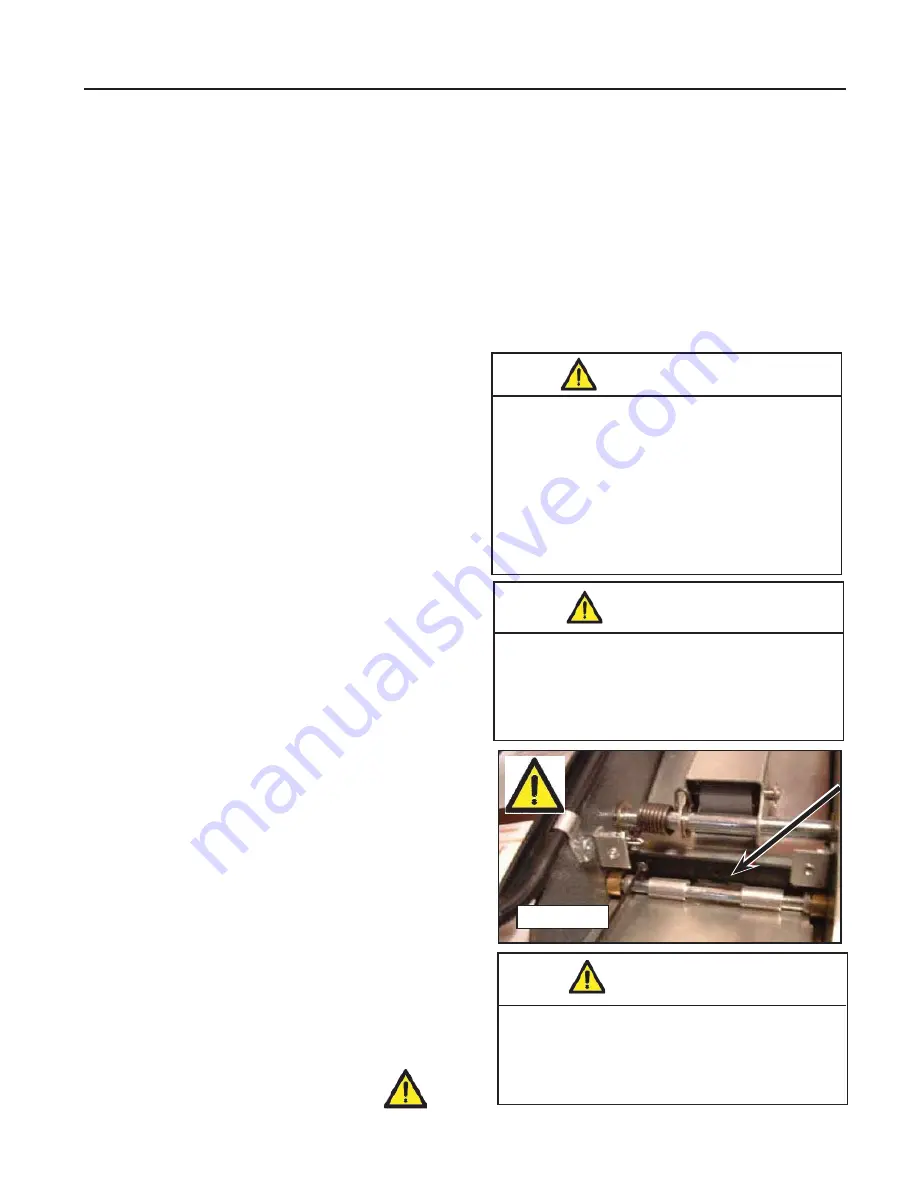
5
2011 October
WaterAct-M-S
1-SAFETY
3.2.4 How to Update the Manual in Case of
Modif
i
cations to the Dispenser
Modi
fi
cations to the dispenser are subject to manufac-
turer’s internal procedures. The user receives a com-
plete and up-to-date copy of the manual together with
the dispenser. Afterwards the user may receive pages
or parts of the manual which contain amendments or
improvements made after its
fi
rst publication. The user
must use them to update this manual.
3.3 Table of Warnings
3.1 How to Read and Use the Service Manual
This instruction manual covers safety aspects,
handling and transport, storage, unpacking, prepara-
tion, installation, operation, set-up and adjustments,
technical and manufacturing speci
fi
cations, mainte-
nance, troubleshooting, repair work and servicing,
electric diagrams, warranty information, disposal, a
de
fi
nition of symbols, plus a parts list of the 3M Wa-
ter Activated Tape Dispenser (manual version) 3M
Industrial Adhesives and Tapes Division 3M Center,
Bldg. 220-5E-06 St. Paul, MN 55144-1000 (USA) /
Edition October 2011 / Copyright 3M 2011 / All rights
reserved The manufacturer reserves the right to
change the product at any time without notice -
Publication © 3M 2011 44-0009-2107-0.
3.2.1 Importance of the Manual
The manual is an important part of the dispenser; all
information contained herein is intended to enable
the equipment to be maintained in perfect condition
and operated safely. Ensure that the manual is avail-
able to all operators of this equipment and is kept
up to date with all subsequent amendments. Should
the equipment be sold or disposed of, please ensure
that the manual is passed on. Electrical and pneu-
matic diagrams are included in the manual. Equip-
ment using PLC controls and/or electronic compo-
nents will include relevant schematics or programs in
the enclosure and in addition, the relevant documen-
tation will be delivered separately.
3.2.2 Manual Maintenance
Keep the manual in a clean and dry place near the
dispenser. Do not remove, tear, or rewrite parts of
the manual for any reason. Use the manual without
damaging it. If the manual has been lost or dam-
aged, ask your after sale service for a new copy.
3.2.3 Consulting the Manual
The manual is composed of:
- Pages which identify the document and the
dispenser
- Index of the subjects
- Instructions and notes on the dispenser
- Enclosures, drawings and diagrams
- Spare parts (last section)
All pages and diagrams are numbered. The spare
parts lists are identi
fi
ed by the
fi
gure identi
fi
cation
number. All the notes on safety measures or
possible dangers are identi
fi
ed by the symbol:
•
To reduce the risk associated with
mechanical hazards:
−
Read, understand, and follow all safety and
operating instructions before operating or
servicing the tape dispenser.
−
Allow only properly trained and quali
fi
ed
personnel to operate and service this
equipment.
WARNING
•
To reduce the risk associated with
sharp blade hazards:
−
Keep hands and
fi
ngers away from
tape cutoff blades. The blades are
extremely
sharp.
CAUTION
WARNING
Sharp Blade
Figure 3-1
•
To reduce the risk associated with
muscle strain:
−
Use proper body mechanics when
working on or moving the dispenser.
WARNING
Summary of Contents for W100
Page 4: ...4 This Page is Blank ...
Page 6: ...6 This Page is Blank ...
Page 8: ...2 This Page is Blank ...
Page 10: ...4 This Page is Blank ...
Page 14: ...2 2 This Page is Blank ...
Page 58: ...46 This Page is Blank ...