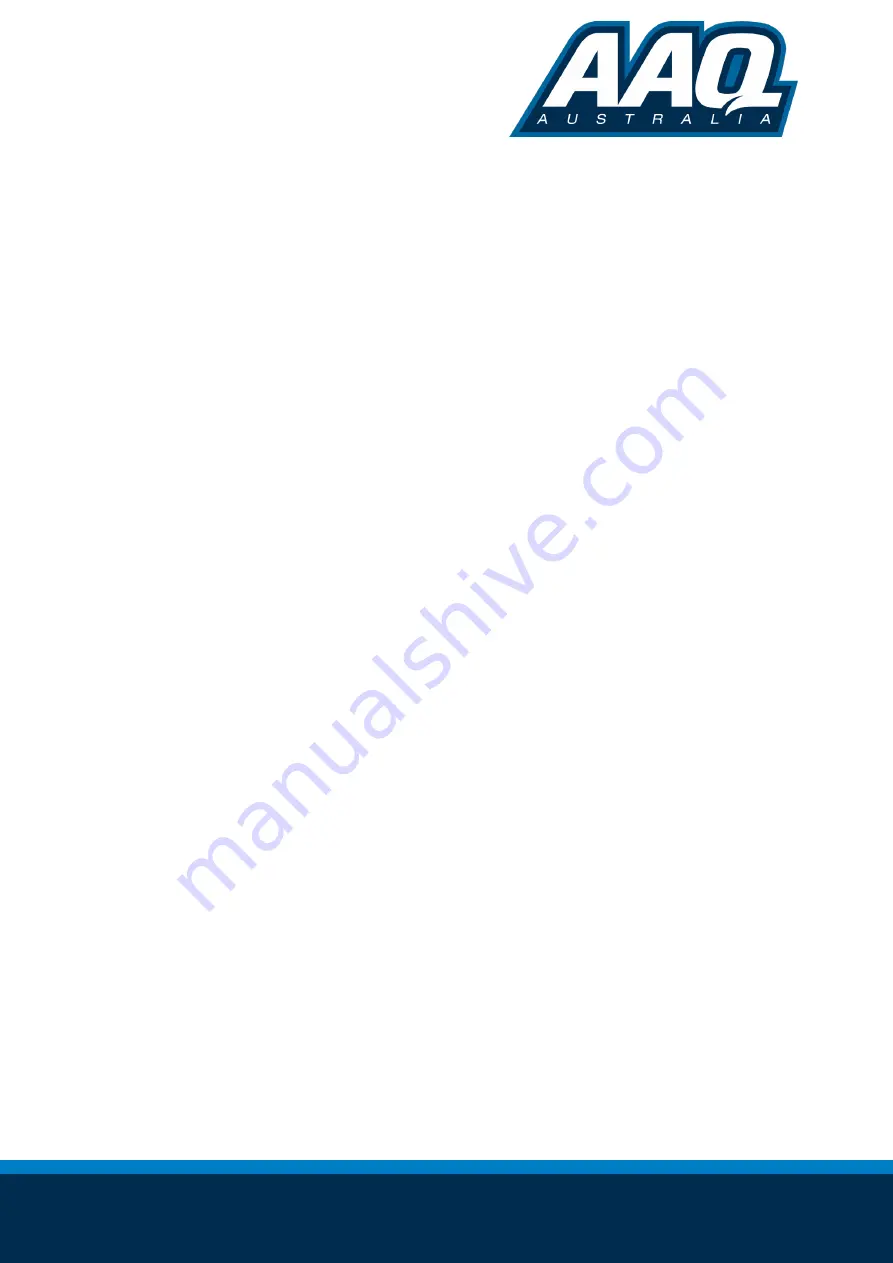
Advance AutoQuip
2 McDonald Crescent | Bassendean WA 6054
Ph: 08 9279 1663 | Fax: 08 9279 1667 | E: [email protected] | W: www.aaq.net.au
ADVANCE AUTOQUIP WARRANTY
GENERAL WARRANTY INFORMATION:
ADVANCE AUTOQUIP’S OBLIGATION UNDER THIS WARRANTY IS LIMITED TO REPAIRING OR
REPLACING ANY PART OR PARTS RETURNED TO THIS FACTORY, TRANSPORTATION CHARGES
PREPAID, WHICH PROVE UPON INSPECTION TO BE DEFECTIVE AND WHICH HAVE NOT BEEN
MISUSED. DAMAGE OR FAILURE TO ANY PART DUE TO FREIGHT DAMAGE OR LACK OF
MAINTENANCE IS NOT COVERED UNDER THIS WARRANTY. ADVANCE AUTOQUIP RESERVES THE
RIGHT TO DECLINE RESPONSIBILITY WHEN REPAIRS HAVE BEEN MADE OR ATTEMPTED BY OTHERS,
OR WHERE NON GENUINE PARTS HAVE BEEN USED. THIS WARRANTY DOES NOT COVER
DOWNTIME EXPENSES INCURRED WHEN UNIT IS IN REPAIR. ADVANCE AUTOQUIP ARE NOT LIABLE
FOR POSSIBLE ISSUES, DAMAGES, ACCIDENTS ETC RESULTING FROM FAILURE TO FOLLOW THE
OPERATION OR INSTALLATION INSTUCTIONS CONTAINED IN THE MANUAL OR ON THE EQUIPMENT.
