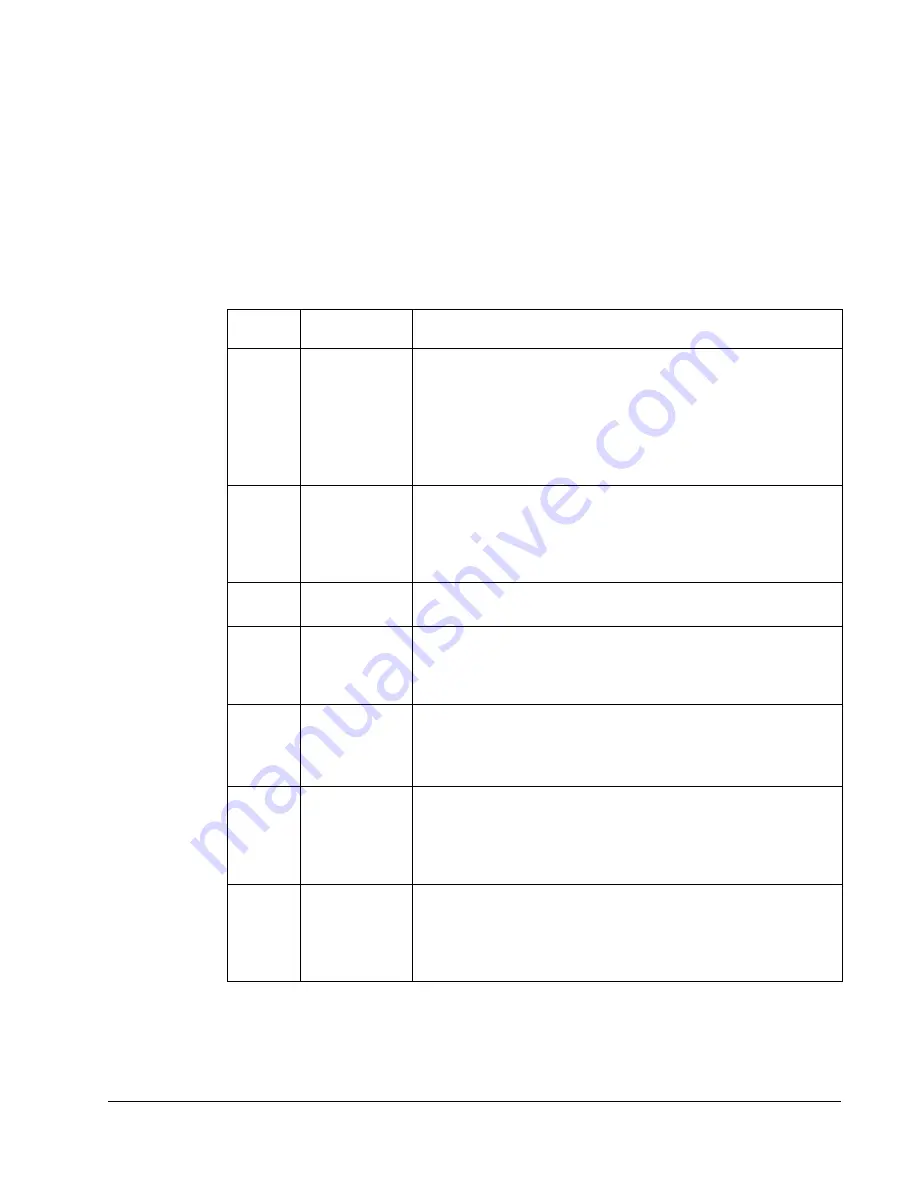
ACH550 Installation, Operation and Maintenance Manual
29
ACH550-UH
To clear the fault history (all of the Group 04, Fault History parameters):
1. Using the control panel in Parameters mode, select parameter 0401.
2. Press EDIT.
3. Press UP and Down simultaneously.
4. Press SAVE.
Alarm listing
The following table lists the alarms by code number and describes each.
Alarm
Code
Display
Description
2001
OVERCURRENT
Current limiting controller is active. Check for and correct:
• Excessive motor load.
• Insufficient acceleration time (parameters 2202
ACCELER
TIME
1 and
2205
ACCELER
TIME
2).
• Faulty motor, motor cables or connections.
• Output disconnect device not interlocked.
• Interaction with external input filter.
2002
OVERVOLTAGE
Over voltage controller is active. Check for and correct:
• Static or transient overvoltages in the input power supply.
• Insufficient deceleration time (parameters 2203
DECELER
TIME
1 and
2206
DECELER
TIME
2).
• Interaction with external input filter.
2003
UNDERVOLTAGE
Under voltage controller is active. Check for and correct:
• Undervoltage on mains.
2004
DIR
LOCK
The change in direction being attempted is not allowed. Either:
• Do not attempt to change the direction of motor rotation, or
• Change parameter 1003
DIRECTION
to allow direction change (if
reverse operation is safe).
2005
I
/
O
COMM
Fieldbus communication has timed out. Check for and correct:
• Fault setup (3018
COMM
FAULT
FUNC
and 3019
COMM
FAULT
TIME
).
• Communication settings (Group 51 or 53 as appropriate).
• Poor connections and/or noise on line.
2006
AI
1
LOSS
Analog input 1 is lost, or value is less than the minimum setting.
Check:
• Input source and connections
• Parameter that sets the minimum (3021)
• Parameter that sets the Alarm/Fault operation (3001)
2007
AI
2
LOSS
Analog input 2 is lost, or value is less than the minimum setting.
Check:
• Input source and connections
• Parameter that sets the minimum (3022)
• Parameter that sets the Alarm/Fault operation (3001)