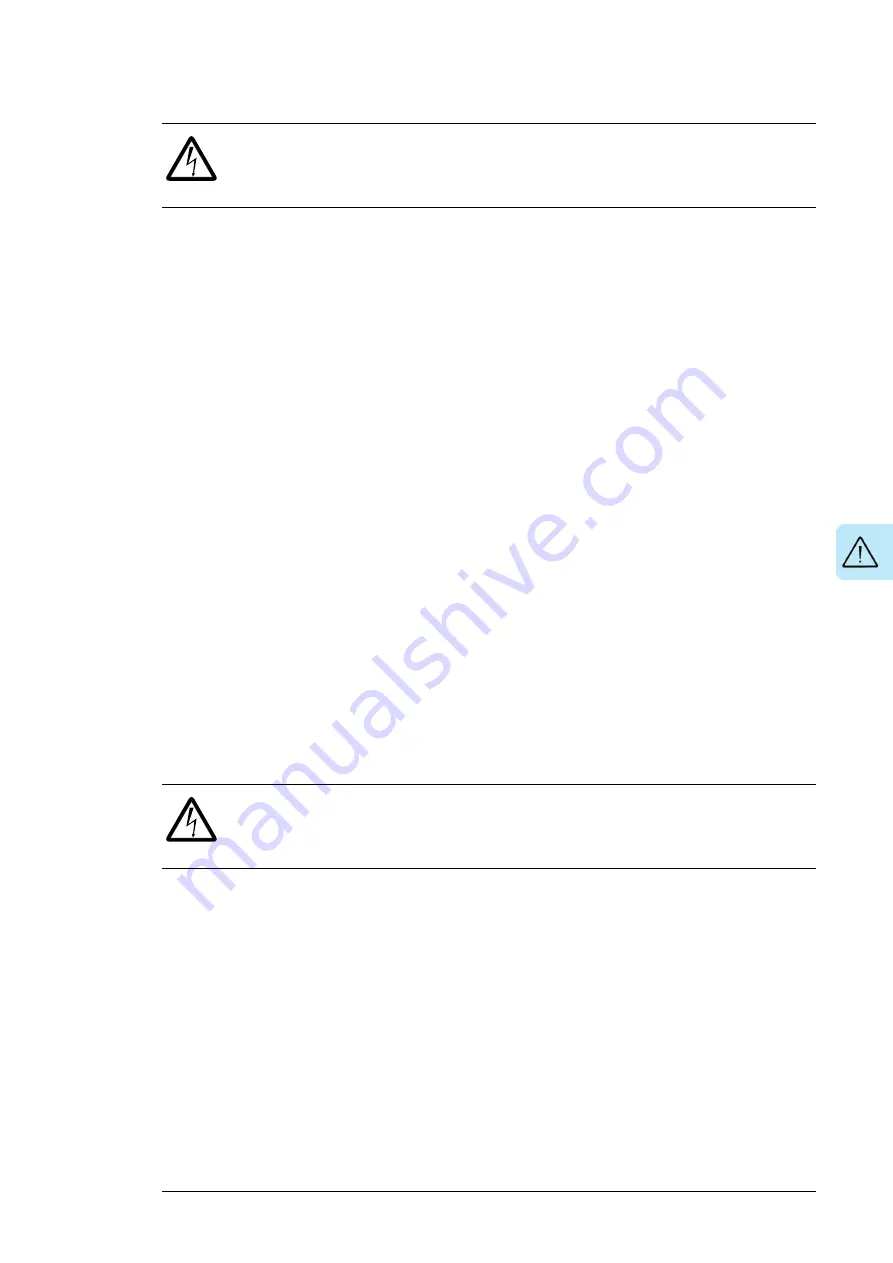
WARNING!
Obey these instructions. If you ignore them, injury or death, or equipment
malfunction can occur, and electromagnetic interference can increase.
•
If you are not a qualified electrician, do not do grounding work.
•
Always ground the drive, the motor and adjoining equipment. This is necessary for the
personnel safety. Proper grounding also reduces electromagnetic emission and
interference.
•
Make sure that the conductivity of the grounding conductors is sufficient. See the
electrical planning instructions of the drive. Obey the local regulations.
•
Connect the power cable shields to protective earth (PE) of the drive to make sure of
personnel safety.
•
Make a 360° grounding of the power and control cable shields at the cable entries to
suppress electromagnetic disturbances.
•
In a multiple-drive installation, connect each drive separately to the protective earth
(PE) busbar of the switch board or the supply transformer.
Note:
•
You can use power cable shields as grounding conductors only when their conductivity
is sufficient.
•
As the normal touch current of the drive is higher than 3.5 mA AC or 10 mA DC, you
must use a fixed protective earth connection. The minimum size of the protective earthing
conductor must comply with the local safety regulations for high protective earthing
conductor current equipment. See standard IEC/EN 61800-5-1, 4.3.5.5.2.
Additional instructions for permanent magnet motor drives
■
Safety in installation, start-up, maintenance
These are additional warnings concerning permanent magnet motor drives. The other safety
instructions in this chapter are also valid.
WARNING!
Obey these instructions. If you ignore them, injury or death and damage to the
equipment can occur.
•
Do not do work on the drive when the permanent magnet motor is rotating. A rotating
permanent magnet motor energizes the drive including its input power terminals.
Before installation, start-up and maintenance work on the drive:
•
Stop the drive and do the steps in section
Electrical safety precautions (page 16)
•
Disconnect the motor from the drive with a safety switch or by other means.
•
If you cannot disconnect the motor, make sure that the motor cannot rotate during work.
Make sure that no other system, like hydraulic crawling drives, can rotate the motor
directly or through any mechanical connection like felt, nip, rope, etc.
•
Measure that the installation is de-energized.
•
Install temporary grounding to the drive output terminals (U2, V2, W2). Connect the
output terminals together as well as to the PE.
Safety instructions 19
Summary of Contents for ACS880-07CLC
Page 1: ...ABB industrial drives Hardware manual ACS880 07CLC drives ...
Page 2: ......
Page 4: ......
Page 64: ...64 ...
Page 82: ...82 ...
Page 91: ...PE PE 10 13 12 22 Electrical installation 91 ...
Page 122: ...122 ...
Page 124: ...124 ...
Page 132: ...5 4 11 7 6 8 132 Maintenance ...
Page 133: ...14 15 16 12 13 17 Maintenance 133 ...
Page 141: ...5 Set the real time clock Maintenance 141 ...
Page 142: ...142 ...
Page 150: ...150 ...
Page 176: ...ACS880 07CLC 0390A 7 C121 marine construction 176 Dimensions ...
Page 177: ...ACS880 07CLC 1310A 7 Dimensions 177 ...
Page 178: ...ACS880 07CLC 2180A 7 C121 marine construction 178 Dimensions ...
Page 179: ...ACS880 07CLC 3260A 7 C121 marine construction Dimensions 179 ...
Page 181: ... 2 D8D Dimensions 181 ...
Page 182: ... 3 D8D 182 Dimensions ...
Page 183: ... 4 D8D Dimensions 183 ...
Page 185: ...Inverter module cubicle with two R8i modules bottom cable exit Dimensions 185 ...
Page 186: ...Inverter module cubicle with three R8i modules bottom cable exit 186 Dimensions ...
Page 187: ...Brake chopper cubicle D150 Dimensions 187 ...
Page 188: ...188 ...
Page 202: ...202 ...
Page 211: ......
Page 212: ......
Page 214: ...Contact us www abb com drives 3AXD50000131457 Rev A EN EFFECTIVE 2018 03 09 3AXD50000131457A ...