THE MODEL NAME AND SERIAL NUMBER OF THE EQUIPMENT MUST BE PROVIDED WITH ALL
WARRANTY CLAIMS. THIS WARRANTY STATEMENT CONTAINS THE ENTIRE AGREEMENT BETWEEN
ADVANCE AUTOQUIP AND THE PURCHASER UNLESS OTHERWISE SPECIFICALLY EXPRESSED IN
WRITING. THIS NON-TRANSFERABLE WARRANTY APPLIES TO THE ORIGINAL PURCHASER ONLY. THIS
WARRANTY IS APPLICABLE TO UNITS LOCATED ONLY IN AUSTRALIA. CONTACT ADVANCE
AUTOQUIP FOR SPECIFIC WARRANTY PROVISIONS FOR UNITS LOCATED OUTSIDE OF THESE
COUNTRIES.
NOTE: THE EQUIPMENT IS NOT TO BE USED FOR WASH DOWN PURPOSES OR TO BE INSTALLED IN AN
OUTDOOR ENVIRONMENT WHERE IT IS SUBJECT TO WEATHER OR WATER DAMAGE. WARRANTY
WILL BE IMMEDIATELY VOID.
STRUCTURAL COMPONENTS:
ALL STRUCTURAL AND MECHANICAL COMPONENTS OF THIS UNIT ARE GUARANTEED FOR A
PERIOD OF FIVE YEARS, FROM THE DATE OF INVOICE, AGAINST DEFECTS IN WORKMANSHIP
AND/OR MATERIALS
WHEN LIFT IS INSTALLED AND USED ACCORDING TO RECOMMENDATIONS.
POWER UNIT:
POWER UNIT COMPONENTS (PUMP AND RESERVOIR) ARE GUARANTEED A PERIOD OF ONE YEAR,
FROM THE DATE OF INVOICE, AGAINST DEFECTS IN WORKMANSHIP AND/OR MATERIALS WHEN
THE LIFT IS INSTALLED AND USED ACCORDING TO RECOMMENDATIONS.
ELECTRICAL COMPONENTS:
ALL ELECTRICAL COMPONENTS (INCLUDING MOTOR) ARE GUARANTEED A PERIOD OF ONE YEAR
FOR PARTS ONLY (EXCLUDING LABOR), FROM THE DATE OF INVOICE, AGAINST DEFECTS IN
WORKMANSHIP AND/OR MATERIALS WHEN THE LIFT IS INSTALLED AND USED ACCORDING TO
RECOMMENDATIONS.
PNEUMATIC (AIR) COMPONENTS:
ALL PNEUMATIC (AIR) COMPONENTS (I.E. AIR CYLINDERS AND POPPET AIR VALVES) ARE
GUARANTEED FOR ONE YEAR FOR PARTS ONLY (EXCLUDING LABOR), FROM THE DATE OF
INVOICE, AGAINST DEFECTS IN WORKMANSHIP AND/OR MATERIALS WHEN THE LIFT IS INSTALLED
AND USED ACCORDING TO RECOMMENDATIONS.
EXCLUSIONS:
WARRANTY DOES NOT INCLUDE CONSUMABLE ITEMS SUCH AS HYDRAULIC OIL, LIFTING PADS, OIL
SEALS, VEE BELTS AND SLIDING BLOCKS.
THIS WARRANTY SUPERSEDES ALL OTHER WARRANTY POLICIES PREVIOUSLY STATED AND IN ALL OTHER ADVANCE AUTOQUIP’s
PRODUCT SPECIFIC LITERATURE.
Summary of Contents for AutoLift AL-3000AG
Page 22: ...Installation Operation and Parts Manual 22 Three phase AL 3000AG FL 8801 ...
Page 23: ...Installation Operation and Parts Manual 23 AL 3000AG FL 8801 ...
Page 24: ...Installation Operation and Parts Manual 24 AL 3000AG FL 8801 ...
Page 25: ...Installation Operation and Parts Manual 25 AL 3000AG FL 8801 ...
Page 27: ...Installation Operation and Parts Manual 27 AL 3000AG FL 8801 For mechanical assembly ...