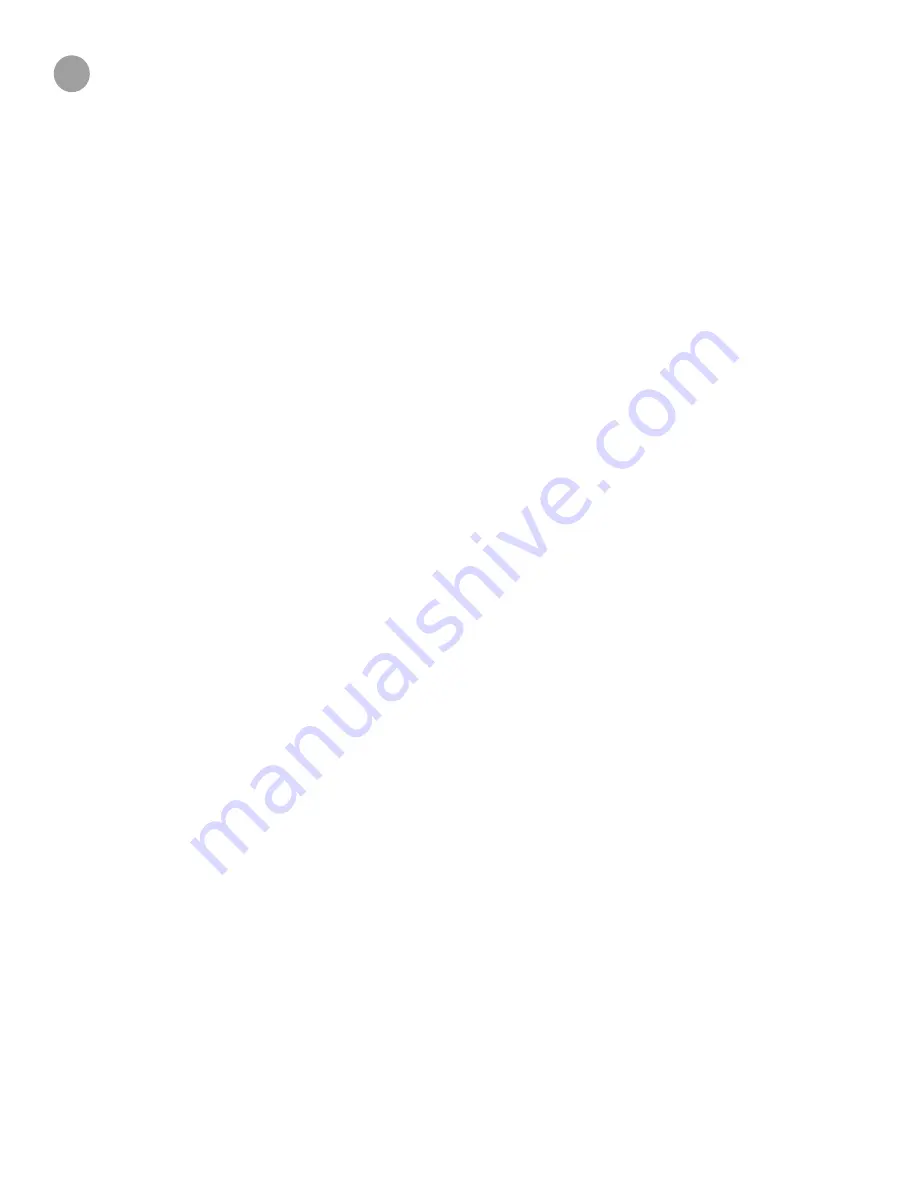
3D Systems, Inc.
31
4
PRINTING PARTS WITH THE PROX 500
This section gives an overview of the part printing process . For detailed information on operating the ProX 500 printer, see the section,
“ProX 500 System Operations” on page 37
. For detailed information on operating the MQC System, see the section
“MQC
System Operations” on page 43
.
The software used to print parts on the ProX 500 printer consists of the
Build Setup
and
Sinter
applications . Build Setup is used to
prepare models for printing . The models are then processed and transferred to the Sinter application which controls the printing of the
parts .
Before printing, several components of the SLS equipment should be cleaned and the MQC System must have transferred material to
the printer .
MQC SYSTEM PREPARATION
The MQC System should be started and filled with material before proceeding. After it has been loaded with material, it will need to
transfer the material to the printer . For detailed information on operating the MQC System .
1 . Turn on the power to the dust collector and MQC System .
a . To turn the dust collector on, simply press the power switch .
b . If the MQC System has not been powered up, press the power switch on the front panel of the system .
2 . Ensure that the system is in “
Stopped
” mode . If the status does not say “Stopped,”
•
Press the knob to navigate to the next screen
•
Select “
Operational mode
”
•
Select “
Stop cycle
”
Load Fresh Material from Material Container
3 . From the Home screen, press the knob to go to the next screen and select “
Operational mode
.”
4 . Select “
Load fresh material
.” The screen will prompt you to scan the tag of the material container on the tag reader .
5 . The tag should be located on the cap of the material container . You can simply remove the cap and scan it across the tag reader .
6 . When the system detects a valid tag, the doors above the interface will unlock .
CLEANING AND CHECKING
Follow these procedures to clean the SLS equipment before you print parts . For detailed cleaning instructions, refer to the sections
indicated .
1 . Clean the print chamber (See the section,
“Cleaning the Print Chamber” on page 57
)
2 . Clean laser window (See the section,
“Cleaning the Laser Window” on page 59
)
3 .
Check the overflow screen which is located at the lower-left side of the ProX 500 and clean, if necessary. (See the section,
“Cleaning and Replacing Filters” on page 63
)
4 .
Check the two-stage filters which are located at the lower-left side of the printer and the back of the MQC System. Clean them if
necessary . (See the section,
“Cleaning and Replacing Filters” on page 63
)
5 . Check the roller and clean any material or debris that may be adhered to it . (See the section,
“Cleaning the Roller Assembly” on
page 59.
)
6 . Clean the print chamber window, if necessary, using a clean dry dust rag . (See the section,
“Cleaning the Print Chamber” on
page 57.
)
7 . Check the heaters and chamber lights inside the print chamber and clean, if necessary . (See the section
“Cleaning the Print
Chamber” on page 57
)
8 .
Check that the coolant flow which is located on the lower-left side of the machine is at least 6 lpm. Also verify that the coolant
temperature on the chiller is 20 °C .
9 . Check to see if the heater assemblies are in the (down) print position . If not, lower the heater assembly into place .
10 .
Close and latch the print chamber door and outer front door. If the chamber door has been unlatched for a significant period of
time, check the IR sensor core temperature before starting a print job . The temperature must be at 77 °C and stable . This can be
checked in the Status settings of the Sinter Status window or Manual Operations Heater screen .
11 . Check the laser window N
2
flow (see Material Guide for correct N
2
flow for your material).
12 . Check the blackbody and clean, if necessary . (See the section,
“Cleaning the Black Body” on page 62
)