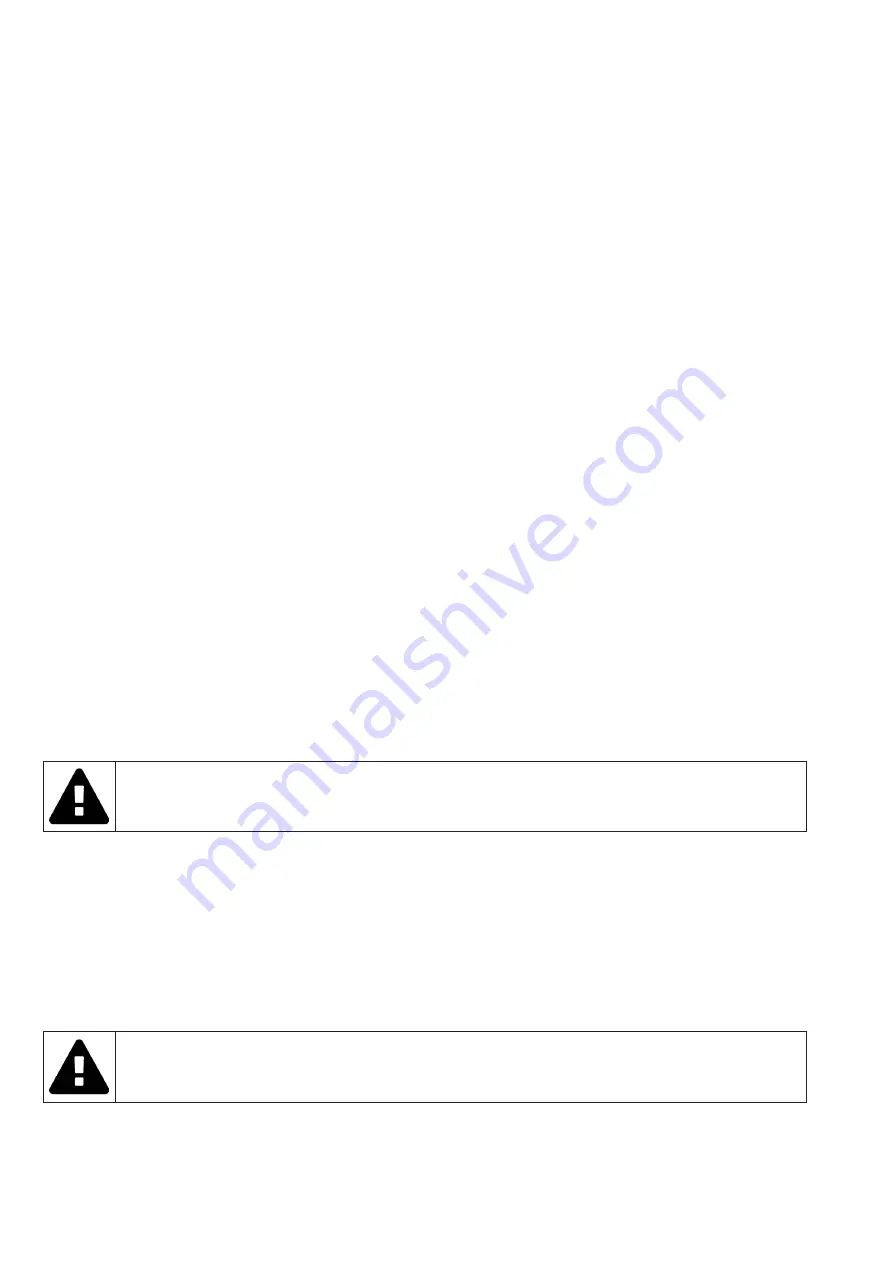
10
T2300-T2350-T2400-T2450 Double Mitre Saw
3. SAFETY
3.1 GENERAL WARNINGS
• The manufacturer, during the design and manufacturing stages, has paid special attention to the aspects that
might jeopardize the safety and health of the personnel that operates the machinery. As well as the compliance
with current regulation on the matter, the manufacturer has adopted all the “rules of good craftsmanship”. The
purpose of this information is to make the user aware to pay special attention in order to foresee any risk. There
is no substitute for carefulness. Safety also lies in the hands of all operators that work on the machinery.
