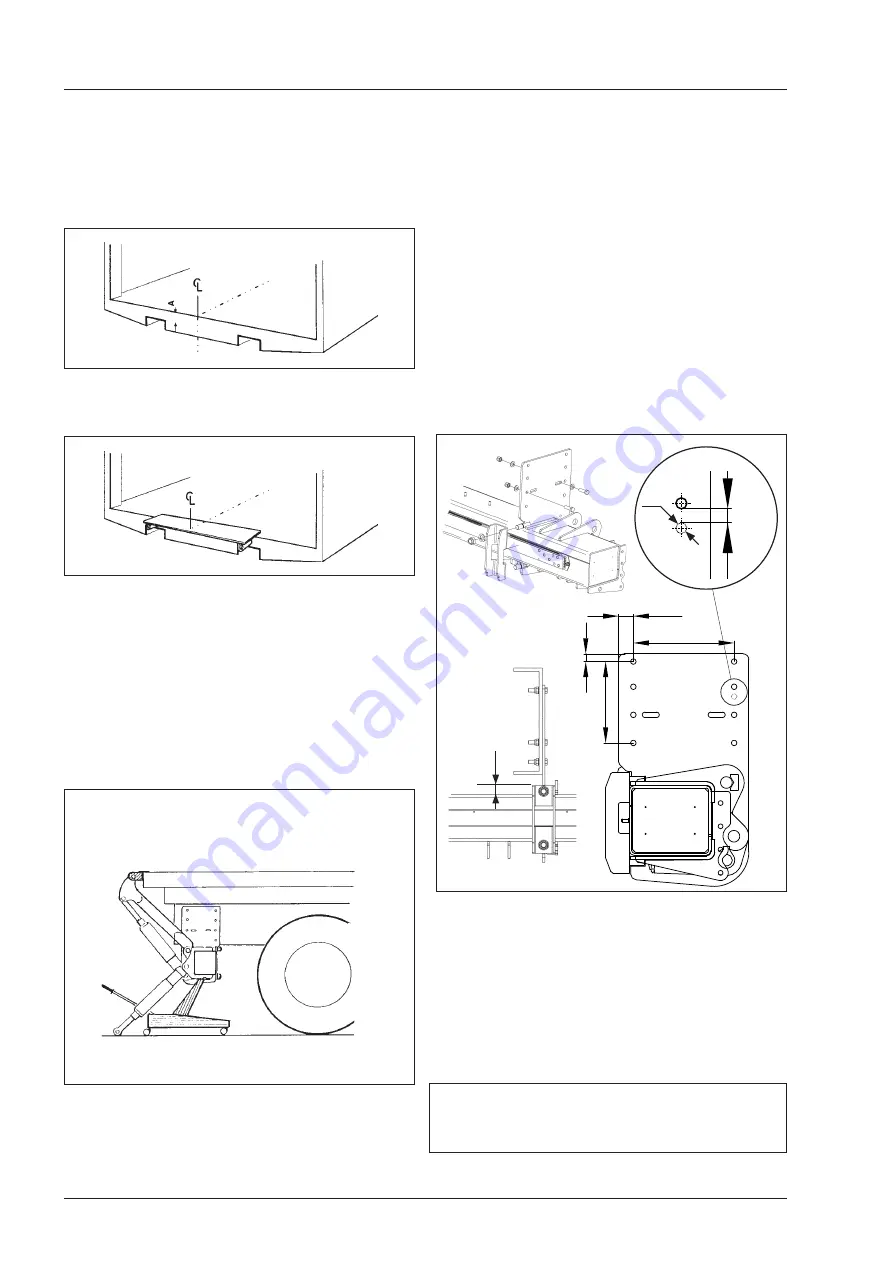
12
35 mm
Min 260
Min 20
Min 180
Min 20
Min D
D
Pict. 2
Pict. 1
Installation jig,
Art. no. 51724 for Z-150/200/250
Art. no. 52312 for ZL-150/200/250
Pict. 3
4. Installation support frame
Preparation/support frame
Attention! Also refer to the truck manufacturer´s instructions for auxiliary equipment
1. Measure out and mark the centre point of the
truck's rear frame.
See picture 1
.
2. Fasten the jig with bolts or spot weld it to the rear
frame so that the middle points line up.
See picture
2
.
3. Make the notches as required in the rear beam in
accordance with the measures on previous pages.
4. Place the support frame of the lift under the frame
of the truck and fit the lift arms to the installation jig.
Use the specified platform pivot bolt.
5. Position the support frame as required under the
truck's chassis frame (a wheeled jack is a good aid).
See picture 3
.
The support frame ought to be positioned as high as
possible. Note the measures on previous pages.
The support frame must be parallel with the chassis
frame, but it must not be pressed against the frame.
There must be some mm between.
If it is difficult to get the support frame into its right posi
-
tion, loosen a hydraulic hose from one lift cylinder to let oil
or air out.
The brackets should be positioned according to picture 4.
Slide the brackets over the support frame so that the ope-
ning points towards the front of the vehicle see picture 4.
If adjustment is necessary, drill
14 mm holes
in the truck
frame in the middle of the oval holes of the bracket. Then
fasten the brackets securely to the frame (torque=115 Nm)
with the delivered
M14x45 10.9 screws
. Washers should
be placed under the screwheads and washers under the
nuts.
Bag 31, 31B. See picture 4.
NB! Welding on the mounting brackets is not allowed.
Install the u-profile end plate with the u pointing to the front
of the vehicle using the washers and nuts provided, one
plate for each mounting bracket, two nuts and two wash-
ers for each plate (torque=260 Nm). After testing the posi-
tion of the lift relative to the chassis, drill the remaining
holes in the frame on each side and fasten the brackets,
min. 6 pcs. M14x45 10.9 115 Nm (this does not include
screws in oval holes).
NB. Do not run the lift up against the armstops during
installation before all the bolts between the mounting
brackets and vehicle frame are tightened.
Note!
Please note that the space for the bracket requires additio-
nal 35 mm between the frame of the truck and the support frame.
See pict. 4
Do not load the lift before all bolts are tightened.
Loosen the installation jig.
Pict. 4
Min 6 pcs.
M14x45 10.9
115 Nm
New hole
Содержание Z 150-135
Страница 2: ......
Страница 9: ...9 Loading Diagram 2 General...
Страница 16: ...16 Z ZL 150 200 250 DA 6 Electric and hydraulic diagram...
Страница 34: ...34 10 Markings decals...