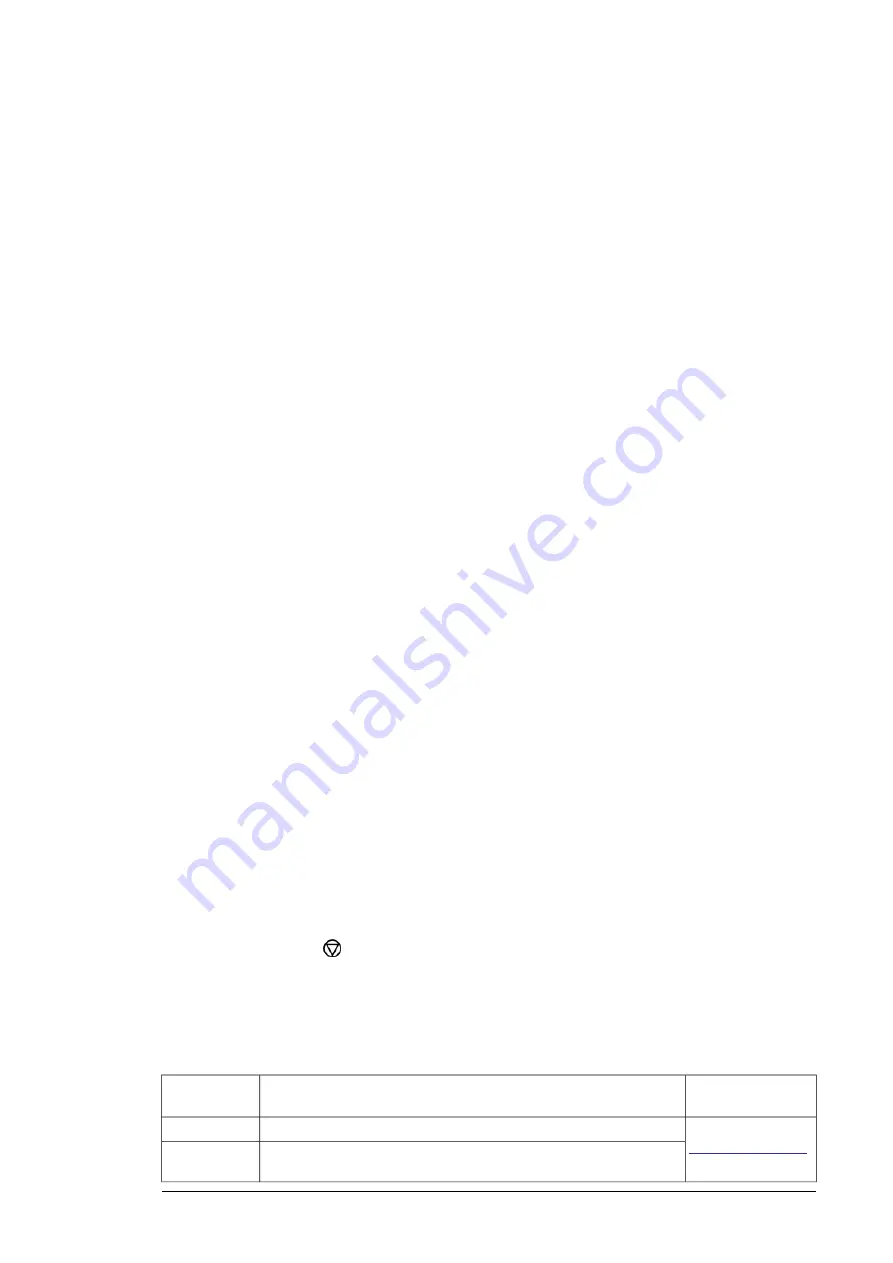
■
Protecting the motor against thermal overload
According to regulations, the motor must be protected against thermal overload and the
current must be switched off when overload is detected. The drive includes a motor thermal
protection function that protects the motor and switches off the current when necessary.
Depending on a drive parameter value, the function either monitors a calculated temperature
value (based on a motor thermal model) or an actual temperature indication given by motor
temperature sensors. The user can tune the thermal model further by feeding in additional
motor and load data.
The most common temperature sensors are:
•
motor sizes IEC180…225: thermal switch, eg. Klixon
•
motor sizes IEC200…250 and larger: PTC or Pt100.
See the firmware manual for more information on the motor thermal protection, and the
connection and use of the temperature sensors.
Protecting the drive against ground faults
The drive is equipped with an internal ground fault protective function to protect the unit
against ground faults in the motor and motor cable in TN (grounded) networks. This is not
a personnel safety or a fire protection feature. The ground fault protective function can be
disabled with a parameter, refer to the firmware manual.
An optional ground fault monitoring device (+Q954) is available for IT (ungrounded) systems.
The option includes a ground fault indicator on the drive cabinet door.
■
Residual current device compatibility
The drive is suitable to be used with residual current devices of Type B.
Note:
The drive contains capacitors connected between the main circuit and the frame. These
capacitors and long motor cables increase the ground leakage current and may cause fault
current circuit breakers to function.
Implementing the emergency stop function
You can order the drive with a category 0 or category 1 emergency stop function.
For safety reasons, install the emergency stop devices at each operator control station and
at other operating stations where emergency stop may be needed.
Note:
Pressing the stop key
on the control panel of the drive, or turning the operating switch
of the drive from position “1” to “0” does not generate an emergency stop of the motor or
separate the drive from dangerous potential.
See the appropriate emergency stop user’s manual for the wiring, start-up and operation
instructions.
Manual code
(English)
User’s manual
Option code
Emergency stop, stop category 0 (using main contactor/breaker)
+Q951
Emergency stop, stop category 0 (using main contactor/breaker) with
push button monitoring
+Q951+Q984
Guidelines for planning the electrical installation 77
Summary of Contents for ACS880-07CLC
Page 1: ...ABB industrial drives Hardware manual ACS880 07CLC drives ...
Page 2: ......
Page 4: ......
Page 64: ...64 ...
Page 82: ...82 ...
Page 91: ...PE PE 10 13 12 22 Electrical installation 91 ...
Page 122: ...122 ...
Page 124: ...124 ...
Page 132: ...5 4 11 7 6 8 132 Maintenance ...
Page 133: ...14 15 16 12 13 17 Maintenance 133 ...
Page 141: ...5 Set the real time clock Maintenance 141 ...
Page 142: ...142 ...
Page 150: ...150 ...
Page 176: ...ACS880 07CLC 0390A 7 C121 marine construction 176 Dimensions ...
Page 177: ...ACS880 07CLC 1310A 7 Dimensions 177 ...
Page 178: ...ACS880 07CLC 2180A 7 C121 marine construction 178 Dimensions ...
Page 179: ...ACS880 07CLC 3260A 7 C121 marine construction Dimensions 179 ...
Page 181: ... 2 D8D Dimensions 181 ...
Page 182: ... 3 D8D 182 Dimensions ...
Page 183: ... 4 D8D Dimensions 183 ...
Page 185: ...Inverter module cubicle with two R8i modules bottom cable exit Dimensions 185 ...
Page 186: ...Inverter module cubicle with three R8i modules bottom cable exit 186 Dimensions ...
Page 187: ...Brake chopper cubicle D150 Dimensions 187 ...
Page 188: ...188 ...
Page 202: ...202 ...
Page 211: ......
Page 212: ......
Page 214: ...Contact us www abb com drives 3AXD50000131457 Rev A EN EFFECTIVE 2018 03 09 3AXD50000131457A ...