• Carefully read the instructions of the manual supplied with the machinery and the ones directly fitted on the
machinery, especially the ones concerning safety. Time dedicated to the study of this manual will prevent
unpleasant accidents; it is always too late to remember what should have been done when it has already
happened.
• Pay attention to the meaning of the symbols of the plates fitted on the machinery; their shape and colour are
important for safety purposes. Keep them readable and comply with their information.
• Do not tamper with, do not dodge, eliminate or bypass the safety devices installed on the machinery. The non-
compliance with this requirement may cause serious risks for personnel’s safety and health.
• The personnel that carries out any type of operation during the entire useful life of the machinery must have
specific technical competence, special skills and experience acquired and acknowledged in the specific sector.
The lack of these requisites may jeopardize the safety and health of personnel.
• During operation only use the personal protection clothes and/or devices listed in the instructions supplied by
the manufacturer and the ones provided for by current regulations on safety at work.
• During the normal use or for any intervention, keep the surrounding area in adequate condition, especially the
one accessing the controls, in order to avoid jeopardizing the safety and health of personnel.
• The operator, as well as being adequately informed on the use of machinery, must possess skills and competence
adequate to the type of working activity to perform.
• The machine must only be used for the applications intended by the manufacturer. Only use the machinery for
the purposes intended by the manufacturer. The employment of the machinery for improper uses may cause
risks to the safety and the health of personnel and economic loss.
• Provide appropriate containers to stock the pieces you will be working with.
• Disconnect the main air supply and the power supply.
• Keep your foot off of the pedal during machine maintenance
3.2 PROPER USE
The machine is only intended for manual operation (under the direct control of the operator).
The machine has been designed and manufactured for cutting to 45 degrees wooden stick, its derivatives, plastic
or light alloys.
For cutting light alloys is necessary:
• To equip the machine with Mist Spray Cooling System
• To use proper blades
3.3 INADVISABLE USE
The machine has not to be used:
• For uses different from those listed in 3.2 paragraph
• In explosive or aggressive atmosphere, at high density of dust or oily substances suspended in the air
• In flammable atmosphere
• Outside in all weather severity
• With disconnected electromagnetic interblocks
• With electric bridges and/or mechanical instruments leaving out machine parts or functions
• For working materials not suitable with machine characteristics
It is absolutely forbidden to cut different materials (glass, ceramic. etc..) in particular irony (or
similar) materials.
3.4 DANGEROUS AREAS
The area of blades operating, is defined “working area” (A).
The dangerous areas of the machine, include the mobile
parts and surrounding zones (B)
Summary of Contents for T2 Series
Page 3: ...3 Double Mitre Saw T2300 T2350 T2400 T2450...
Page 37: ...37 Double Mitre Saw T2300 T2350 T2400 T2450 ATTACHMENT A MACHINE OVERALL DIMENSIONS...
Page 38: ...38 T2300 T2350 T2400 T2450 Double Mitre Saw ATTACHMENT B MECHANIC SCHEMATICS PRELIMINARY...
Page 39: ...39 Double Mitre Saw T2300 T2350 T2400 T2450...
Page 40: ...40 T2300 T2350 T2400 T2450 Double Mitre Saw...
Page 41: ...41 Double Mitre Saw T2300 T2350 T2400 T2450...
Page 42: ...42 T2300 T2350 T2400 T2450 Double Mitre Saw...
Page 44: ...44 T2300 T2350 T2400 T2450 Double Mitre Saw ATTACHMENT D ELECTRIC SCHEMATICS...
Page 45: ...45 Double Mitre Saw T2300 T2350 T2400 T2450 ATTACHMENT E PLATES DISLOCATION PRELIMINARY...