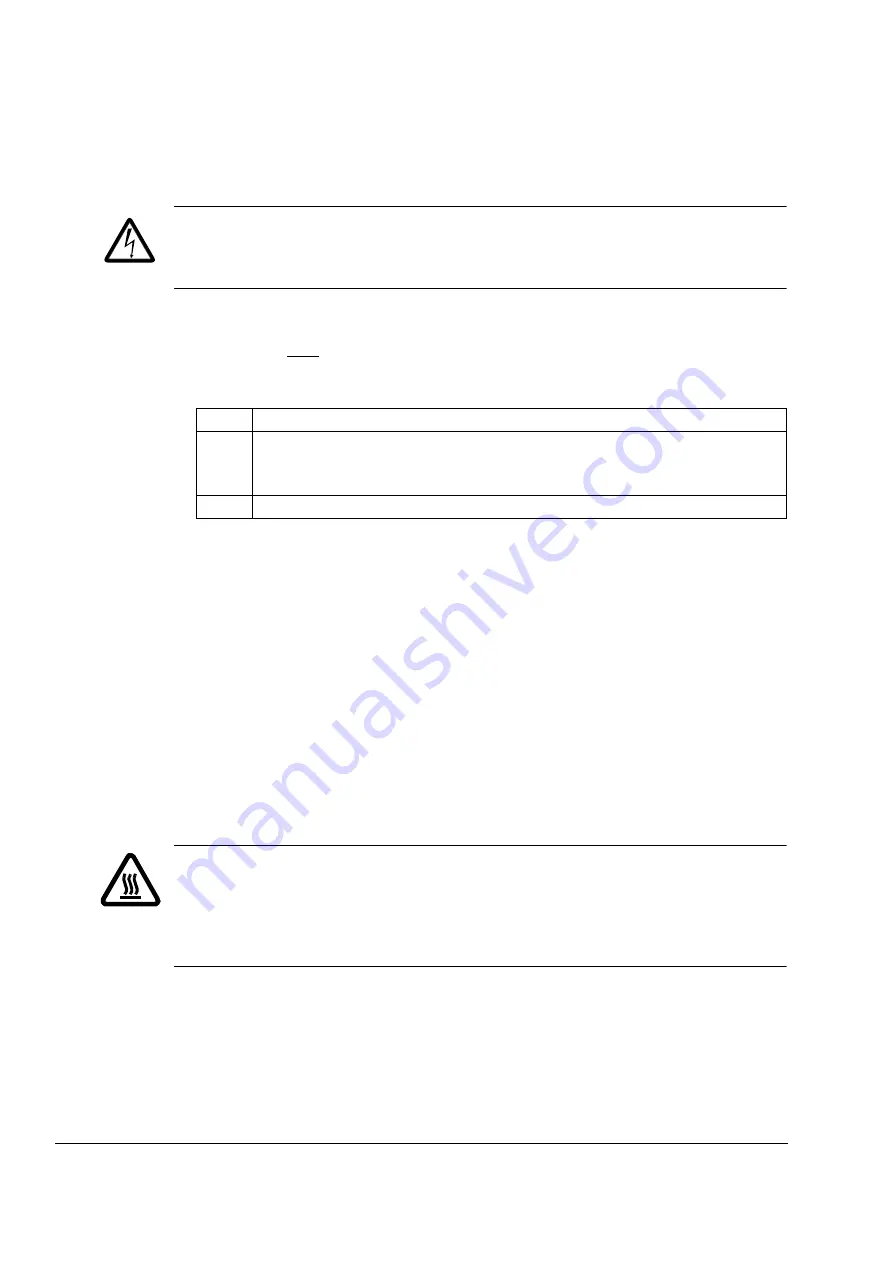
Resistor braking
156
A resistor other than the standard resistor can be used provided that:
• its resistance is not lower than the resistance of the standard resistor
WARNING!
Never use a brake resistor with a resistance below the value specified
for the particular drive / brake chopper / resistor combination. The drive and the
chopper are not able to handle the overcurrent caused by the low resistance.
• the resistance does not restrict the braking capacity needed, ie,
where
• the heat dissipation capacity
(E
R
) is sufficient for the application, see step 3
above.
Placing the brake resistors
All resistors must be installed outside the drive module in a place where they will
cool and the maximum allowed cable length (10 m [33 ft]) is not exceeded.
Arrange the cooling of the resistor in a way that:
• no danger of overheating is caused to the resistor or nearby materials
• the temperature of the room the resistor is located in does not exceed the allowed
maximum.
Supply the resistor with cooling air/water according to the resistor manufacturer’s
instructions.
WARNING!
The materials near the brake resistor must be non-flammable. The
surface temperature of the resistor is high. Air flowing from the resistor is of
hundreds of degrees Celsius. If the exhaust vents are connected to a ventilation
system, ensure that the material withstands high temperatures. Protect the resistor
against contact.
P
max
Maximum power generated by the motor during braking
U
DC
Voltage over the resistor during braking, eg,
1.35 · 1.2 · 415 V DC when supply voltage is 380 to 415 VAC
1.35 · 1.2 · 500 V DC when supply voltage is 440 to 500 VAC
R
Resistor resistance (ohm)
P
max
<
U
DC
R
2
Summary of Contents for ACS850-04 series
Page 1: ...ABB machinery drives Hardware manual ACS850 04 drive modules 160 to 560 kW 200 to 700 hp ...
Page 4: ......
Page 12: ...Table of contents 12 ...
Page 20: ...Safety instructions 20 ...
Page 26: ...Introduction to the manual 26 ...
Page 81: ...Installation 81 Assembly drawing frame G1 3AUA0000132078 ...
Page 82: ...Installation 82 Assembly drawing frame G2 3AUA0000132062 ...
Page 83: ...Installation 83 Assembly drawing air baffles 3AUA0000132062 ...
Page 92: ...Installation 92 3 6a 6b 5 4 8 4 8 6a 6b 7a 7b 7b ...
Page 112: ...Installation checklist 112 ...
Page 114: ...Start up 114 ...
Page 116: ...Fault tracing 116 ...
Page 140: ...Technical data 140 ...
Page 142: ...Dimension drawings 142 Frame G1 Drive module dimensions ...
Page 143: ...Dimension drawings 143 Frame G1 Drive module dimensions with optional cabling panels H381 ...
Page 144: ...Dimension drawings 144 ...
Page 145: ...Dimension drawings 145 Frame G1 Cabling panels H383 installed into a Rittal TS 8 cabinet ...
Page 146: ...Dimension drawings 146 Frame G2 Drive module dimensions ...
Page 147: ...Dimension drawings 147 Frame G2 Drive module dimensions with optional cabling panels H381 ...
Page 148: ...Dimension drawings 148 ...
Page 149: ...Dimension drawings 149 Frame G2 Cabling panels H383 installed into a Rittal TS 8 cabinet ...
Page 150: ...Dimension drawings 150 Frames G1 and G2 Bottom plate 3AUA0000082240 ...
Page 151: ...Dimension drawings 151 Frames G1 and G2 Air baffles 3AUA0000138986 ...
Page 152: ...Dimension drawings 152 ...
Page 162: ...du dt filters 162 ...
Page 164: ...3AUA0000081249 Rev C EN 2013 04 11 Contact us www abb com drives www abb com drivespartners ...