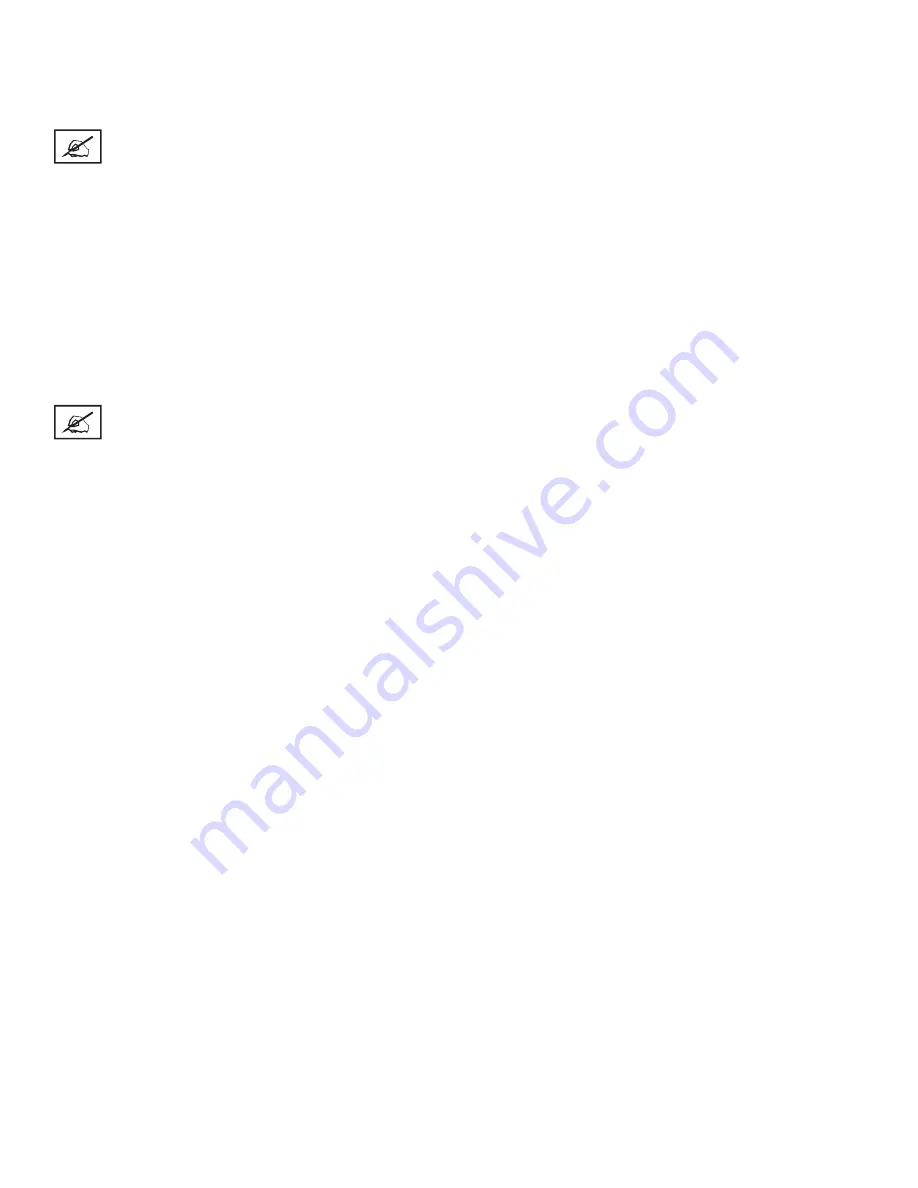
3D Systems, Inc.
47
BREAKING OUT PARTS
When a print completes, you need to remove the sintered parts from the print cake and clean them . Removing parts from the print cake
is called “breakout .” This section describes the procedures you follow when you break out parts .
NOTE: You can find material-specific information about breaking out and cleaning parts in your Material Guide.
Before breakout, you must:
•
Cool down the print cake then remove the part transfer cylinder from the print chamber—or vice-versa .
•
Roll the part transfer cart to the MQC System and unload the print cylinder onto the breakout area .
•
Remove the print cylinder .
•
Remove the surrounding powder from the outline of the parts with a spatula and brush . Ensure the sifter is running, then brush
unsintered print cake powder into the sifter .
•
When you can easily grasp a part, carefully lift it . Gently brush off the parts and place them on the breakout area of the MQC Sys-
tem .
Part Finishing After Breakout
NOTE: Consult your Material Guide for full details on part finishing.
After breakout, remove and dispose of any remaining print cake material from holes and crevices .
Your SLS system ships with a basic set of rough and fine part cleaning tools. You may find it useful to supplement these with other fine
tools, picks, and brushes, such as those used for dental and jewelry work .
3D Systems recommends you also purchase a glass bead blaster (pneumatic blast cabinet). A bead blaster makes fine cleaning much
easier and faster . See your
Facility Guide
for recommended third party suppliers .